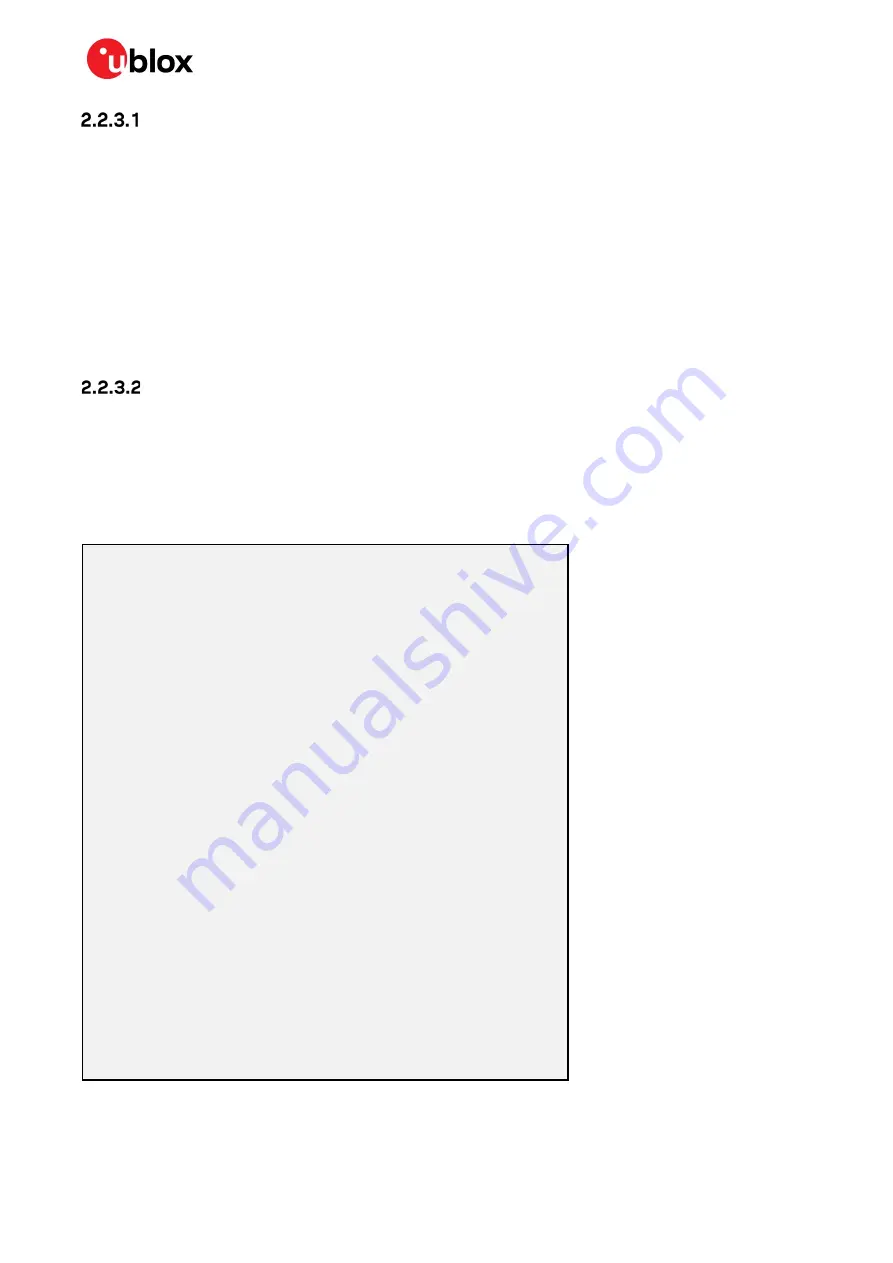
NINA-B1 series - System integration manual
UBX-15026175 - R16
Software
Page 21 of 63
C1-Public
Getting started with the Arm Mbed OS
A list of prerequisites for getting started with Arm Mbed OS 5 development on EVK-NINA-B1 is
available at
https://github.com/ARMmbed/mbed-os-example-ble#getting-started
Mbed CLI is the name of the Arm Mbed command line tool, which enables the full Mbed workflow, such
as repositories version control, maintaining dependencies, updating from remotely hosted
repositories (GitHub, GitLab and mbed.org), and invoking Arm Mbed's own build system. The
document describes the installation and usage of the Mbed CLI and is available at
https://github.com/ARMmbed/mbed-cli#introduction
For information describing how to create a build target for EVK-NINA-B1, see section 2.2.3.2.3.
Bluetooth low energy examples from Arm Mbed are available at
https://github.com/ARMmbed/mbed-
Create a custom target for Arm Mbed
2.2.3.2.1
Add target
Add a new JSON object to the
targets.json
file located in the
\mbed-os\targets\
folder. Figure 8
shows an example of the JSON object for EVK-NINA-B1. A list of the properties known to the Arm
Mbed build system are described in the Standard properties section in reference [5].
☞
The given folder location
\mbed-os\targets\
is standard in Arm Mbed OS release 5.6.
Figure 8: Example of EVK-NINA-B1 target object
"EVK_NINA_B1": {
"supported_form_factors": ["ARDUINO"],
"inherits": ["MCU_NRF52"],
"macros_add": [
"BOARD_PCA10040",
"NRF52_PAN_12",
"NRF52_PAN_15",
"NRF52_PAN_58",
"NRF52_PAN_55",
"NRF52_PAN_54",
"NRF52_PAN_31",
"NRF52_PAN_30",
"NRF52_PAN_51",
"NRF52_PAN_36",
"NRF52_PAN_53",
"S132",
"CONFIG_GPIO_AS_PINRESET",
"BLE_STACK_SUPPORT_REQD",
"SWI_DISABLE0",
"NRF52_PAN_20",
"NRF52_PAN_64",
"NRF52_PAN_62",
"NRF52_PAN_63"],
"device_has": [
"ANALOGIN",
"ERROR_PATTERN",
"I2C",
"I2C_ASYNCH",
"INTERRUPTIN",
"LOWPOWERTIMER",
"PORTIN",
"PORTINOUT",
"PORTOUT",
"PWMOUT",
"RTC",
"SERIAL",
"SERIAL_ASYNCH",
"SLEEP",
"SPI",
"SPI_ASYNCH",
"SPISLAVE"],
"release_versions": ["2", "5"]
}