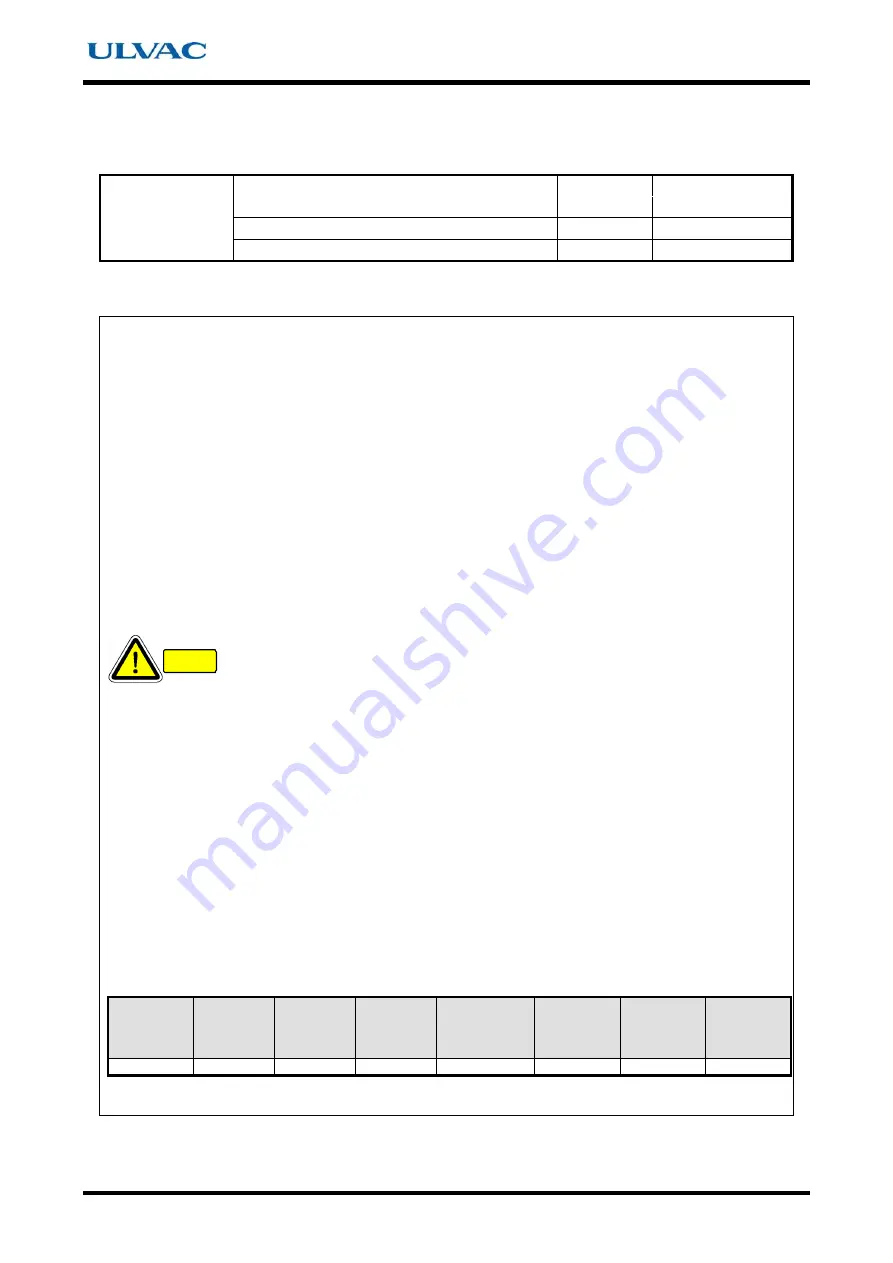
Instructions Manual
-
Multiple Roots Type Dry Pump GR60/90/180
YK09-0023-DI-003-02
18
3.6 Cooling water pipe
The pump cooling water port is Rc 3/8. Connect to the cooling water pipe using an appropriate joint.
Cooling water
Supply water pressure
MPaG
0.1 - 0.3
Pressure difference between outlet and inlet
MPaG
0.1
Supply cooling water temperature
℃
10 – 30
※
Flow rate
L/min.
5.0
* No condensation
(1) If the operation is continued under the conditions where the cooling
water flow is lower than the specified value, the pump may be
broken. Using a flow sensor etc, make a system that shuts out the
supply of electricity to the pump in the event that the cooling water
stops.
(2) It is designed to prevent leakage under specified conditions and a
leak test is performed. However, any abnormal conditions outside
the range of the specifications (such as an abnormal pressure
increase) may cause leakage. In such a case, water continues to
leak until the supply from the device stops. Do not install electric
equipment or wires on the bottom of or the floor surface in the
proximity of the pump.
(3) During the operation of this product, the vacuum pump body needs
to be cooled at all times by supplying a specified amount of flowing
water. Install a flow meter that can visually recognize the flow (such
as a flow sight) to check that cooling water flows.
(4) Install a water leakage sensor on the floor under the pump. If any
water leakage is detected, immediately close the feed valve of the
cooling water and set up a system to shut out electricity to the
pump.
(5) Attach a feed valve to stop the supply of cooling water.
(6) We recommend using water with the low amount of impurities (such
as industrial water shown in the table below) for cooling water of this
product. Water stain, such as calcium carbonate, accumulates in the
cooling water system of this product depending on the water quality,
which reduces the cooling efficiency. In addition, chlorine ions may
corrode from the inner wall, causing cooling water leakage. Note that
in such a case, the repair will be charged.
Established by: Japan Industrial Water Association (Industrial Water Quality Criteria Establishment
Committee)
Turbidity
(mg/L)
pH
-
Alkali level
CaCO
2
mg/L
Hardness
Mg, CaCO
3
mg/L
Evaporation
residue
mg/L
Chlorine
ion
Cl
-1
Mg/L
Iron
Fe
mg/L
Manganese
Mn
mg/L
20
or less
6.5-8.0
75
or less 120
or less
250
or less
80
or less
0.3
or less
0.2
or less
[Reference] Supplied Standard Water in Japanese Industrial Water Service
CAUTION