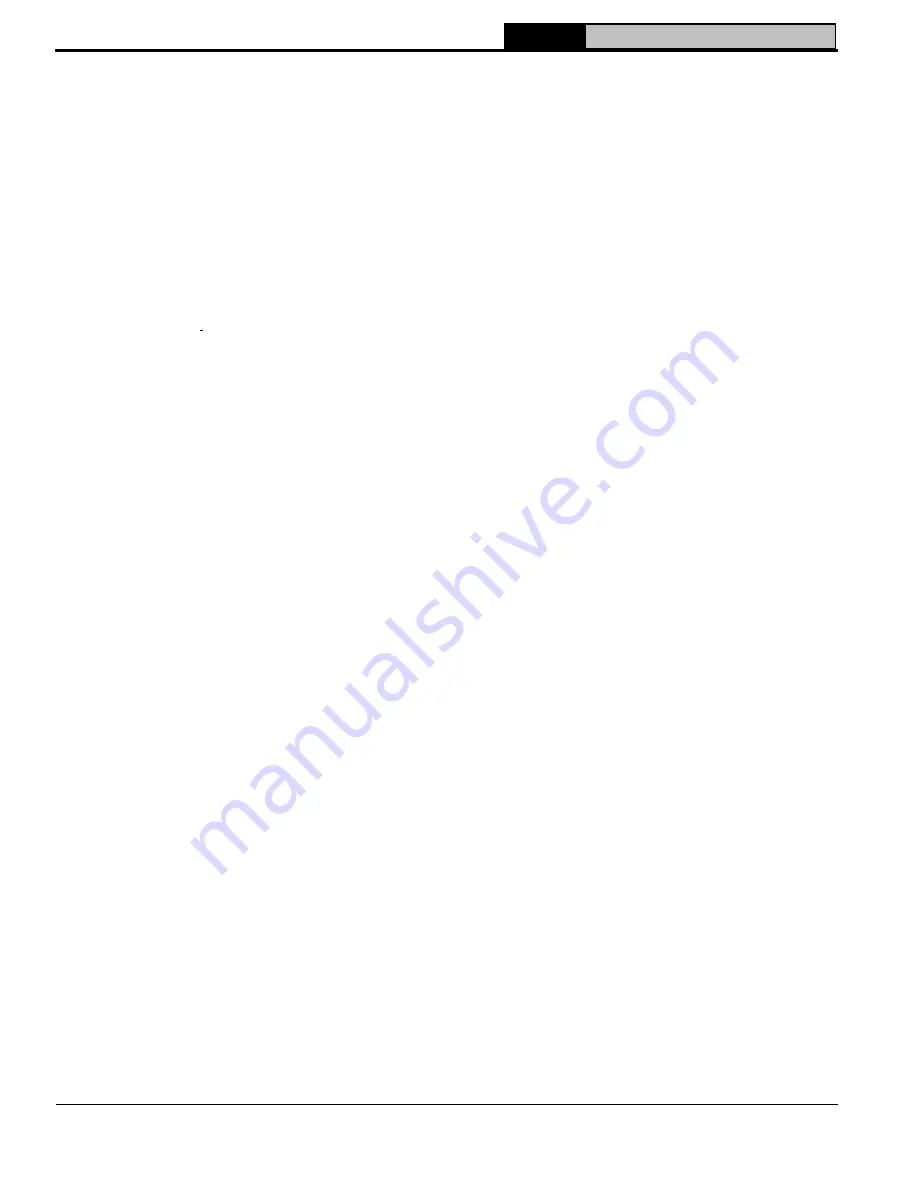
48
103536-13 - 2/24
MegaSteam
Installation & Service Manual
iii.
Start burner and operate sufficiently to
boil the water without producing steam
pressure. Boil for about 5 hours. Open
boiler feed pipe sufficiently to permit a
steady trickle of water from the surface
blow-off pipe. Continue this slow boiling
and trickle of overflow for several hours
until the water coming from the overflow
is clear.
iv.
Stop burner and drain boiler in a
manner and to a location that hot water
can be discharged with safety.
v
.
Refill boiler to normal water line. If water
in gauge glass does not appear to be
clear, repeat steps
(
i.
thru
iii.
)
and boil
out the boiler for a longer time.
b. Low pressure steam boilers such as the
MegaSteam™, should be maintained with
appropriate water treatment compounds.
Add suitable water treatment compounds
as recommended by your qualified water
treatment company.
c. Remove temporary surface blow-off piping,
plug tapping and reinstall safety valve.
Boil or bring water temperature to 180°F
promptly in order to drive off the dissolved
gases in the fresh water.
d. If unsteady water line, foaming or priming
persist, install gate valve in Hartford Loop
and drain valves in return main and at boiler
as shown in Figure 3-3 and proceed as
follows:
i.
Connect hoses from drain valves to floor
drain. Close gate valve in Hartford Loop
and open drain valve in return main. Fill
boiler to normal water level, turn on oil
burner and operate boiler at this water
level for at least 30 minutes after the
condensate begins to run hot, then turn
off burner.
Close all radiator valves. Remove all
supply main air valves and plug the
openings in supply main.
ii.
Draw about 5 gallons of hot water from
boiler into a container and dissolve
into it the appropriate amount of a
recommended boilout compound.
Remove safety valve from boiler and
pour this solution into boiler, then
reinstall safety valve.
iii.
Turn on oil burner and keep operating
while feeding water to boiler slowly. This
will raise water level in boiler slowly so
that water will be boiling hot and will
rise slowly into supply main and back
through return main, flowing from drain
hose at about 180°F. Continue until
water runs clear from drain hose for at
least 30 minutes.
iv.
Stop feeding water to boiler but
continue operating oil burner until
excess water in boiler flows out through
supply main and water lowers (by
steaming) until it reaches normal level
in boiler. Turn off oil burner. Drain boiler.
Open all radiator valves. Reinstall all
supply main air valves. Open gate valve
in Hartford Loop.
v.
When boiler has cooled down
sufficiently (crown sheet of sections are
not too hot to touch), close the drain
valves at boiler and in return main and
feed water slowly up to normal level
in boiler. Turn on oil burner and allow
boiler to steam for 10 minutes, then turn
off burner. Draw off one quart of water
from bottom gauge glass fitting and
discard. Draw off another quart sample
and if this sample is not clear, repeat
the cycle of draining the boiler and
return main and refilling the boiler until
sample is clear.
vi.
If the boiler water becomes dirty
again at a later date due to additional
sediment loosened up in the piping,
close gate valve in Hartford Loop, open
drain valve in return main, turn on oil
burner and allow Condensate to flow to
drain until it has run clear for at least 30
minutes while feeding water to boiler so
as to maintain normal water level. Turn
off oil burner, drain boiler, open gate
valve in Hartford Loop, then repeat Step
1 above.
NOTICE:
Check with local authorities or consult
local water treatment services for acceptable
chemical cleaning compounds.
9
Maintenance and Service
(continued)