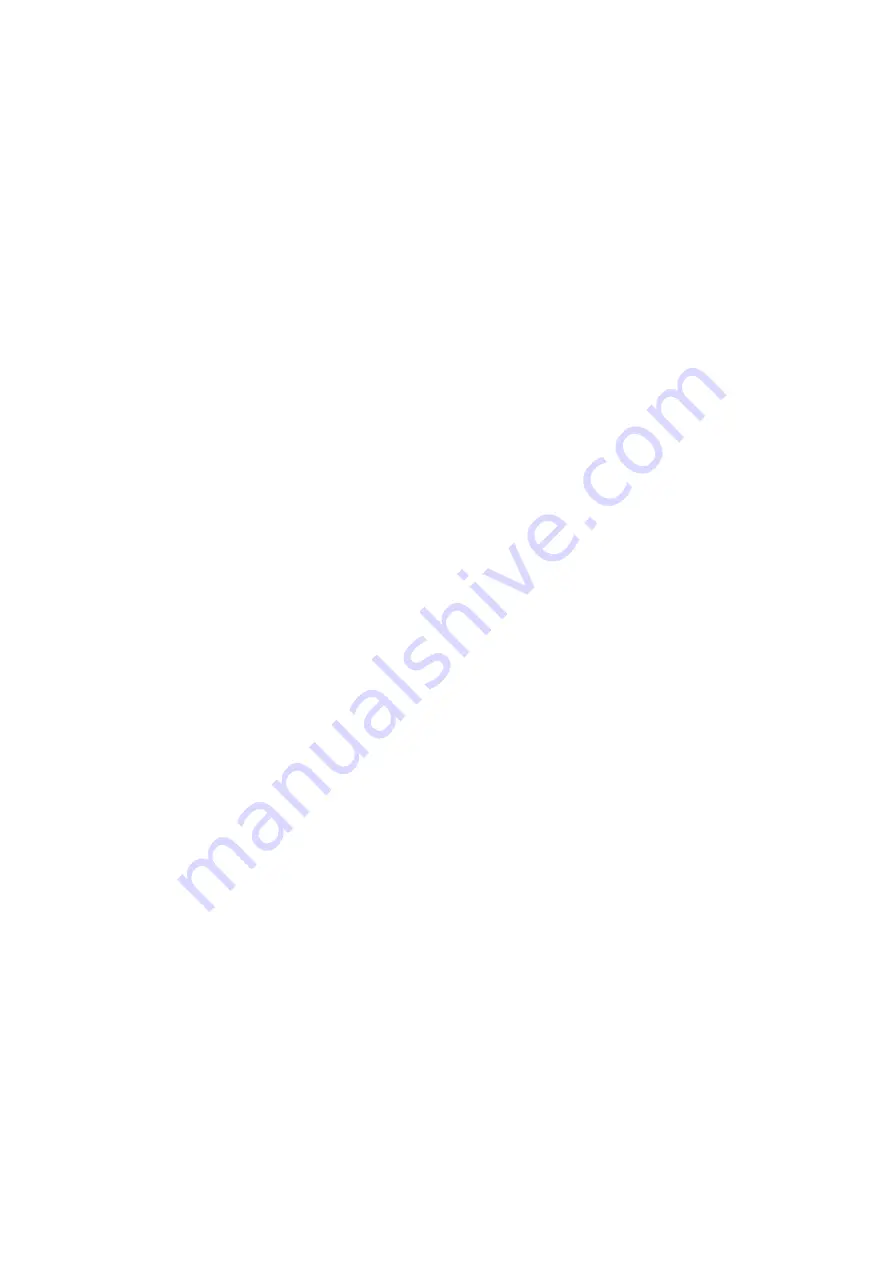
TYROLIT
Hydrostress AG
Page 8
Ring saw HRE400
Target groups and responsibility
Authorised personnel
Work on or with machines or systems from TYROLIT Hydrostress must be carried out by
authorised personnel only. Personnel are considered to be authorised if they meet the
necessary training and know-how requirements and have been assigned a precisely defined
task.
Manufacturer
Manufacturers of products supplied by TYROLIT Hydrostress are:
• TYROLIT Hydrostress
• A company explicitly named by TYROLIT Hydrostress
Within the context of an integrated quality assurance and safety control system, the
manufacturer is entitled to request from the operating company information about the
products.
Operating company
The operating company named by TYROLIT Hydrostress is the primary, legal entity responsible
for the correct use of the product and for the training and assignment of authorised personnel.
The operating company sets out the skills and level of training of authorised personnel.
Personnel qualifications
• A person with technical qualifications in a management position
• Relevant experience in personnel management and risk assessment
• Has read and understood the safety instructions
Operator (user)
User is the term employed by TYROLIT Hydrostress to designate a person who performs the
following work without direct supervision:
• Setting up the machines and systems from TYROLIT Hydrostress within the scope of their
intended use
• Performs and monitors work without direct supervision
• Localises faults and organises troubleshooting and fault correction without direct
supervision
• Maintenance
• Verifies safety devices are functioning correctly
Personnel qualifications
• Completed vocational training as a concrete tradesman or relevant occupational experience
• Introduction (basic training) in the operation of the electrical tool by a service engineer
Service engineer
A service engineer is the term applied by TYROLIT Hydrostress to a person who performs the
following work without direct supervision:
• Installs TYROLIT Hydrostress machines and systems
• Makes adjustments to machines and systems for which certain access rights are required
• Complex service and repair work
Personnel qualifications
• Specialist vocational training (mechanical / electrical engineering)
• Product-specific training at TYROLIT Hydrostress
2.4
2.4.1
2.4.2
2.4.3
2.4.4
2.4.5