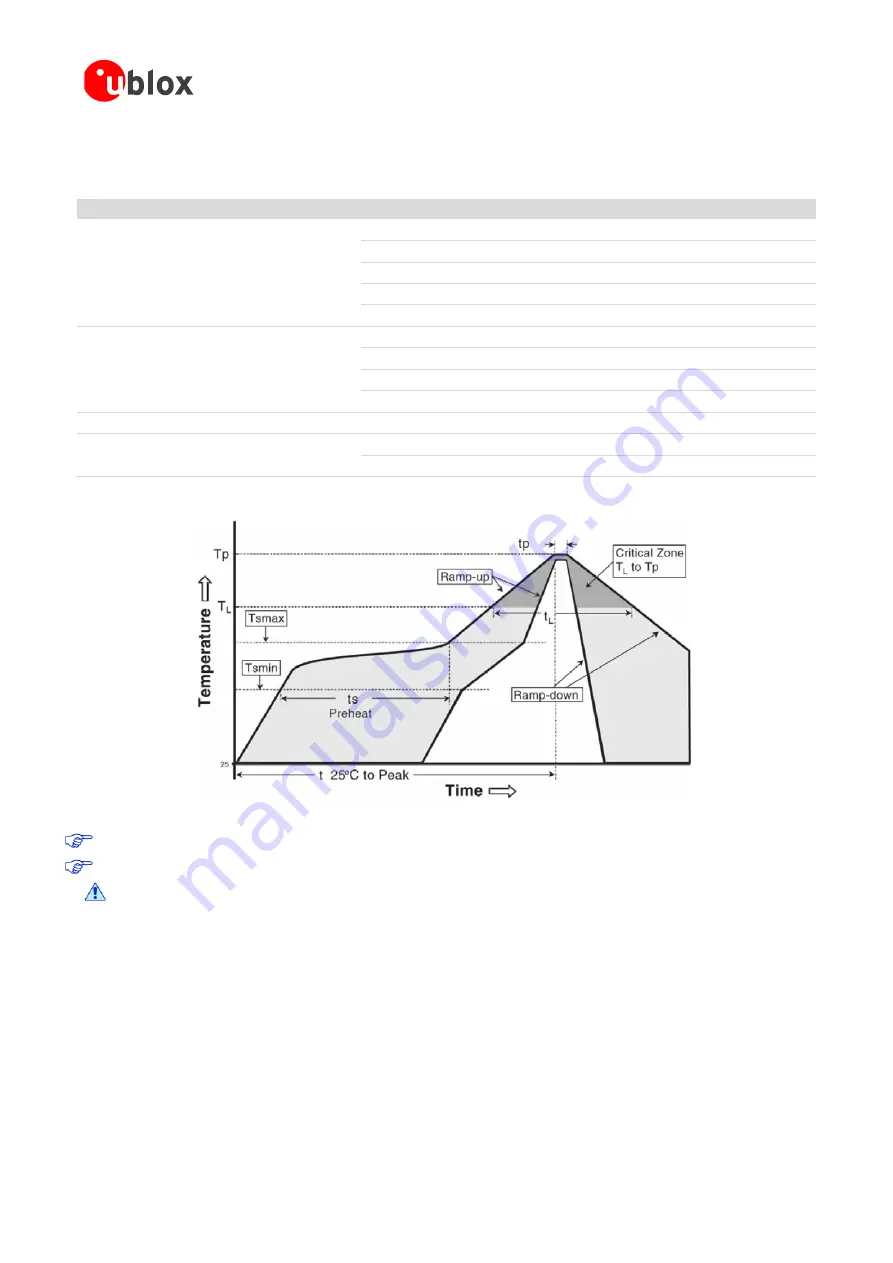
NINA-B1 series - System Integration Manual
UBX-15026175 - R06
Handling and soldering
Page 38 of 48
The reflow profile used is dependent on the thermal mass of the entire populated PCB, heat transfer efficiency
of the oven and particular type of solder paste used. The optimal soldering profile used has to be trimmed for
each case depending on the specific process and PCB layout.
Process parameter
Unit
Target
Pre-heat
Ramp up rate to
T
SMIN
K/s
3
T
SMIN
°C
150
T
SMAX
°C
200
t
S
(from 25 °C)
s
150
t
S
(Pre-heat)
s
110
Peak
T
L
°C
217
t
L
(time above
T
L
)
s
90
T
P
(absolute max)
°C
260
t
P
(time above
T
P
-5 °C)
s
40
Cooling
Ramp-down from
T
L
K/s
6
General
T
to peak
s
300
Allowed soldering cycles
-
1
Table 11: Recommended reflow profile
Figure 14: Reflow profile
Lower value of T
P
and slower ramp down rate (2 – 3 °C/sec) is preferred.
After reflow soldering, optical inspection of the modules is recommended to verify proper alignment.
Target values in Table 11 should be taken as general guidelines for a Pb-free process. Refer to
JEDEC J-STD-020C [7] standard for further information.
4.3.2
Cleaning
Cleaning the modules is not recommended. Residues underneath the modules cannot be easily removed with a
washing process.
•
Cleaning with water will lead to capillary effects where water is absorbed in the gap between the
baseboard and the module. The combination of residues of soldering flux and encapsulated water leads
to short circuits or resistor-like interconnections between neighboring pads. Water will also damage the
sticker and the ink-jet printed text.