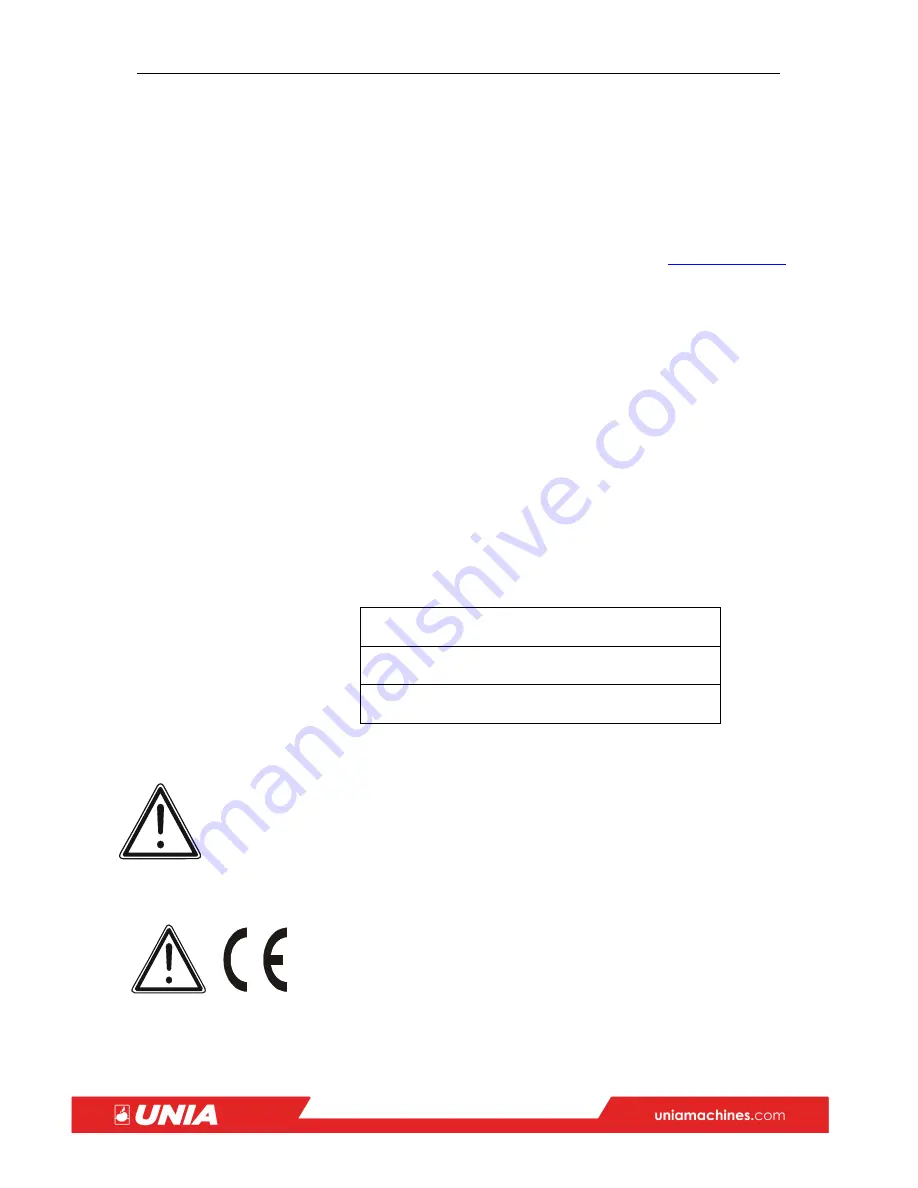
OPERATING AND MAINTENANCE MANUAL ARES L
- 3 -
UNIA Sp. z o.o.
st. Szosa Torunska 32/38
PL 86 – 300 Grudziadz
tel. + 48 56 451 05 00
fax. + 48 56 451 05 01
Service tel. + 48 56 451 05 26
uniamachines.com
ARES L
OPERATING AND MAINTENANCE
MANUAL
Machine identification data:
Type
Production year
Serial no.
This maintenance and operating manual is an integral part of the
machine. It is important that the manual is always in the possession
of the machine user. Access to the manual should be provided to
machine operators and cooperating persons while operation,
regulation, repairs and renovations.
Before starting the machine please read the operating
manual and follow the recommendations and
instructions regarding safety and proper usage of the
machine.
Summary of Contents for ARES L 2.5
Page 1: ......
Page 2: ......
Page 4: ......
Page 30: ...OPERATING AND MAINTENANCE MANUAL ARES L 33 COMMENTS AND NOTE ...
Page 31: ...OPERATING AND MAINTENANCE MANUAL ARES L 34 COMMENTS AND NOTE ...
Page 32: ...OPERATING AND MAINTENANCE MANUAL ARES L 35 COMMENTS AND NOTE ...