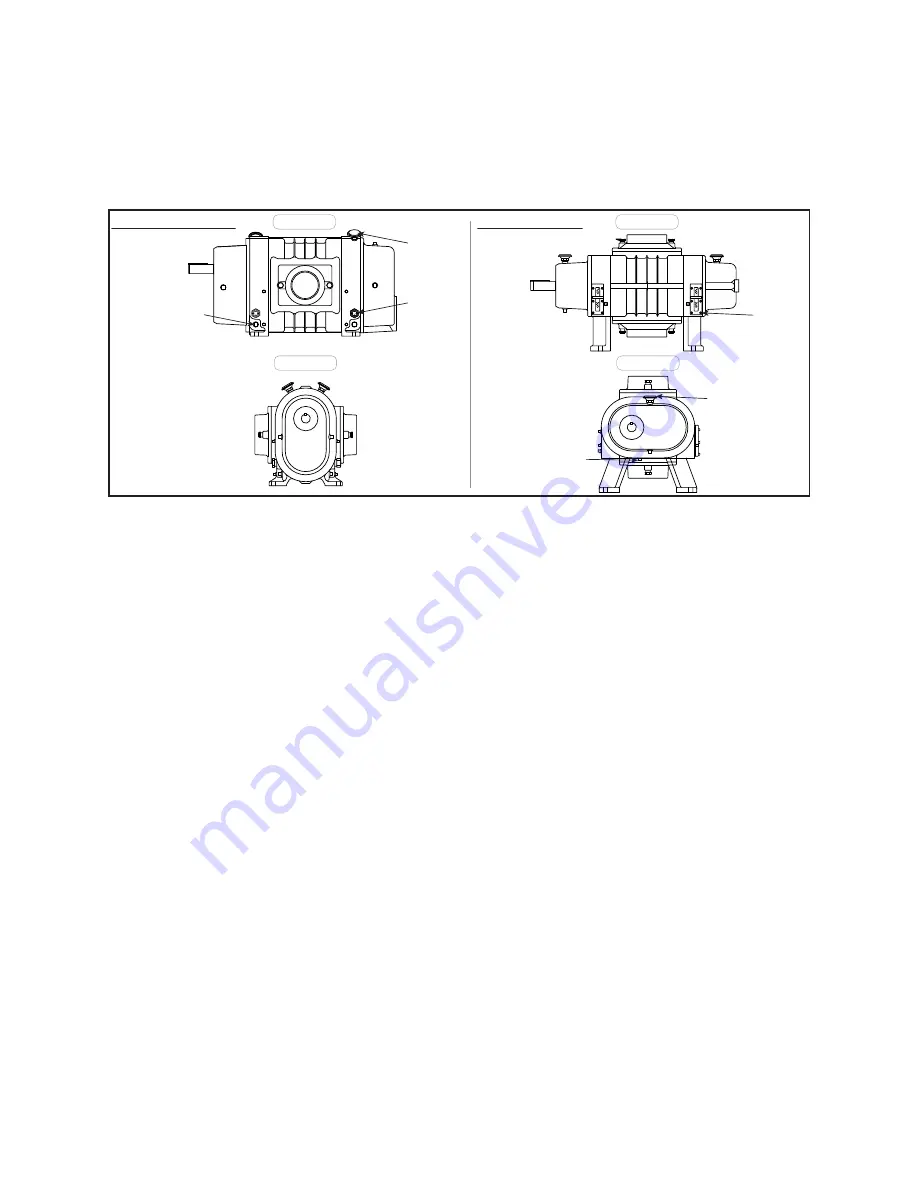
13
5.3.1 FILLING PROCEDURE
See Figure 5. Recommended lubricants are shown on page 35.
1. Remove
fi ll plugs or breathers from both gear end and drive end plates.
2. SLOWLY pour oil through fi ll until oil appears in the oil sight glass. Bring oil level to center of sight glass.
3. Verify oil level is at proper level in BOTH gear end and drive end sight glasses.
4. Replace
fi ll plugs or breathers that were removed in step 1.
HORIZONTAL FLOW
VERTICAL FLOW
END
END
SIDE
SIDE
MAGNETIC
DRAIN PLUG
(1) EA
END PLATE
MAGNETIC
DRAIN PLUG
(1) EA
END PLATE
OIL LEVEL
GAUGE
(1) EA
END COVER
OIL LEVEL
GAUGE
(1) EA
END PLATE
BREATHER
& OIL FILL
(1) EA
END PLATE
BREATHER
& OIL FILL
(1) EA
END PLATE
Figure 5 - Oil Fill, Drain Connections and Oil Level Gauges
5.3.2 FREQUENTLY ASKED QUESTIONS REGARDING LUBRICATION
What is the functional detriment if the “wrong oil” is used?
The lubricant is selected based on bearing and gear speed, and operating temperature. Too light
of a lubricant increases wear by not separating the sliding surfaces and it will not remove the heat
adequately. If the lubricant is too thick, the drag in the bearings is increased causing them to run hotter.
Since it is thicker, it will not fl ow as readily into the gears and it will reduce the available backlash.
Lubricants at our conditions are incompressible.
What is the functional detriment if the oil is not serviced?
If the lubricant is not serviced at the proper interval the shearing action in the bearing and the gears will
begin to take their toll and the lubricant will thicken, making matters worse. The unit will run hotter and
the wear on running surfaces will increase. Generally, the lubricant will appear dirtier, this is actually
material rubbed off the unit’s components. The discoloration comes from overheating the additive
package. An indicator of the breakdown of a lubricant is the increase in the TAN (Total Acid Number),
and a change in the base viscosity of ten percent.
Several things are happening as the lubricant goes through the unit. First, it is absorbing frictional
energy in the form of heat. This heat has to be dissipated through either surface contact with cooler
materials, or in a rest volume of lubricant. While reducing the friction, the lubricant is also going through
a shearing process and the molecular structure is broken down.
The result is that the lubricant will begin to thicken because of the shorter molecular chains and the drop
out of additive packages. The thickened lubricant will cause more drag, increasing the friction and heat,
and further degrading the lubricant.
Operation of the blower (environment, run time, speed, and pressure) has a direct effect on duty cycles.
Our published cycles are based on worst-case conditions.