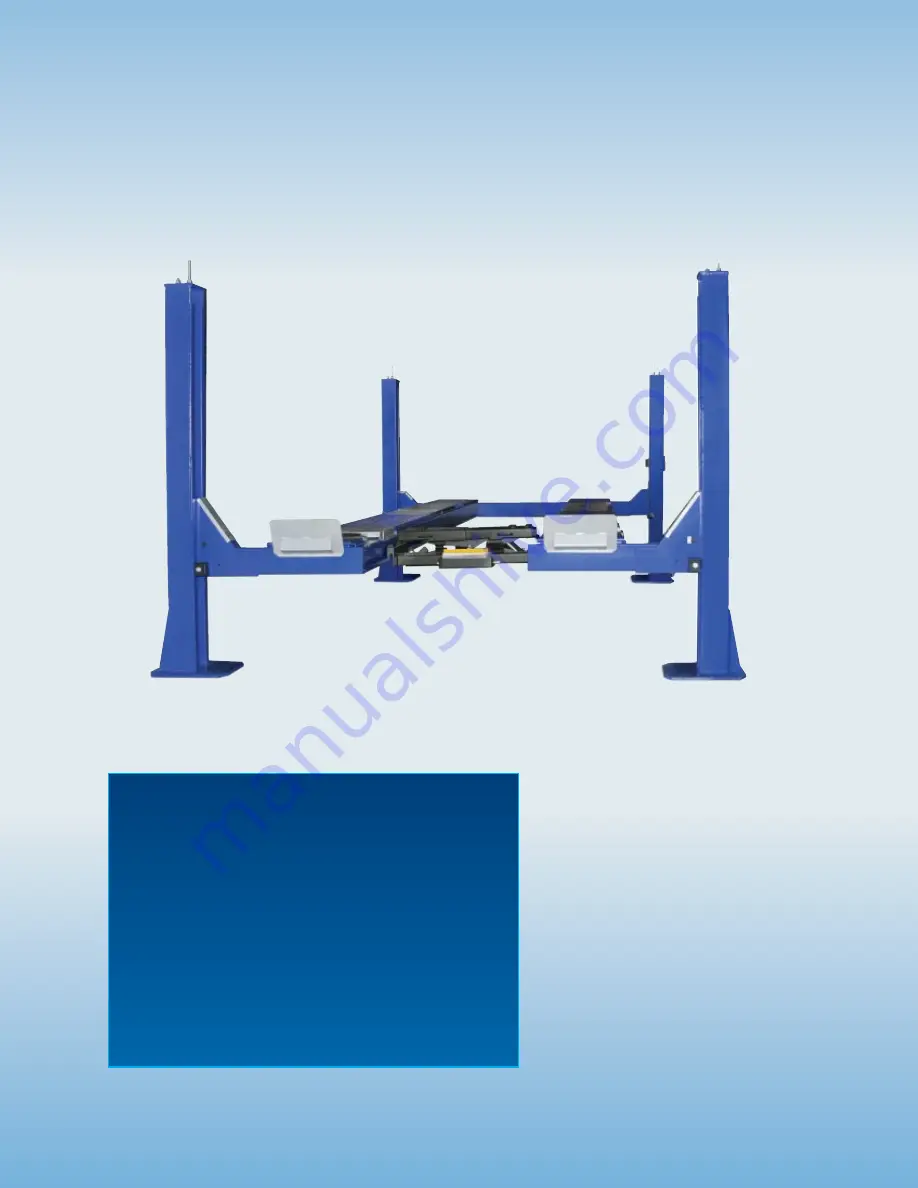
No obstructions! The open front design on our alignment lift allows
total access to front wheel adjustment points and with the cylinder located
under the track, there’s no power beam, eliminating risk of damage
to doors and mirrors. (Shown with optional rolling jack and turntables.)
14,000
LB
.
F
OUR
P
OST
O
PEN
F
RONT
A
LIGNMENT
L
IFT
FP
14KO-A
14,000 lb. capacity
Four post
Open front
Alignment lift
Features:
✦
14,000 lb. lifting capacity
✦
Cable drive
✦
Single point pneumatic safety
release mechanism
✦
20” wide non-skid,
diamond plate runways
✦
Powder-coated paint finish
✦
C-channel construction
✦
Hydraulic operation
for minimum maintenance
✦
Three turntable positions for
a wide range of vehicles
✦
Rear slip plates mounted on
ring roller bearings
✦
Fully adjustable lock stops
for easy leveling
S
PECIFICATIONS
:
FP
14KO-A
Lifting capacity
14,000 lbs.
Overall length w/ramps
24’ 3”
Overall width
11’ 6”
Width between posts
116”
Column height
7’ 8”
Lifting height
73”
Maximum wheel base (2 wheel)
208”
Maximum wheel base (4 wheel)
158”
Runway width
20”
Width between runways
43”
Power pack
2hp 220/230 vac 20 amps
Summary of Contents for FP14KO-A
Page 2: ...FP14KO A 14 000 lb Capacity Open Front Alignment Lift ASSEMBLY OPERATION MANUAL...
Page 3: ......
Page 7: ...3 Note All d Fig 1 imensions typical...
Page 17: ...PARTS DRAWING 2 III 38 2234 12 6 16 52 93 94 95 96 97 97 102 103 13...
Page 22: ...PARTS DRAWING 7 93 94 95 96 98 99 100 101 18...
Page 26: ......