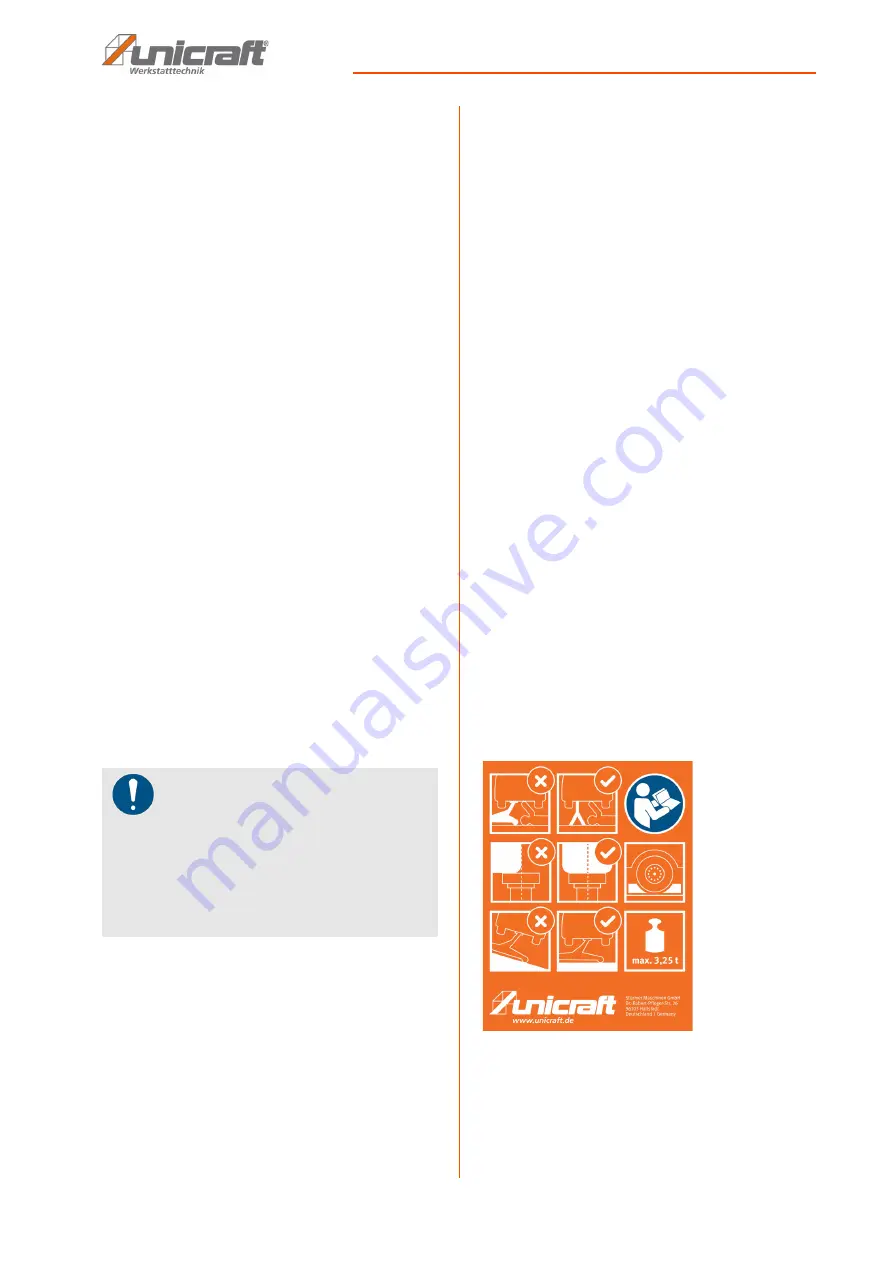
Safety
SRWH-Series | Version 1.01
5
Operator
The operator is instructed by the operating company
about the assigned tasks and possible risks in case of
improper behaviour. Any tasks which need to be perfor-
med beyond the operation in the standard mode must
only be performed by the operator if it is indicated in
these instructions and if the operating company ex-
pressively commissioned the operator.
Qualified electrician
Due to their technical training, knowledge and experi-
ence as well as knowledge of the relevant standards
and regulations, skilled electricians are able to carry out
work on electrical systems and to recognize and avoid
potential hazards independently.
Qualified electricians are specially trained for the wor-
king environment in which they work and are familiar
with the relevant standards and regulations.
Qualified personnel
Due to their professional training, knowledge and expe-
rience as well as their knowledge of relevant regulations
the specialist staff is able to perform the assigned tasks
and to recognise and avoid any possible dangers them-
selves.
Manufacturer
Certain works may only be performed by specialist per-
sonnel of the manufacturer. Other personnel is not au-
thorized to perform these works. Please contact our cus-
tomer service for the execution of all arising work.
2.4 General safety regulations
Maintenance and inspection activities may only be car-
ried out when not in use and only by trained personnel.
It is pointed out that any unauthorized modifications and
changes to the devices are not permitted for safety rea-
sons.
2.5 Safety information for operating personnel
- The operating staff must always make sure that the
specified max. Load capacity of the floor jack is not
exceeded.
- It must be ensured that the ground is sufficiently
stable to hold the load.
- Lift loads only on level, even and firm ground with
the floor jack.
- For vehicles to be lifted, set the wheels straight and
lock with sufficiently sized wedges.
- Never move the lifted load.
- It must never be worked under the lifted load without
it being additionally secured with racks.
- The operator must also ensure that no unauthorized
persons work on and with the floor jack (for example,
by operating devices against unauthorized use).
- The operator is obligated to inspect the floor jack at
least once every day (on a daily basis) for externally
visible damage and defects, and to immediately re-
port any changes (including performance) that af-
fect the safety.
- The operator must ensure that the floor jack is al-
ways operated in perfect condition. If necessary,
the operator must oblige the operating staff to wear
protective clothing, etc.
- In principle, no safety equipment may be dismant-
led or put out of service, there is a risk of massive
crushing hazards.
2.6 Safety labels on the floor jack
The following safety labels are attached to the floor jack
(Fig. 1), which must be observed and fallowed.
Fig. 1: Safety labels SRWH 3002 EF
The safety labels attached to the floor jack must not be
removed. Damaged or missing safety labels can lead to
malfunction, personal injury and material damage.
If the safety labels are not immediately recognizable
and comprehensible, the floor jack must be taken out of
service until new safety markings have been fitted.
NOTE!
In each case, the regulations or guidelines and stan-
dards valid in the country of use must be observed
(in the respectively valid version).
In Germany at the moment
DIN EN 1494: 2000 + A1: 2008: Mobile or mobile lif-
ting equipment and related equipment.
EC Machinery Directive 2006/42 / EC
Summary of Contents for 6201121
Page 20: ...www unicraft de...