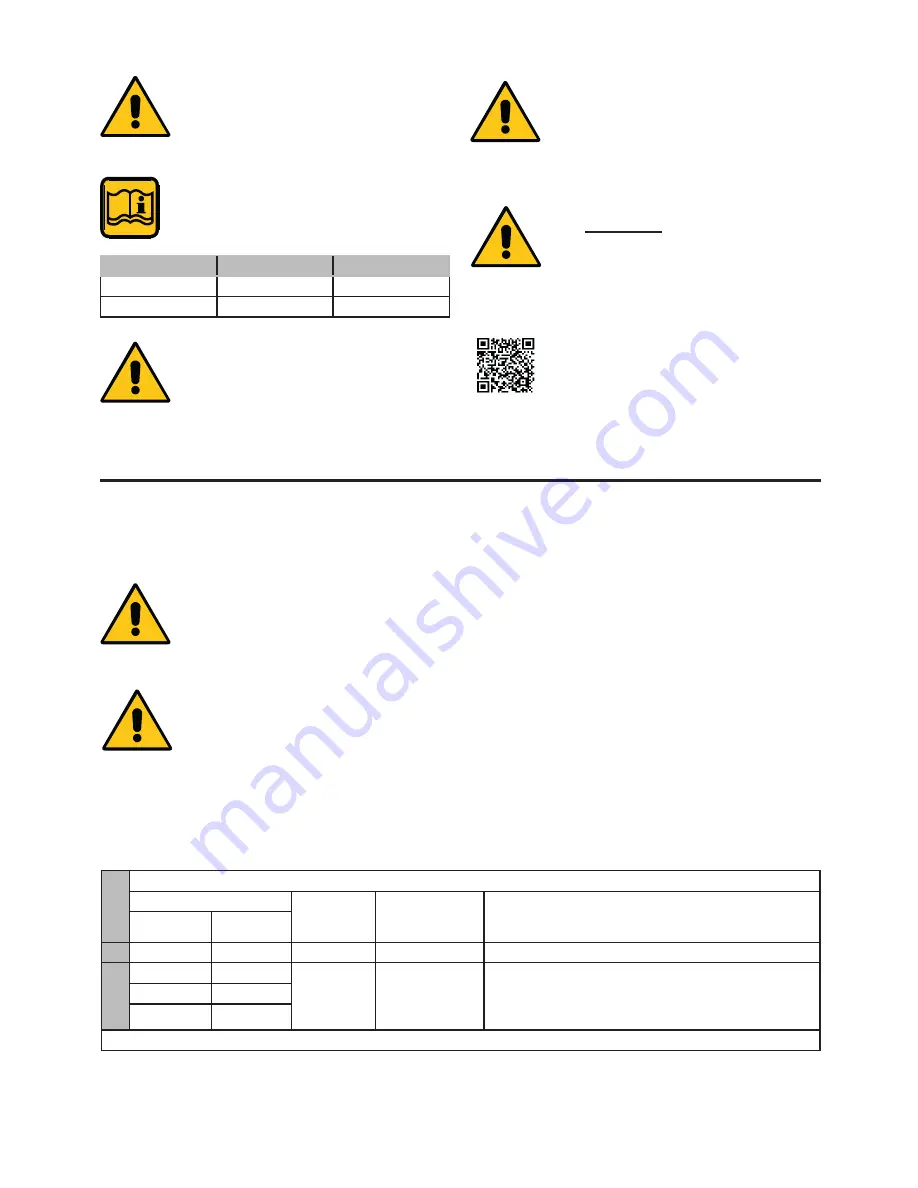
8
ATTENTION (*) see general warnings 1.1:
The heating only models are NOT suitable
for the production of water for human con-
sumption according to Ministerial Decree
D.M. 174/2004.
ATTENTION!
ANY DAMAGE TO THE BOILER CAUSED BY
THE FORMATION OF FOULING OR BY COR-
ROSIVE wATER wILL NOT BE COVERED BY
THE wARRANTY.
1.8 - BOILER ANTIFREEZE
PROTECTION
It is activated by default
VALuE
mIN
mAX
PH
6.5
8
Hardness [°fr]
9
15
NotE!
Further details in the section
‘‘technical Information’’ on the boiler
page of the www.unicalag.it website
this protection can intervene only if the electricity
and gas supplies are connected.
If one of the two is not available and upon reset
11 (Sm) a temperature level between 2 and
5°c is detected, the appliance will behave as
described in the table below, pos 2.
the heating system can be protected effectively
from frost by using antifreeze products with
inhibitor for heating systems (specific for
multidmetal)
do not use car engine antifreeze products as
they could damage the water gaskets.
1.7 - wATER TREATMENT
Feed water treatment prevents problems and
maintains the functionality and efficiency of the
generator over time.
the ideal water pH in heating systems must be
within:
to minimise corrosion, it is crucial to use a cor-
rosion inhibitor; in order for it to work properly,
the metal surfaces must be clean.
(see system protection AccESSoRIES sect. in
domestic price list)
P
O
S
ANTIFREEZE FUNCTION
Power supplies
SM
(*)
Status
antifreeze func-
tion
Actions
Electric
Gas
1
oN
oN
< 7 °c
oN
- Burner and Pump oN until t > 15°c
2
oN
oFF
< 5 ÷ 5 °c
oN
FAuLt SIGNAL codE 16
(with Electrical power supply oN)
(see par. 4.6 - ERRoR codES).
Ignition inhibited.
oFF
oN
oFF
oFF
(*) Flow sensor