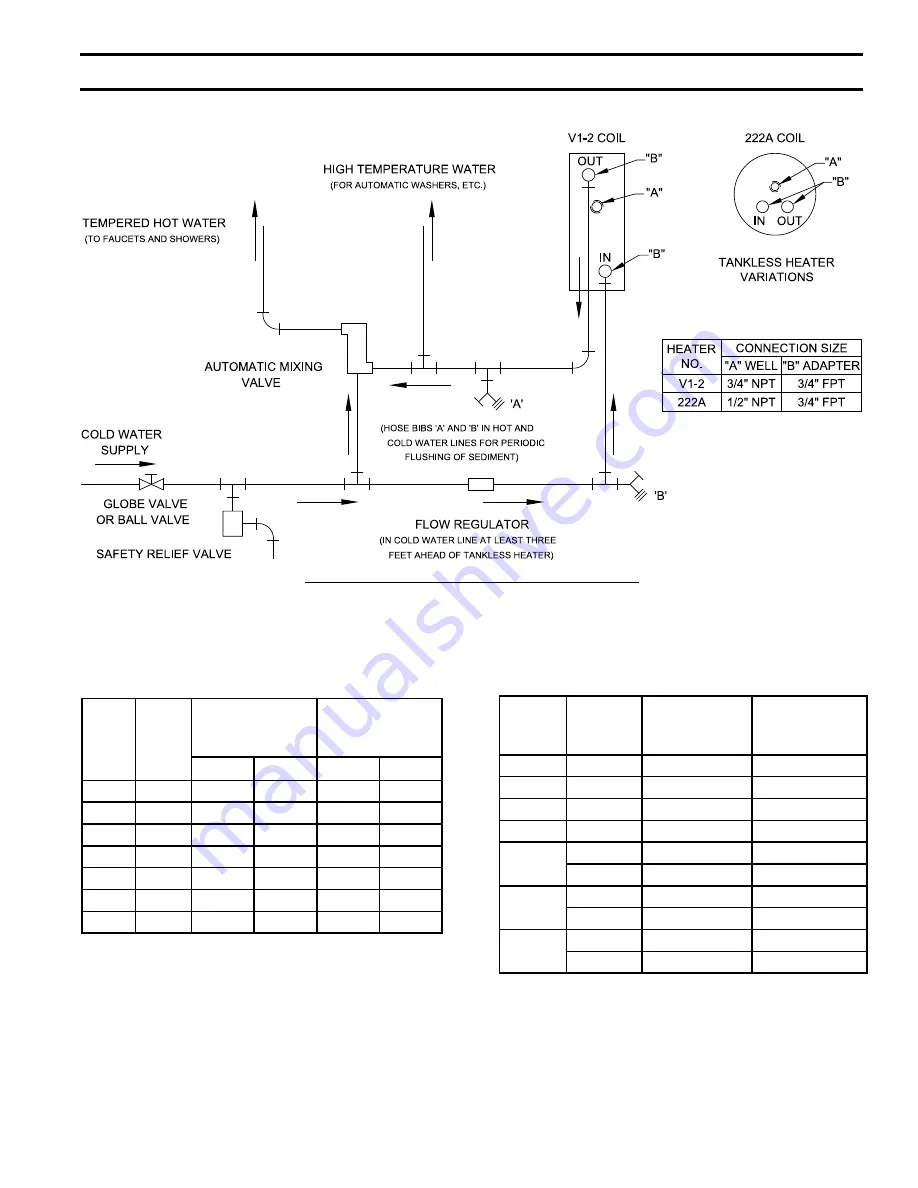
35
Figure 17A: Schematic Tankless Heater Piping
TABLE 2A: TANKLESS HEATER DATA:
Rear Mounted Heater on Steam and Water Boilers
TABLE 2B: TANKLESS HEATER DATA:
Front Mounted Heater on Water Boilers
Boiler
Model
Heater
No.
Heater Rating
(GPM)
Pressure Drop
thru Heater
(PSI)
Steam Water
Steam
Water
V8H3
V1-2
2.75
3
3.9
4.7
V8H4
V1-2
3
3.25
4.7
5.6
V8H5
V1-2
3.25
3.5
5.6
6.4
V8H6
V1-2
3.75
3.75
7.2
7.2
V8H7
V1-2
3.75
4
7.2
8
V8H8
V1-2
4
4.5
8
9.8
V8H9
V1-2
4
4.5
8
9.8
Boiler
Model
Heater
No.
Heater Rating
(GPM)
Pressure Drop
thru Heater
(PSI)
V8H3
222A
3
22
V8H4
222A
3.5
22
V8H5
222A
4
30.5
V8H6
222A
4.5
33
V8H7
222A
4.6
33
A54
5.5
36
V8H8
222A
4.75
40
A54
6
39.5
V8H9
222A
4.75
40
A54
6
39.5
SECTION VII: TANKLESS AND INDIRECT WATER HEATER PIPING (cont'd)
Summary of Contents for V8H SERIES
Page 76: ...76 Bare Boiler Assembly Continued SECTION XVI Repair Parts continued ...
Page 78: ...78 Jacket Assembly SECTION XVI Repair Parts continued ...
Page 80: ...80 V8H3 Thru V8H9 Steam Boilers Trim and Controls SECTION XVI Repair Parts continued ...
Page 82: ...82 V8H3 Thru V8H9 Water Boilers Trim and Controls SECTION XVI Repair Parts continued ...
Page 84: ...84 Beckett AFG Burner SECTION XVI Repair Parts continued ...
Page 94: ...94 SERVICE RECORD DATE SERVICE PERFORMED ...
Page 95: ...95 SERVICE RECORD DATE SERVICE PERFORMED ...
Page 96: ...96 U S Boiler Company Inc P O Box 3020 Lancaster PA 17604 1 888 432 8887 www usboiler net ...