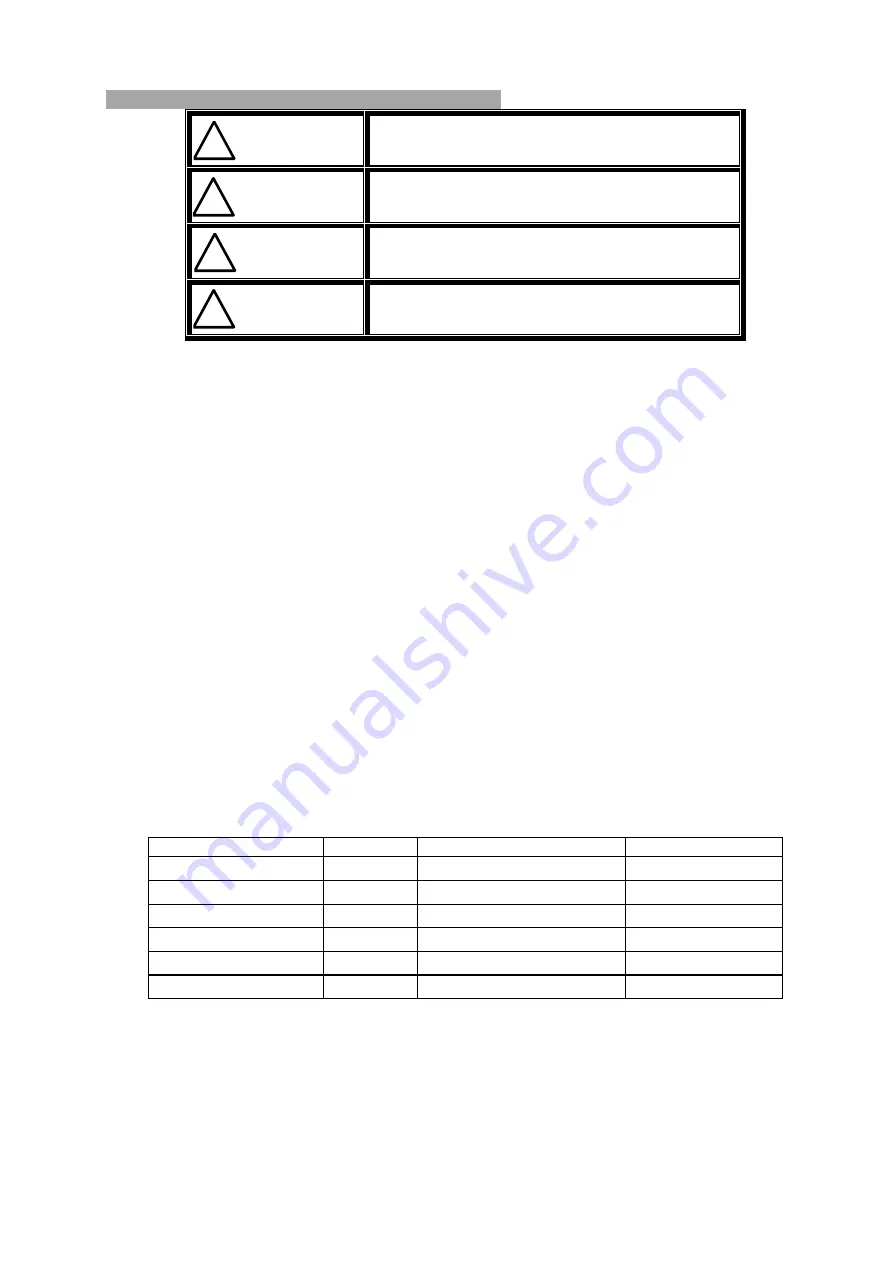
7
6. Maintenance, Inspection, and Repair
6.1. Cautions for Maintenance, Inspection, and Repair
See Danger (3), P04
See Warning (4)(18)(19), P04,P05
See Caution (10)(11), P06
See Note (14), P06
Customer repair technicians are able to perform the following maintenance and repairs. Other
repairs and modifications (except for the standard options available from the manufacturer)
should not be performed by the customer.
1) Replacing cup packing
2) Replacing suction and exhaust valves
3) Replacing gaskets
4) Replacing O rings
6.2 Maintenance
The following checks are required at least once every three days during operation.
(1) Check for abnormal noises.
(2) Check for abnormal heating of the pump.
(3) Check that gas is discharged normally.
If a problem is found, take the measures described in 6.5 Troubleshooting List.
6.3 Regular Inspections
Inspect consumables after the first 3000 hours of operation, and replace and clean in
accordance with the " Guidelines for Replacement and Cleaning "on the following page. Refer to
6.5 Replacing Consumables and Cleaning for procedures.
Request replacement by the manufacturer
’s service division if a repair technician is not
available.
Table 6.1 Consumables List
Components
Quantity
Material
Average life
Cup packing
2
PTFE
3,000 Hr
Suction valves
2
SUS
3,000 Hr
Exhaust valves
2
SUS
3,000 Hr
Gaskets
2
FPM
10,000 Hr
O rings
6
FPM
10,000 Hr
Bearing
4
15,000 Hr
Note that the average life for a component varies with the conditions of use.
Always follow 4.1 Cautions for Operation, and remember that life is extended by running the
pump at minimal load (running the pump at minimal load is operation at near-atmospheric
pressure).
Bearings are replaced by the manufacturer’s service division.
!
Danger
!
Warning
!
Caution
!
Note