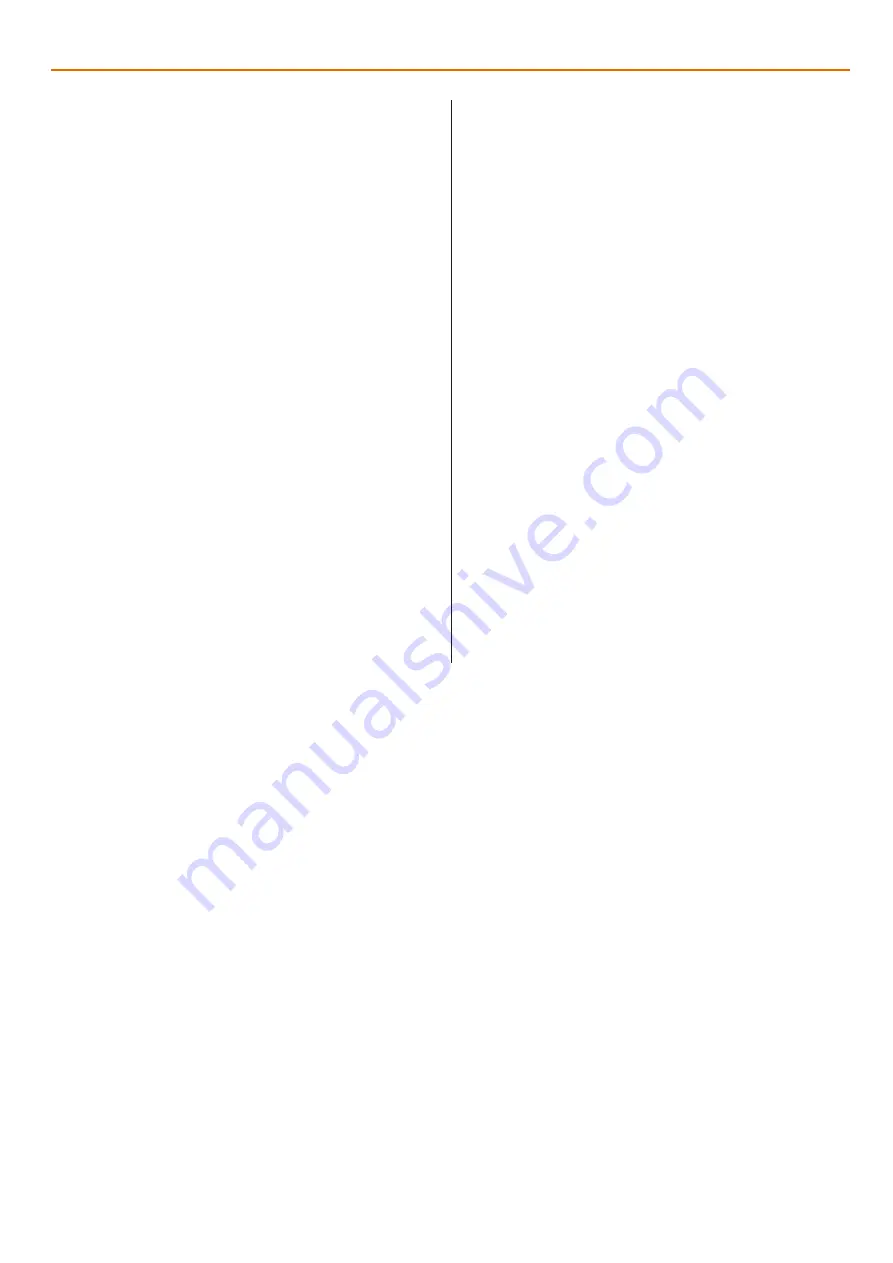
Safety Instructions for use of Routers
5
1. Make sure you have read and fully understood the
General Instructions and safety precautions that apply
to your router.
2. Before connecting the machine to the supply; check
for obvious signs of damage, paying particular attention
to the plug and the power cable. Rectify or have rectified
any damage you discover. Fit and set the guide bush,
using the Guide Bush Check Centre, to check
concentricity, if you are doubtful of correct centering.
Check the cutter bit you are about to fit is the correct
tool for the job. Check the bit for damage, make sure it
is sharp and clean, check you have the correct collet for
the cutter shank size you are about to fit, ensure that a
sufficient length of the shank is inserted in the collet to
guarantee a secure fixing. (‘K’ line on cutter shank)
Conversely, ensure there is sufficient length of cutter to
carry out the cutting task. Make sure that the tools you
use to fit the cutter bit, or any accessories are the correct
ones, DO NOT risk damaging the router by using the
wrong size spanners, Hex keys, etc. Make sure the ‘chip
screens’ (if available) are fitted securely. If dust
extraction is available, connect it.
3. Check that all accessories, tools etc., that have been
used to set the machine up, are removed and set
carefully aside or stowed away correctly.
4. Set the depth of cut, either as one plunge or
incrementally (Staight cutters only).
5. Ensure the machine is switched off. Never engage a
trigger hold-on unless you are actually holding the
machine. Plug the power cable into a correctly rated
switched socket outlet. If extension leads are being
used, check these for damage, do not use if damaged,
check that any extension cables in use are correctly
rated for use with your machine. Switch on the supply.
6. Make sure you are holding the machine in a safe
position, ensure that the cutter bit is not in contact
with anything, and the ‘plunge’ is locked off. Give the
machine a quick “burst”, to ensure that everything is
working correctly, check especially for vibration, which
might indicate that the cutter is incorrectly fitted. If you
disconnect the machine; re-fit the cutter and test again.
7. If there is any vibration make sure that the jig is
clamped or fixed firmly to the workbench.
8. Make sure that the power cable is safely positioned
away from the operating area, and when operating
the router, the movement of this operation will not
drag it to within range of the router or cutter.
Summary of Contents for 506300
Page 26: ...Exploded Diagram Parts List 26...