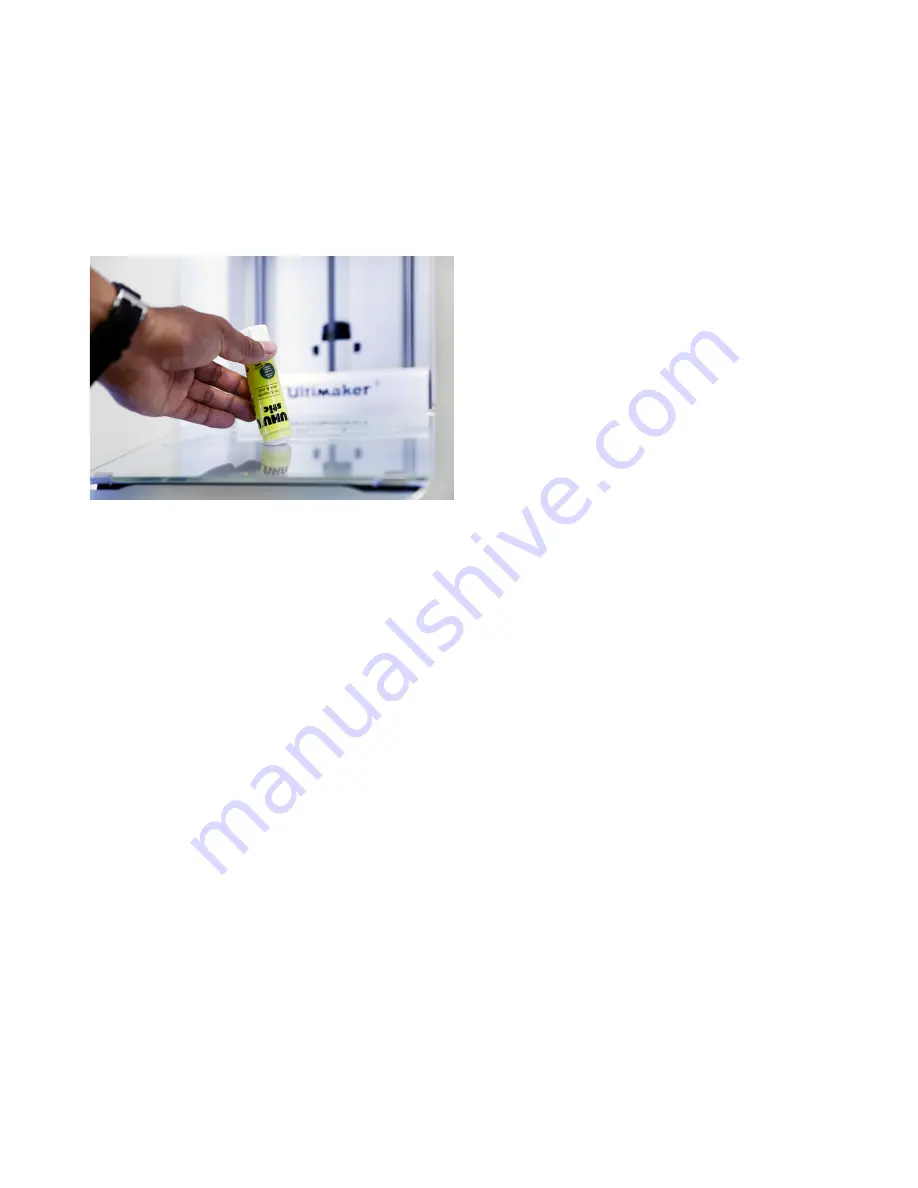
29
Build plate adhesion
Although the heat of the heated build plate already helps with a good adhesion of the material to the glass plate, you will
need an adhesive in some cases. In the accessory box of your Ultimaker 3 is one glue stick, of which a thin, even layer can
be applied to the glass plate to let the first layer of the print stick better. Below you can find an overview on the use of glue
per material.
PLA
Ultimaker PLA usually adheres well to the glass plate. Make sure that the glass plate is completely clean and free of any
oil/grease and fingerprints. For best results, you can apply a thin layer of glue to the glass plate.
Once the print is finished, do not remove it while the build plate is still warm. This can result in deformation of the base of
your print.
ABS
When printing with Ultimaker ABS you must apply a thin layer of glue to the glass plate. Not using the glue results in a
high risk of chipping the glass plate when removing the print and may void the warranty.
Please note that for this material it may be easier to remove the 3D prints from the build plate if it is still slightly warm at
approximately 40ºC.
CPE
Although Ultimaker CPE adheres well to the glass plate, it does tend to warp heavily. To minimize warping when printing
with Ultimaker CPE, apply a thin layer of glue to the glass plate using the glue provided with your Ultimaker 3.
Nylon
Ultimaker Nylon sticks well to the build plate. In most instances, extra adhesives are not necessary for a successful print.
For even better build plate adhesion, apply a thin layer of glue to the glass plate.
PVA
Ultimaker PVA strongly adheres to the build plate, so we suggest to apply a thin layer of glue to the glass plate.