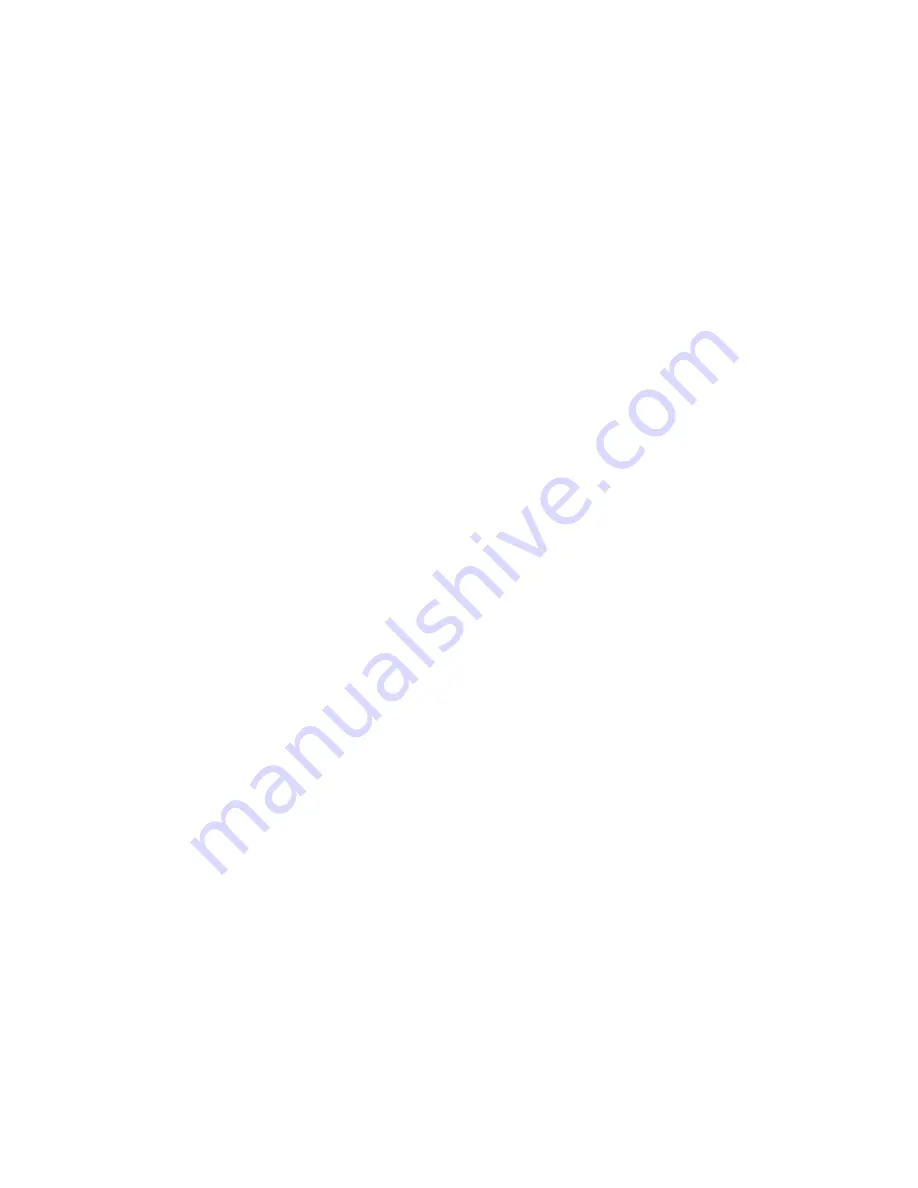
22
16) Install oil retainer rings and screws (14 & 30, spacer (57) (model
540C & 720C only), washer (25), screw (29), oil slinger and
dowel (21 & 68), and screw (69).
NOTE:
Oil slinger should always be mounted on lower rotor for
horizontal flow units. It can be mounted on either shaft for
vertical flow units.
17) Lay booster assembly down and torque timing gear nuts at this
time. See exploded view for proper torques.
18) The driven gear is made of two pieces. The outer gear shell is
fastened to the inner hub with four cap screws and located with
two dowel pins. A laminated shim, made up of .003 laminations,
separates the hub and the shell. By removing or adding shim
laminations, the gear shell is removed axially relative to the inner
hub. Behind the helical gear, it rotates as it is moved in or out
and the driven rotor turns with it, thus changing the clearance
between rotor lobes. Changing the shim thickness .006 will
change the rotor lobe clearance .003 or one half the amount.
EXAMPLE:
Referring the Figure 9 on page 17, check the
clearance at AA (right hand reading) and BB (left hand reading).
If AA reading is .009 and BB reading .003 by removing .006
shims, the readings will change one half the amount removed
or .003. AA should then read .006 and BB should read .006. The
final reading should be within .002 of each other.
To determine the amount of shim to add ore remove, subtract the
small figure from the larger. If the right side reading is higher
than the left side, remove shim. If the right side reading is lower,
add shim.
When removing gear shell from driven gear, it is not necessary to
remove gear lock nut. Make sure bolt locks are in place because
the dowel pins must come off with the gear shell.
19) Bend over lock tabs of gear lockwasher 936) and gear screw
locks. KMBD-850C, 1200C, 1600C, 2000C, 2700C models,
horizontal flow series (top drive only). Reinstall oil slinger (20)
to lower rotor and secure with washer (136 & 80) and cap screw
(396), if furnished. Not used on older models.
20) Install drive shaft, making sure both surfaces are clean and free of
all burrs. Drive shaft runout should not exceed .003 T.I.R. (Total
Indicator Reading). measured behind keyway.
21) Remove temporary cap screws from gear end plate and apply a
bead of sealer around end plate (not cover), encircling all holes,
and install gear cover (6) and secure with cap screws (26).
NOTE:
If cooling coil or manifold screw have been disturbed,
they should be retested with air pressure to check for leaks.
(Mechanical Seal Boosters only.) If leaks occur, disassemble and
replace o-rings.
Adjusting Rotor
Interlobe Clearance