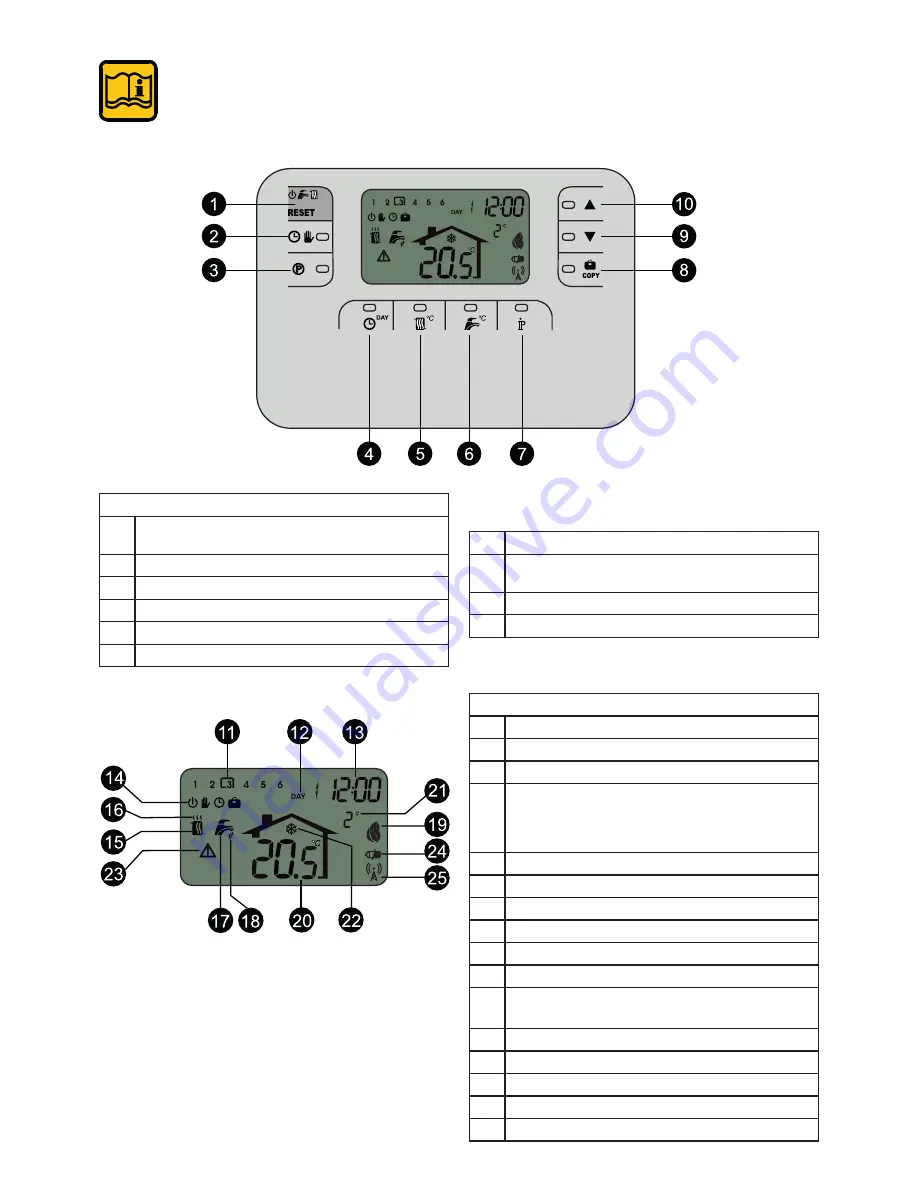
36
4.2 - REMOTE CONTROL EASYr
User instructiona are contained into the
EASYr
package
In this section are indicated only info
necessary for adjustment / maintenance of
the boiler:
- Adjust parameter (Par. 4.3)
KEY
1
OFF / Sumemr / Winter /
Reset faults programs button
2
Automatic / Manual heating program button
3
Heating / DHW programming button
4
Time and Day setting button
5
Heating temperature adjustment button
6
DHW temperature adjustment button
KEY DISPLAY
11 Heating programme time bands
12 Day of week
13 Hours and minutes
14
Programs:
OFF/HEATING MANUAL /
HEATING AUTOMAT. /
HOLYDAY
15 Winter mode
16 Heating demand
17 Summer mode
18 DHW demand
19
Flame presence and level
20 Room temperature
21 Outside temperature
(Only with external probe avaible)
22 Room antifreeze
23 Fault
24
Batteries flat
25 Flashing: Finding synch
25 Fixed: RF comunication ok
7
User information / setting button
8
Holiday function buton/copy heating -
DHW programme day
9
Manual room temperature decrease button
10 Manual room temperature increase button