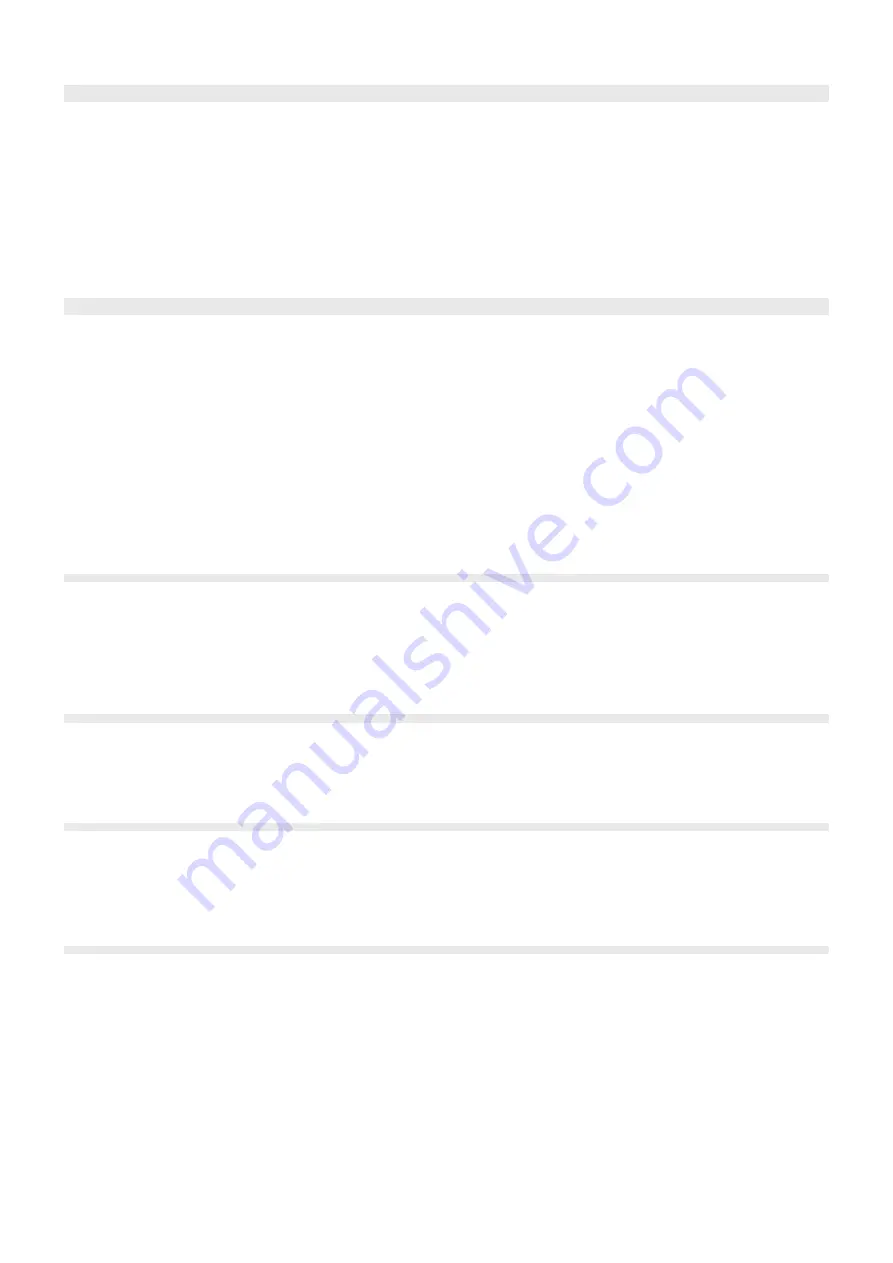
12
2.4 - CONNECTION TO THE
CHIMNEY
The chimney has a foundamental importance
for the good operation of the boiler.
Due to the low temperature of the smokes
during the intermittent operation, it is necessary
that the chimney is perfectly impermeable to
the condensate of the combustion products
and manufactured with corrosion resistant
materials.
The different connections must be sealed with
an approved boiler putty so that the inlet of
fresh air, with consequent increase of the
possibility of condensate formation, is avoided.
Furthermore the possible condensate or rain
water comming from the chimney must be
avoided from entering the smoke chamber
of the boiler.
As far as the cross section and the high of
the chimney is concerned, it is necessary to
make reference to the local and national rules
in force.
In the flue pipe, between the boiler and
the chimney, convenient sampling points
for smoke temperature and combustion
products analysis must be provided.
2.5 - WATER CONNECTIONS
2.5.1 - FEEDING WATER QUALITY
-
The chemical-physical characteristics of
the C.H. system and reinstatement water
are foundamental for the good operation
and safety of the boiler.
-
Among the inconvenients caused by the
bad quality of the feeding water the most
frequent and serious is the scaling of the
heat exchange surfaces.
-
Less frequent, but also dangerous, is the
corrosion of the water side surfaces of all
the circuit.
-
It is well known that the lime, due to its
very low thermal conductivity, reduces the
heat transfer so that also a scaling of a
few millimeters produces very dangerous
localized overheating.
1 mm of lime reduces the heat transfer
from metal to water by 10%.
It is suggested to make a water treatement
in the following cases:
A- high hardness of the water available on
site (higher than 20°f).
B- very large C.H. systems.
C- large quantities of reinstatement water
due to water leaks.
D- subsequent fillings of the system due to
maintenance works.
E- mixing of different metals in the CH circuit.
For the treatment of filling water it is suggested
to address them self to specialized firms.
The same firms are able to provide for the
descaling of the boilers.
Every C.H. system needs reinstatements of
water, du to evaporation, small or large water
leaks or for maintenance works.
It is, therefor, necessary to be able to evaluate
the entity of the reinstatement water to avoid
inconvenients due to untreated water.
For that reason it is suggested to fit, in the
feeding line to the boiler, a water meter for
small capacities.
2.5.2 - C.H. FLOW AND RETURN
CONNECTIONS
The dimensions of flow and return connections
are shown, for each boiler model, in the table
DIMENSIONS.
Before connecting the boiler to the C.H. system,
this one has to be throughly cleaned.
Make sure in the system there is a sufficient
number of air venter.
When connecting flow and return pipes avoid
to create mechanical stress onto the boiler
flanges.
The boiler is not made to support the piping
of the C.H. system, which needs dedicated
supports.
Once the complete C.H. system is finished,
check for water leaks all the connections.
2.5.3 - CONNECTION OF FILLING AND
DRAIN TAP
For the filling and drain of the boiler a
dedicated tap can be connected to the
point T4, which is in rear part of the boi
ler.
2.5.4 - CONNECTION OF THE
PRESSURE RELIEF VALVE
Fit onto the point T3 or onto the supply pipe,
within 0.5 m from the flow flange, a pressure
relief valve properly dimensioned for the
boiler capacity and in conformity with the local
rules in force.
It is forbidden to put any gate valve between
the boiler and the pressure relief valve.
The maximum working pressure of the boiler
is 5 bar for models TXN 65 - TXN 840 and
6 bar for models TXN 1100 - TXN 1900;
the pressure relief valve has to be selected
accordingly.
2.5.5 - CONNECTION OF THE
EXPANSION PIPE AND VESSEL
An expansion vessel is always necessary, to
compensate the water volume increase due
to the heating.
The TRIOPREX-N boilers are suitable for fully
pumped systems, which can be open vented
or sealed.
In the 1
st
case the height of the hydrostatic
column must be, at least, 3 m above the boiler
casing and the capacity of the expansion
cistern shall be able to contain, between the
water surface and the overflow pipe, the volume
increase of all the water of the C.H. system.
Preference shall be given to high and narrow
cisterns, to expose to the air a surface as
small as possible, thus reducing the water
evaporation.
In the 2
nd
case the vessel capacity has to be
calculated taking into consideration:
-
The total volume of the water contained
in the system.
The maximum working pressure of the
system (see setting of PRV).
-
The maximum working pressure of the
expansion vessel.
-
The initial preloading of the expansion
vessel.
-
The maximum working temperature of the
boiler (the maximum setting of the
thermostat fitted onto the panel board is
90 °C; under this aspect it it suggested to
consider 100 °C.
The expansion pipe connects the C.H. system
to the expansion vessel.
This pipe which starts from the connecting
point T3 (see table DIMENSIONS), must have
NO gate valve on it.