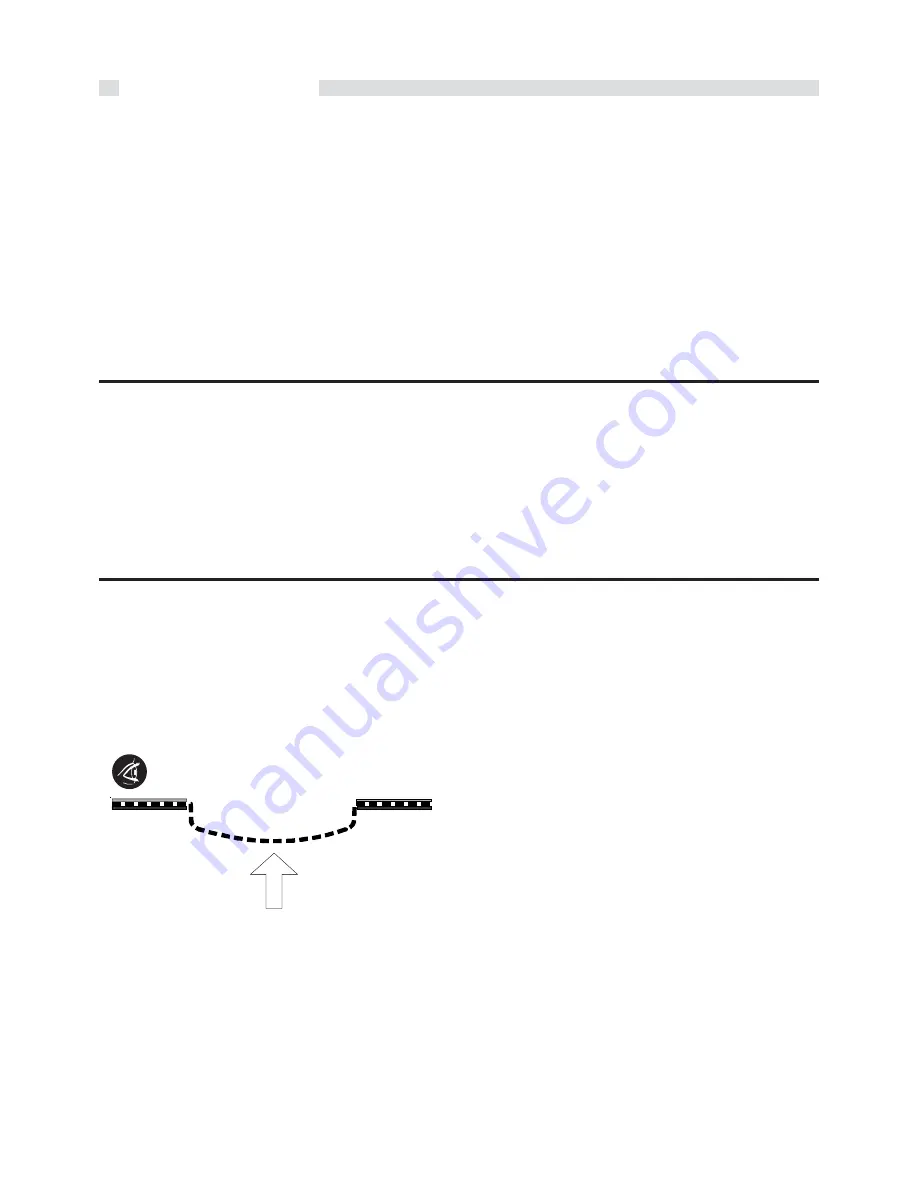
44
Servicing schedule
4.2 - PERIODIC EXAMINATION OF VENTING
SYSTEM
4.3 - PROPER PROCEDURE FOR
CLEANING FLUE GAS
PASSAGEWAYS
(After 1 year maintenance)
Verify that the system of flue and chimney are
unobstructed.
4.4 - PROPER PROCEDURE FOR
CLEANING THE BURNER
The inspection of the boiler and venting system should be
done
every 1 years and full maintenance every 2 years,
whichever occurs first. When doing this the circumstances of
the boiler’s location must be taken into account. From this
one can determine whether to deviate from this advice.
Please contact LATTNER for further guidance on the
frequency and service requirements. Contact details can
be found on the back page of this manual.
Verify that the air ventilation system, air intake and air
intake pipes are unobstructed.
(After 1 year maintenance)
• Perform cleaning of the burners only by blowing, with com-
pressed air, acting from the “side flame”
• Verify visually the state of the spot weldings of the L profiles
and the burner mesh.
Compressed air
•
Wash with water the combustion chamber, avoiding to
wet the electrical harness
During this operation it will be necessary to ascertain
that the condensate drain pipe is free, so that the washing
water does not come out from the inspection hole.
•
Blow the combustion chamber with compressed air, trying
to remove all the dirt still fixed to the fins.
•
Once the washing of the aluminium sections is finished,
make sure the siphon for the evacuation of the conden-
sate is free: if necessary clean it.