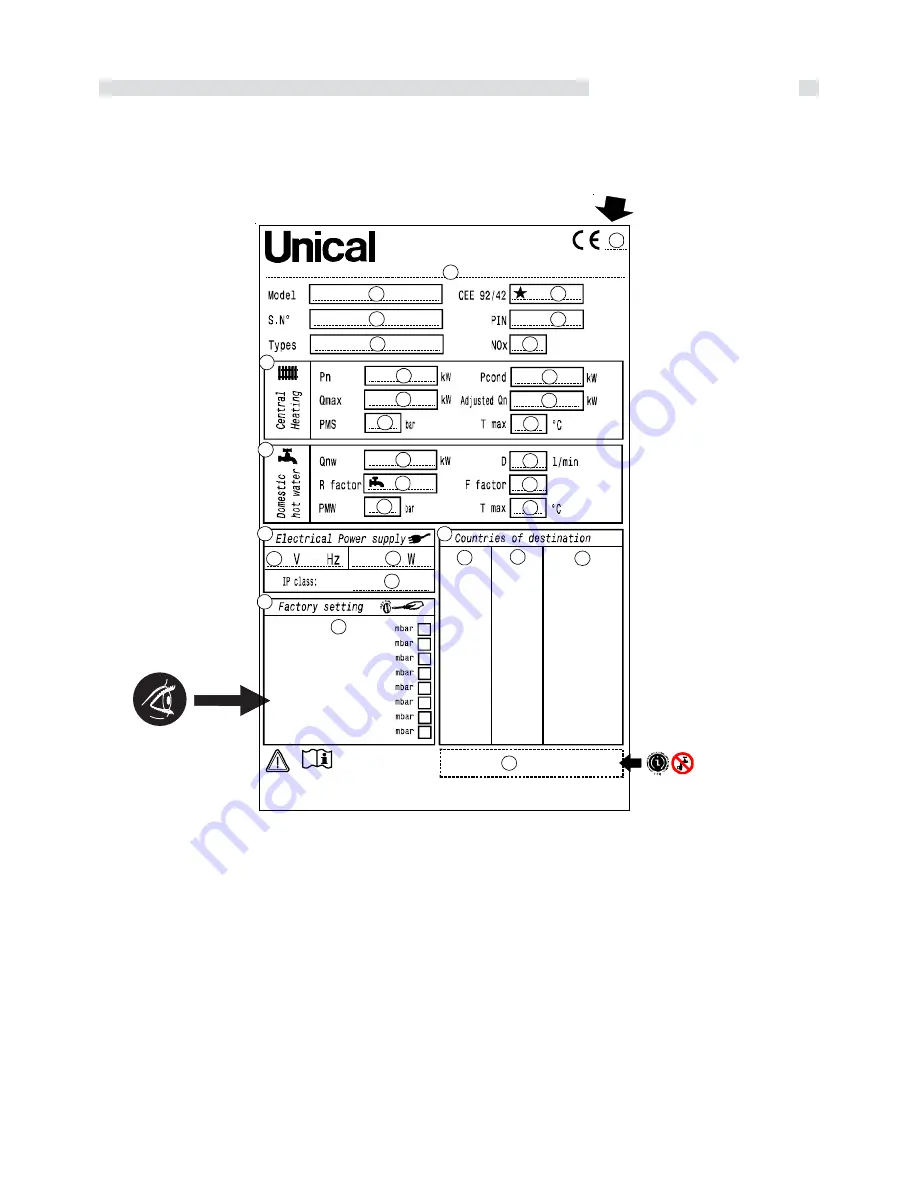
5
General Information
LEGEND:
1 = CE Surveillance notify body
2 =
Boiler type
3 =
Boiler model
4 =
Number of stars (Directive 92/42/CEE)
5 =
(S.N°) Serial number
6 =
P.I.N. code
7 =
Approved fluing configurations
8 =
(N0x) N0x class
A = Central Heating circuit features
9 =
(Pn) Nominal output
10 = (
Pcond) Condensing nominal output
11 =
(Qmax) Nominal heat input
12 = (Adjusted Qn) Adjusted for nominal Heat input
13 =
(PMS) Max. pressure C.H. system
14 =
(T max) Max. C.H. temperature
B = Domestic Hot Water circuit features
15 = (Qnw) Nominal heat input in D.H.W. mode (if different from Qn)
16 = (D) Specific D.H.W. flow rate according to EN 625 - EN 13203-1
17 = (R factor) N° taps based on the quantity of water declared EN
13203-1
18 = (F factor) N°stars based on the quality of water declared
EN 13203-1
19 = (PMW) Max. pressure D.H.W. system
20 = (T max) Max. temperature D.H.W system
C = Electrical features
21 = Electrical power supply
22 = Consumption
23 = Protection grade
D = Countries of destination
24 = Direct and indirect country of destination
25 = Gas family
26 = Supply pressure
E = Factory setting
27 = Adjusted for gas type X
28 = Space for national brands
1.6
DATA BADGE
CE Marking
-
The CE marking documents that the boilers satisfy:
-
The essential requirements of the Directive regarding gas appliances (Directive
90/396/CEE)
-
The essential requirements of the ElectroMagnetic CompatibilityDirective
(2004/108/CEE)
-
The essential requirements of the BoilersEfficiency Directive ( 92/42/CEE)
-
The essential requirements of the Low Voltage Directive ( 2006/95/CEE)
®
1
2
3
5
7
8
6
4
9
11
13
10
12
14
15
17
19
16
18
20
28
A
B
21
22
23
24
25
26
27
C
D
E
Summary of Contents for ALKON 50 kW
Page 1: ...00333009 a 3rd edition 02 10 ALKON 70 kW ALKON 50 kW INSTALLATION ANDSERVICING MANUAL ENGLISH ...
Page 62: ......
Page 63: ......