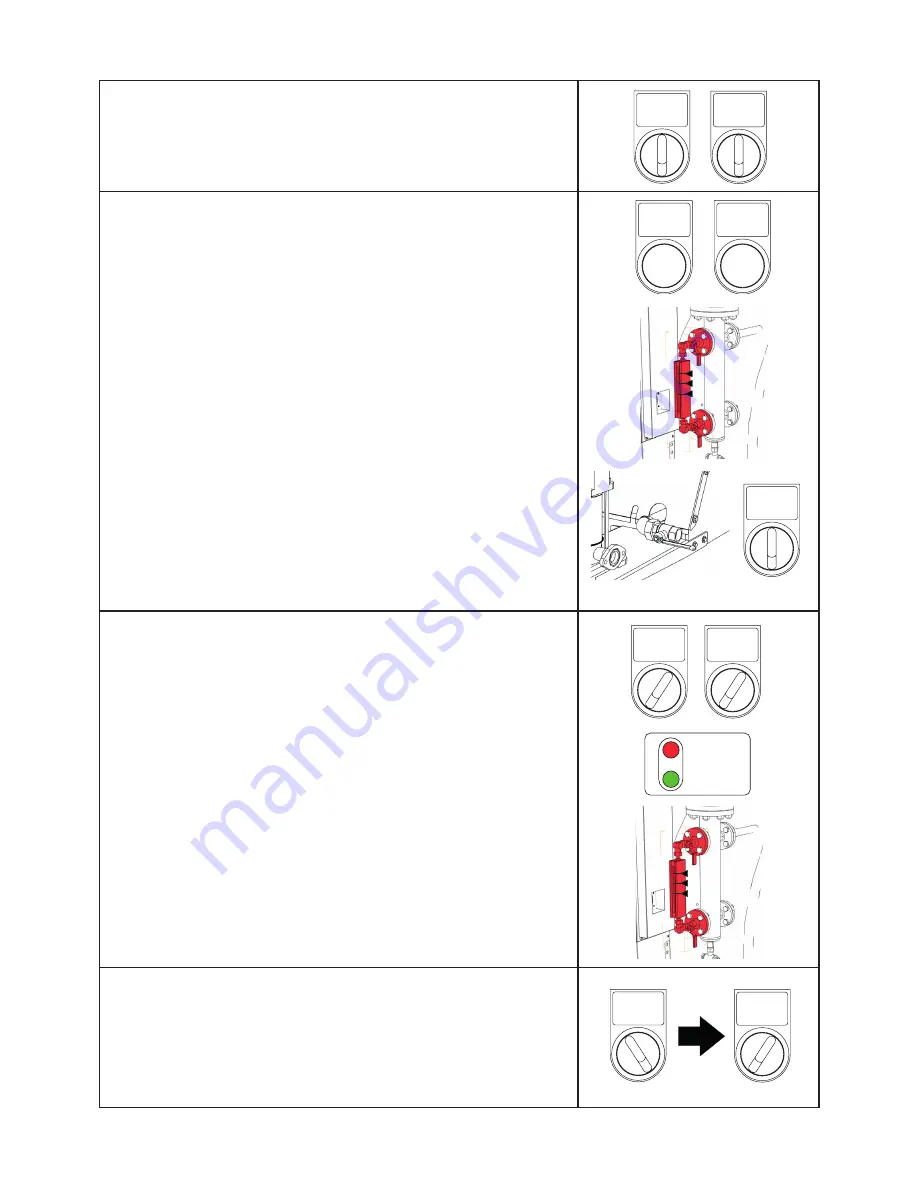
34
P1 MODE
MAN 0 AUT
P2 MODE
MAN 0 AUT
LWL SAFE 1
PUSH to RESET
LWL SAFE 2
PUSH to RESET
SET
HIGH
LOW
P1 MODE
MAN 0 AUT
P2 MODE
MAN 0 AUT
SET
HIGH
LOW
TDS MODE
MAN 0 AUT
Turn off the pump by placing the selector in position
0
.
Force generator emptying below the pump SET / ON level in manual mode to
verify intervention of LWL1 and LWL2 low level safety probes.
Check that the alarm warning light
LWL SAFE 1 - PUSH to RESET
(
LWL
SAFE 2 - PUSH to RESET
) switches on.
Check that the level corresponds to that indicated on the adhesive plate
(LOW)
applied on the side of the level indicator (if the label is not present,
apply it).
Stop the emptying procedure:
- version with manual discharge: act on the lever valve and hand wheel
- version with automatic discharge: by
MAN
activation from panel
Restore the SET level by placing the selector switch
P1 (2) MODE - MAN 0
AUT
in position
AUT
from the panel to start the pump.
When starting the filling phase, the warning light
P1 (2) MODE RUN
on the
panel lights-up.
During the filling phase, check switching off of the red LEDs on the panel on
the level regulators
(LWL SAFE 1 and 2)
and the swithing on of the green
LEDs.
Upon reaching the SET level, the pump stops automatically (the warning
light
P1 (2) MODE RUN
is off) .
Once again, make sure that the level corresponds to the one indicated on the
adhesive plate applied on the side of the level indicator.
Verify the correct operation of the TDS valve (
if any
) by placing the
TDS
MODE - MAN 0 AUT
selector switch in
MAN
position.
Check tha the valve itself opens, place the
TDS MODE - MAN 0 AUT
selec-
tor in
AUT
position.
BLD MODE
MAN 0 AUT
MANUALE
AUTOMATICO
ALARM
OK
TDS MODE
MAN 0 AUT
Summary of Contents for BAHR'UNO
Page 1: ...BAHR UNO INSTRUCTIONS ON INSTALLATION USE AND MAINTENANCE ...
Page 49: ......