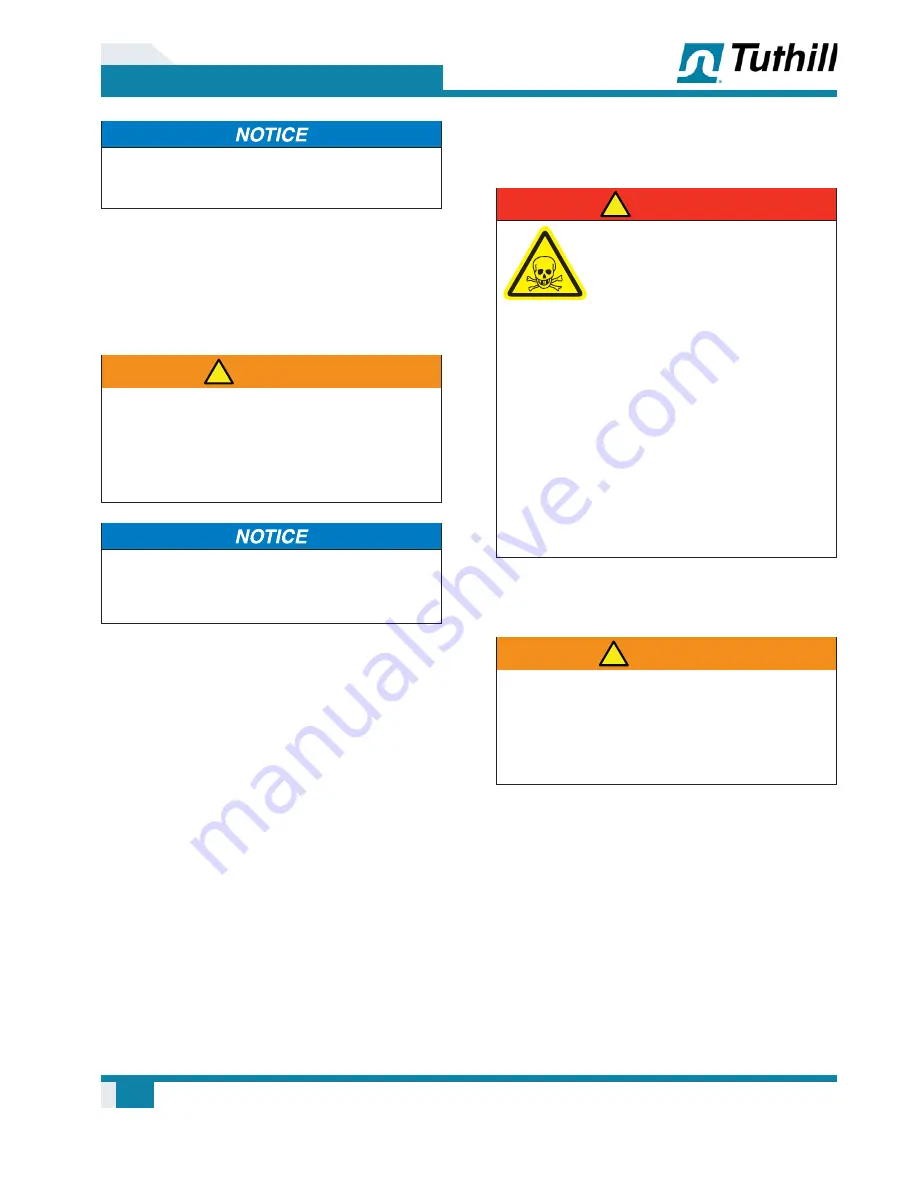
Manual 2017 Rev C p/n 2017
18
05
Installation
To avoid blowing out the drive shaft seal, do
not grease too rapidly.
OTE:
N
See Figure 5-3 for locations of grease
¿
ttings and grease reliefs for horizontal
and vertical
À
ow blowers.
PIPING CONNECTIONS
WARNING
!
Pipe loading on the blower should be
negligible as pipe loading can cause
distortion of the blower. Use proper supports
and pipe hangers to assure that there is no
loading.
Remove the protective covers from the inlet
and outlet ports and inspect for dirt and foreign
material.
Inlet and outlet connections on all blowers are
large enough to handle maximum volume with
minimum friction loss. Maintain same-diameter
piping. Do not support silencers by the blower.
Avoid stress loads and bending moments.
Be certain all piping is clean internally before
connecting to the blower. Place a 16-mesh wire
screen backed with hardware cloth at or near
the inlet connections for the
¿
rst 50 hours of use
until the system is clean. Clean the screen after
3 hours of operation and completely discard it
once the system is clean, as it will eventually
deteriorate and small pieces going into the blower
can cause serious damage. A horizontal or vertical
air
À
ow piping con
¿
guration is easily achieved by
rearranging the mounting feet position.
Hazards Associated With Hazardous
Process Fluids
DANGER
!
It shall be the responsibility
of the installer to ensure that
piping is adequate, sealing
between pipe joints is adequate
for the process
À
uids and
proper process and pressure
protection devices are in place.
It is also the responsibility
of the installer to assure that
process gases are not vented
in a manner that would be
hazardous.
Refer to the manufacturer of the
process media to assure that
proper safety precautions are in
place.
Blockage or Restriction
WARNING
!
Damage to the blower could occur if there is
blockage in the inlet or outlet ports or piping.
Care should be taken when installing the
blower to assure that there are no foreign
objects or restrictions in the ports or piping.