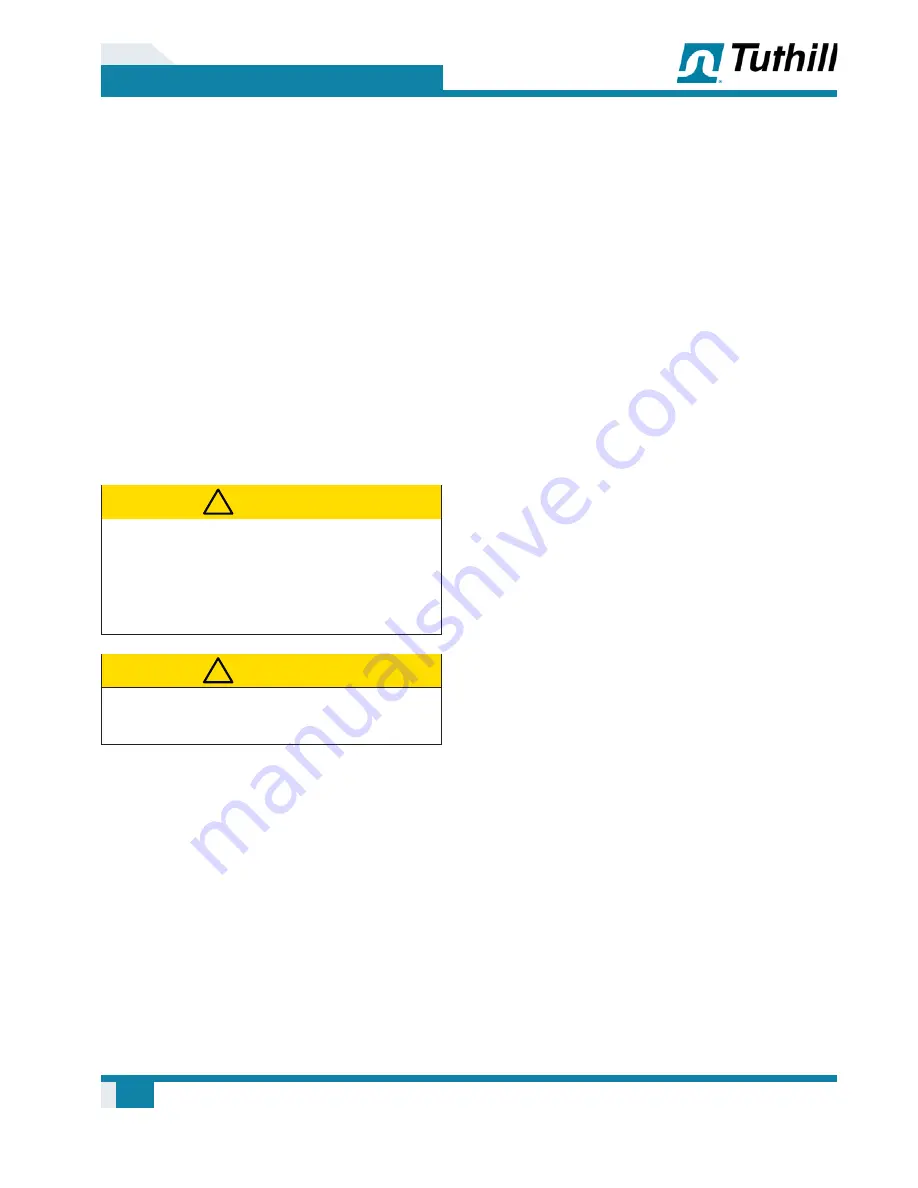
12
03
Installation
Manual 4804 Rev C p/n 004804 0000
MANIFOLD PIPING
The suction and discharge ports are distinguishable
by arrows on the pump, and are also shown in
Figure 3-1 on page 7
through
Figure 3-4
on page 10
. Note that the discharge port on
the KLRC-40 and KLRC-75 are at the shaft drive
end, whereas on the KLRC-125 to KLRC-950 the
discharge port is at the non-drive end. The discharge
leg should not have more than 24 inches of elevation
from the pump discharge
À
ange. Too much elevation
in this line would cause a buildup of back pressure,
overload the motor, and reduce the ef
¿
ciency of the
pump. During initial operation, install a screen across
the incoming port of the suction end casing to prevent
abrasive particles from entering the pump. Remove
any accumulation in the screen often enough to
prevent restriction of gas
À
ow. Remove the screen
when particulate accumulation no longer occurs.
CAUTION
!
Newly installed manifolding must be clean,
leak-free, and free of any weld slag. When the
process produces particulates, which could
damage the pump, use a suitable suction line
¿
lter.
CAUTION
!
The pump liquid sealant must not be allowed
to freeze in the piping or pump.
ELECTRICAL CONNECTIONS
Standard electrical motors supplied with Kinney
Liquid Ring Pumps are three-phase 230/460
volts 60 Hz, across the line operation. Pump
starting loads are low, as null load is developed at
maximum RPM. Reduced voltage when starting is
not required unless the power use is restricted by
the plant power supply. Connect the pump motor
and all applicable electrical accessories to a motor
controller that has over-current protection (heaters
or fuses) based on the full load current multiplied
by the service factor as stamped on the nameplate.
There should also be a suitable disconnect switch
between the controller and the power supply.
After the motor starter and disconnect switch have
been installed, turn the pump by hand to determine
that the impeller(s) is free to rotate. Check the
rotation by jogging the motor. An arrow on the drive
end casing indicates the direction that the pump
must rotate. If, after wiring the motor, the pump
turns in the wrong direction, reverse any two of the
power leads to the motor.
SYSTEM COMPONENTS
The following are some of the components available
for installation, either when the pump is ordered or
later to be installed in the
¿
eld. Accessories such
as solenoid valves and
À
ow switches can be added
to meet particular needs. The air/liquid separator
tank can be either the design that is mounted to
the
À
oor or the type that is suspended by the pump
manifolding, depending on the application.
INLET ELBOW: Used to adapt vertical pump inlet
to horizontal for mounting inlet check valve, etc.
A similar elbow may be used to connect pump
discharge separator tank.
INLET VACUUM GAUGE: Used to measure pump
inlet vacuum. Standard 3" W dial gauge has brass
bourdon tube and reads 0-30" Hg. The gauge is
mounted at the pump suction. Stainless is available
at an additional cost.
INLET VACUUM RELIEF VALVE: Used to control
pump inlet vacuum. If pump capacity exceeds the
system requirements at a preset vacuum, then the
valve will open and admit ambient air or connected
gas. Valve selection is dependent upon desired
vacuum setting and pump size.
INLET CHECK VALVE: Used to automatically isolate
pump from process chamber when the vacuum
pump is shut down, by blocking the back
À
ow of air
and sealant. Valve must be installed in a horizontal
position.
FLEXIBLE CONNECTOR: Used to accommodate
some motion and misalignment between pump
and system. Kinney Flexible Vacuum Connectors
with steel
À
anges and stainless steel bellows are
recommended.
INLET SHUT-OFF VALVE: Used to positively
isolate pump from process chamber. Ball valves are
supplied up to 2" NPT. Butter
À
y valves are supplied
for connections larger than 2" NPT.
Summary of Contents for KLRC Series
Page 6: ...iv Table of Contents Manual 4804 Rev C p n 004804 0000 ...
Page 33: ...27 08 Reassembly Manual 4804 Rev C p n 004804 0000 Figure 8 2 Bearing Driver Tool ...
Page 34: ...28 08 Reassembly Manual 4804 Rev C p n 004804 0000 Figure 8 3 Foot Alignment Tool ...
Page 37: ...31 09 Troubleshooting Manual 4804 Rev C p n 004804 0000 NOTES ...