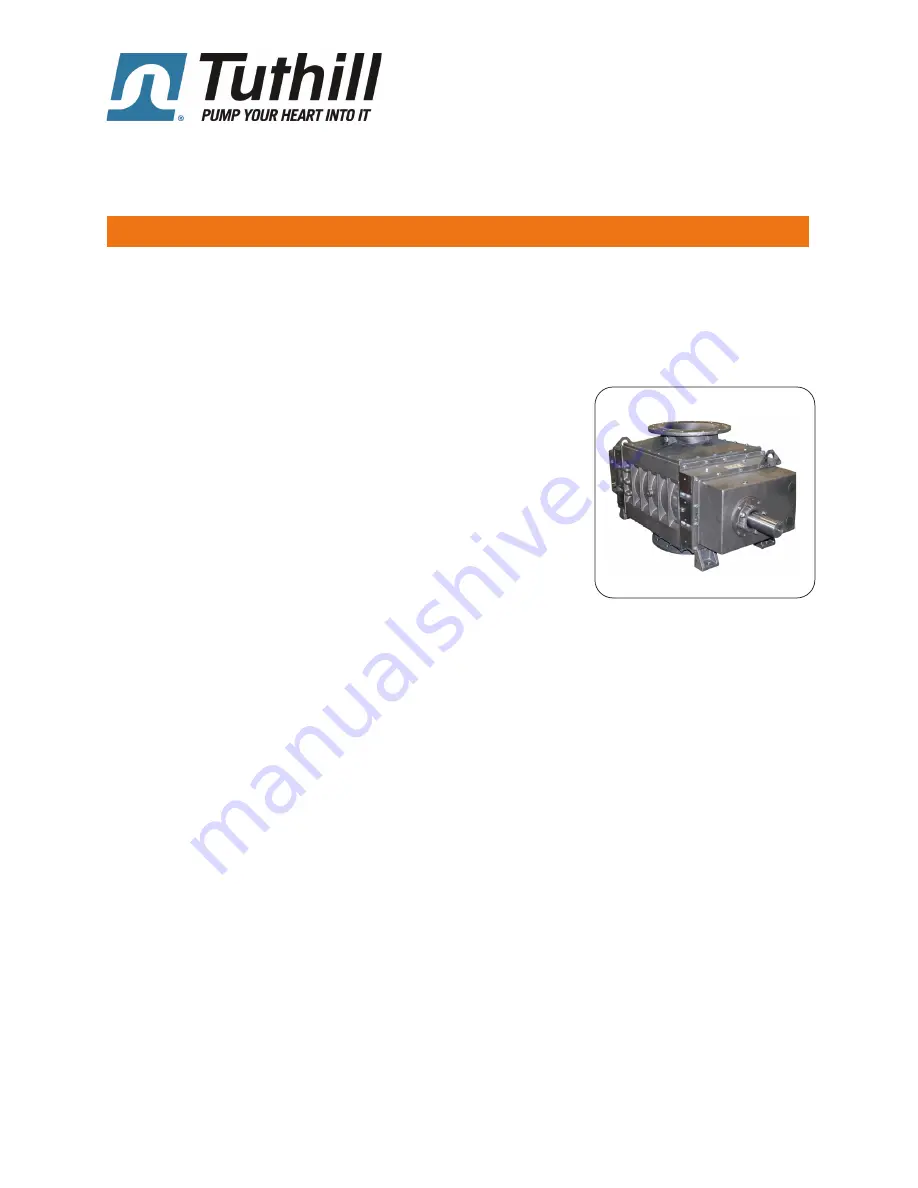
Tuthill
Rotary Positive Displacement Blower
PD Plus
Models
9016
9020
9027
Horizontal Air Flow
Vertical Air Flow
Horizontal Flow, Single Envelope
Gastight Vertical Flow, Single
Envelope Gastight Horizontal Flow,
Double Envelope Gastight Vertical
Flow, Double Envelope Gastight
OPERATOR’S MANUAL
WARNING: Do Not Operate Before Reading Manual
Operator
’s Manual: T
uthill PD Plus Rotary Positive Displacement Blower
Manual 2008 Rev A p/n 2008
Copyright © 2020 Tuthill Springfield
All rights reserved. Product information and specifications subject to change.
Tuthill Springfield | tuthillvacuumblower.com | 800.825.6937
Summary of Contents for PD Plus 9000 Series
Page 65: ......