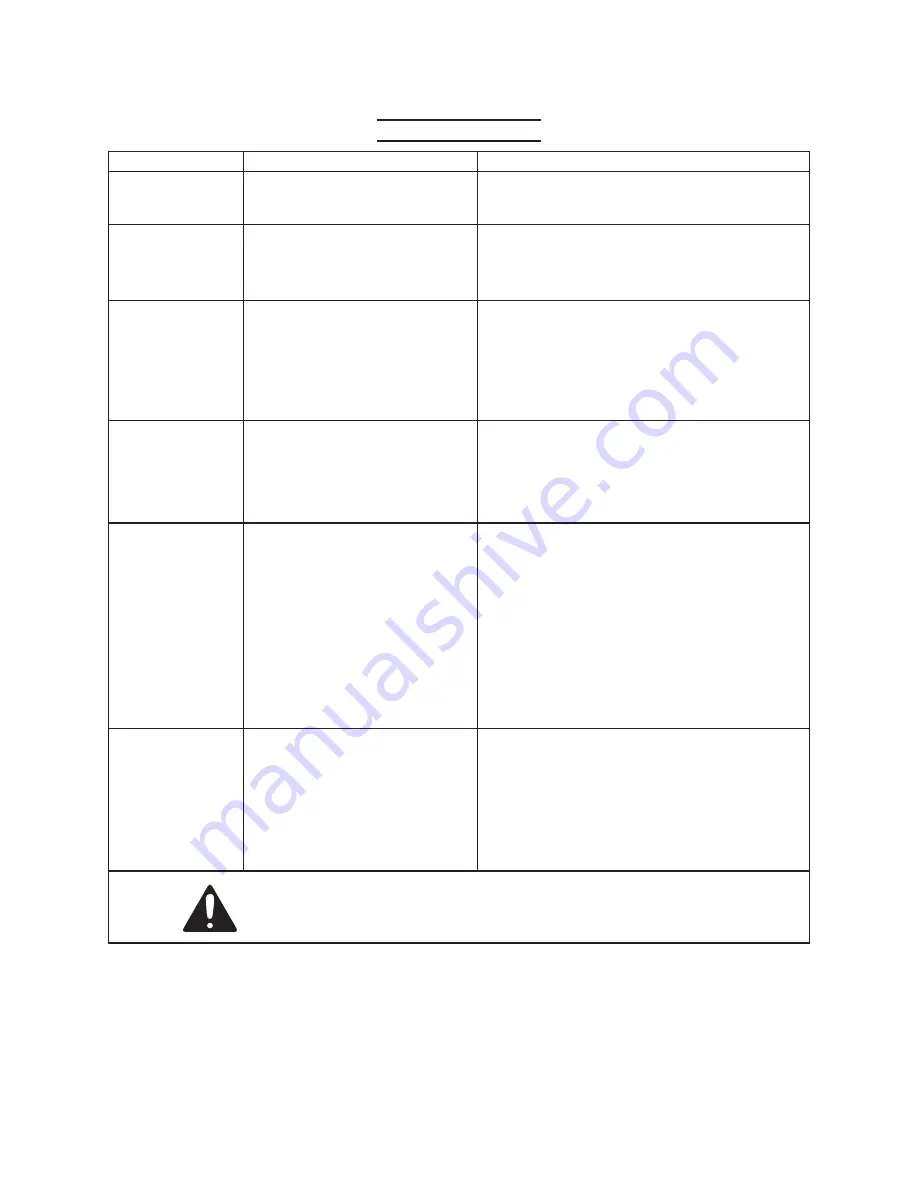
Page 14
For technical questions, please call 1-800-444-3353.
SKU 65204/
99918
troubleshooting
Problem
Possible causes
likely solutions
Engine will not
start.
Start procedure not followed
completely.
Empty all pressure from tank, open pilot valve,
and carefully follow starting instructions in
engine manual.
Compressor over-
heats.
Incorrect lubrication or not
1.
enough lubrication.
Worn parts.
2.
Lubricate using recommended oil or grease
1.
according to directions.
Have qualified technician inspect internal
2.
mechanism and replace parts as needed.
Severe air
leakage.
Poor air outlet seal.
1.
Loose cylinder/cylinder head.
2.
Damaged valve or housing.
3.
Dirty, worn or damaged valve.
4.
Tighten or re-attach using thread seal tape.
1.
Tighten cylinder/cylinder head assembly. If
2.
cylinder/cylinder head cannot tighten properly,
internal parts may be misaligned.
Replace damaged components.
3.
Clean or replace valve assembly.
4.
Unit stalls
Low engine idle.
1.
Severely clogged air filter.
2.
Improper lubrication.
3.
Defective pilot/unloader valve.
4.
Qualified technician should increase idle to
1.
1,800±100 RPM by adjusting pressure switch.
Replace air filter.
2.
Check for proper oil level.
3.
Replace.
4.
Excessive noise
Loose drive pulley or flywheel.
1.
Misaligned pulleys.
2.
Lack of oil in crankcase.
3.
Worn connecting rod.
4.
Worn wrist pin bushing.
5.
Worn bearings.
6.
Loose belts.
7.
Loose pulleys are a common cause of
1.
“knocking”. Tighten appropriate bolts.
Align pulleys with straightedge and secure in
2.
place.
Check for proper oil level.
3.
Replace.
4.
Remove piston assembly and replace
5.
necessary parts.
Replace bearings and oil.
6.
Check for proper belt tension.
7.
Oil in the discharge
air
Wrong type of oil or low-quality
1.
oil.
Overheating.
2.
Restricted intake air.
3.
Worn piston rings.
4.
Excessive moisture in the tank.
5.
Change oil. Check oil recommendations
1.
under
EquipmEnt SEt up
,
Equipment Oil
Fill
section of this manual.
See above section.
2.
Clean or replace air filter.
3.
Replace.
4.
Drain moisture from the tank daily.
5.
Follow all safety precautions whenever diagnosing or
servicing the tool.