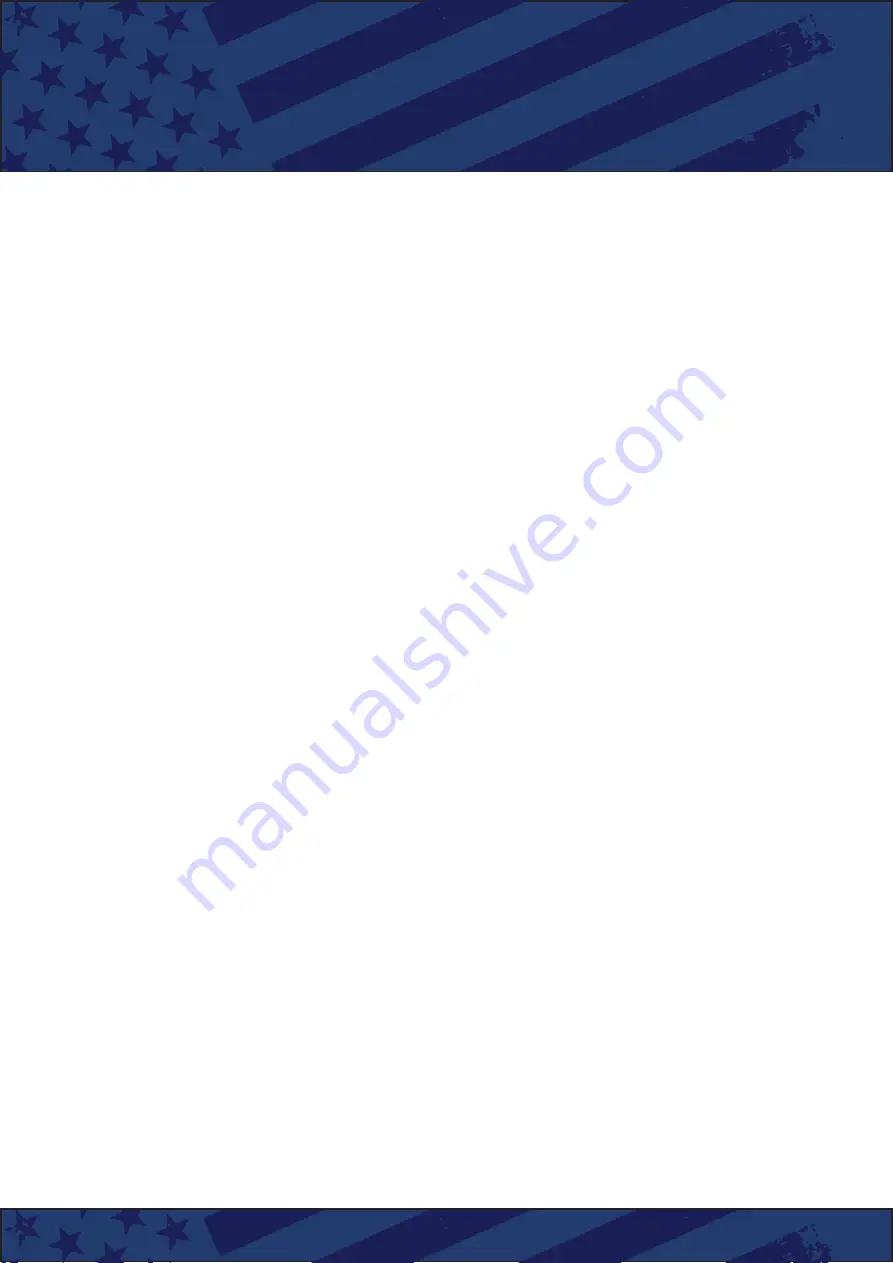
24
2
6
s
Warranty Statement
Unibor™ warrants its machines to be free from faulty parts, under normal usage of machines, for a period of 12
months from initial date of purchase. All other parts (excluding cutters) are under warranty for 90 days, provided
that the warranty registration card (or online registration) has been completed and returned to Unibor™ or its
designated distributor within a period of (30) days from the purchase date. Failure to do so will void the
warranty.
If the stated is adhered to, Unibor™ will repair or replace (at its option) without charge any faulty items returned.
This Warranty does not cover:
1. Components that are subject to natural wear and tear caused by the use is not in accordance with the
operator’s instructions
2. Defects in the tool caused by non-compliance with the operating instructions, improper use, abnormal
environment conditions, inappropriate operating conditions overload or insufficient servicing or maintenance.
3. Defects caused by using accessories, components or spare parts other than original Unibor™ parts.
4. Tools to which changes or additions have been made.
5. Electrical components are subject to manufacturer’s warranty.
The warranty claim must be logged within the warranty period. This requires the submission or sending of the
complete tool in question with the original sales receipt which must indicate the purchase date of the product. A
complaint form must also be submitted prior to the return.
This can be found online at www.unibor
usa
.com. Failure to complete this form will result in the delay of your
claim.
All goods returned defective must be returned pre-paid to Unibor™, in no event shall Unibor™ be liable for
subsequent direct, or indirect loss or damage.
THIS WARRANTY IS IN LIEU OF ANY OTHER WARRANTY, (EXPRESSED OR IMPLIED) INCLUDING
ANY WARRANTY OF MERCHANTABLITY OR FITNESS FOR A PURPOSE. UNIBOR™RESERVE THE
RIGHT TO MAKE IMPROVEMENTS AND MODIFICATIONS TO DESIGN WITHOUT PRIOR NOTICE
Known and Trusted Worldwide for Quality, Performance and Reliability
Summary of Contents for E4000 Perm
Page 2: ...2...
Page 11: ...11 s Control Panel...
Page 16: ...16 s Wiring Diagram...
Page 17: ...17 s Machine Parts...
Page 18: ...18 s Machine Parts...
Page 19: ...19 s Motor Gearbox Parts...
Page 20: ...20 s Motor Gearbox Parts...
Page 25: ...25 s Cutting Speed Selection...
Page 27: ...26 s Extra...
Page 28: ...27 s Extra...
Page 29: ...28 s Extra...
Page 30: ...29 s Extra...
Page 31: ...30 s Extra...
Page 32: ...31 s Extra...
Page 33: ...32 WWW UNIBORUSA COM This machine is CSA approved...