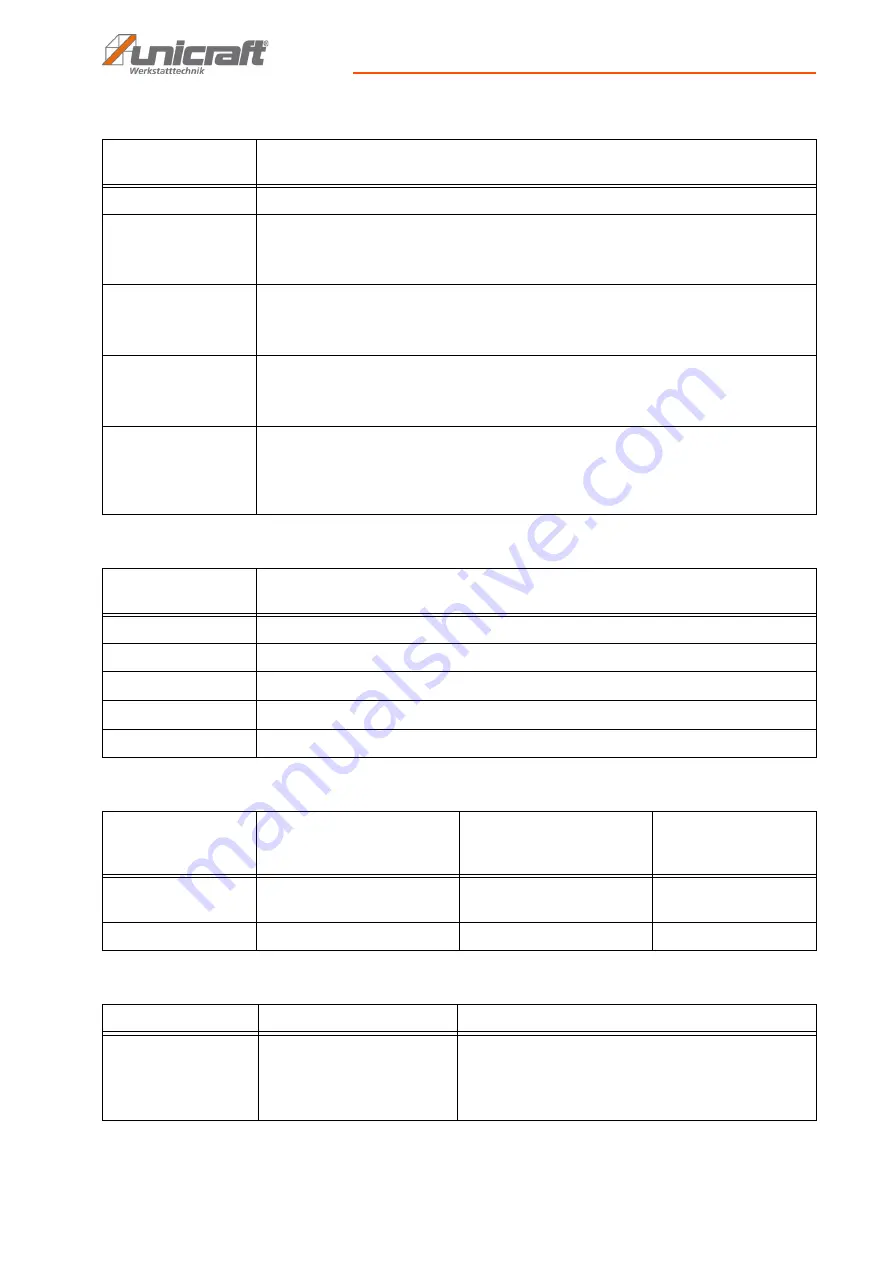
Maintenance and repairs
WPP 15 E | Version 1.02
13
11.2.1Visual inspection
11.2.2 Maintenance tasks
11.2.3Recommended processing materials
11.2.4Lubrication
Maintenance intervals
and operating hours
Maintenance point
Daily
Visual inspection of the hydraulic workshop press for dirt, clean if necessary
Weekly
Visual inspection of the hydraulic workshop press, in particular the press table and support
bolts:
if necessary, replace damaged components or request repairs
Weekly
Visual inspection of the hydraulic workshop press, in particular the functions of the hydrau-
lic components and checking for oil leaks (pump, hoses, cylinders, pressure gauge, etc.):
If necessary, replace damaged components
200
Functional inspection of the entire hydraulic workshop press to verify the machine com-
pletes all steps and operates correctly and safely:
If necessary, request repairs
Annually
Have the hydraulic pipes and connections checked by an authorised person. In the event
of increased usage periods, frequent or increased pressure pulses or severe external influ-
ences the machine must be checked once every six months.
If necessary, have damaged pipes replaced.
Maintenance intervals
and operating hours
Maintenance task
200
Lubricate the hydraulic workshop press (all moving parts, bearings and guides).
300
Change the hydraulic oil.
When necessary
Vent the hydraulic system.
When necessary
Top up hydraulic oil and then vent the hydraulic system.
6 years
Have hydraulic lines replaced. Every two years in the event of increased usage periods.
Processing material
Specification
Manufacturer/type
(non-binding recommenda-
tion)
Quantity
Hydraulic oil
ISO 32
Viscosity from 22 to 25 mm²/s
OMV HYDRAL 32
Grease
SO XM 2
OMV SIGNUM M 283
As required
Machine component
Lubrication point
Lubrication medium
Manual hydraulic
pump
Stamp
Shaft on the switching valve
Grease:
Apply grease to the listed components using a greased
brush. Remove excess lubricant using a dry and lint-free
cloth.