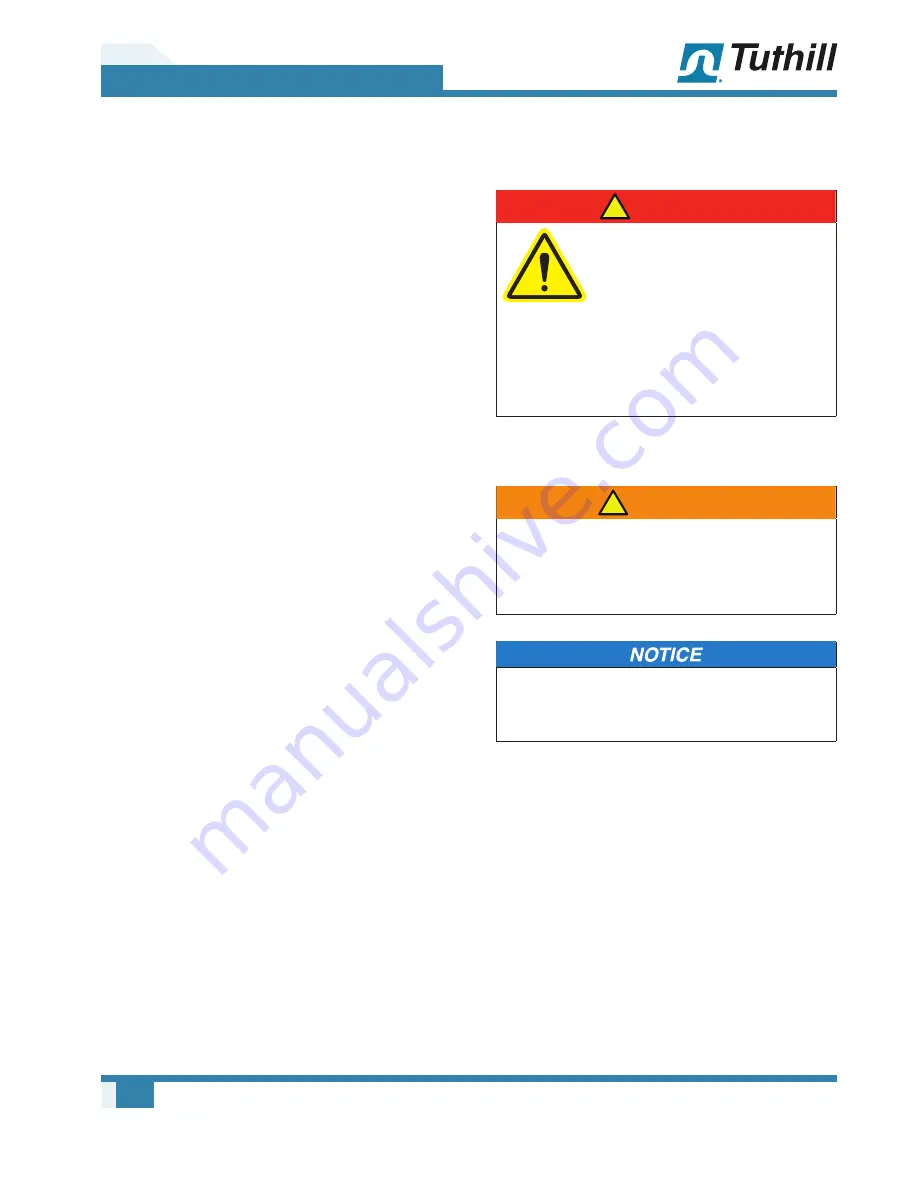
Manual 2003 Rev D p/n 2003
16
05
Installation
Frequently Asked Questions Regarding
Lubrication
What is the functional detriment if the “wrong
oil” is used?
The lubricant is selected based on bearing
speed, gear speed, and operating temperature.
If the lubricant is too light, it increases wear by
not separating the sliding surfaces and it will not
remove the heat adequately. If the lubricant is
too thick, the drag in the bearings is increased,
causing them to run hotter. Thicker lubricant will
not flow as readily into the gears and it will reduce
the available backlash. Lubricants at our conditions
are incompressible.
What is the functional detriment if the oil is not
serviced?
If the lubricant is not serviced at the proper interval,
the shearing action in the bearing and the gears
will begin to take its toll and the lubricant will
thicken. The booster will run hotter and the wear
on running surfaces will increase. The lubricant
will generally appear dirtier, caused by material
rubbing off the components. The lubricant will
discolor because of overheating. An indicator of the
breakdown of a lubricant is the increase in the Total
Acid Number (TAN), and a change of 10 percent in
the base viscosity.
Several things are happening as the lubricant
goes through the booster. First, it is absorbing
frictional energy in the form of heat. This heat has
to be dissipated through either surface contact
with cooler materials or in a rest volume of
lubricant. While reducing the friction, the lubricant
is also going through a shearing process and the
molecular structure is broken down.
The result is that the lubricant will begin to thicken
because of the shorter molecular chains and the
drop out of additive packages. The thickened
lubricant will cause more drag, increasing the
friction and heat, and further degrading the
lubricant.
Operation of the booster (environment, run time,
speed, and pressure) has a direct effect on duty
cycles. The published cycles are based on worst-
case conditions.
Hazards Associated With Breakdown
or Ignition of Lubrication
DANGER
!
There is a risk associated with the
lubrication media breaking down
and resulting in a hazardous fluid
or vapor. There may also be a
hazard associated with the ignition
of the lubrication media. Refer
to the lubrication manufacturer’s
applicable instruction for safety
precautions.
PIPING CONNECTIONS
WARNING
!
Pipe loading on the booster should be negligible
as pipe loading can cause distortion of the
booster. Use proper supports and pipe hangers
to assure that there is no loading.
Remove the protective covers from the inlet
and outlet ports and inspect for dirt and foreign
material.
Make sure that manifolding is no smaller than the
pump connections in order to minimize restrictions
to gas flow. Accurately align the mating flanges
to the inlet and discharge manifolding to prevent
distortion of the booster housing. Temporarily fit
a fine-wire mesh filter at the suction port if solid
particles are likely to be entrained into the air
stream, and remove the filter when particles no
longer appear. This is especially desirable on
new installations and when manifolds have been
welded. Fit the manifolding to and from the booster
with flexible connections to isolate vibrations,
absorb expansion and contraction due to thermal
change, and absorb misalignment differences. If
the booster is to be water-cooled, connect a clean
supply to the 1/8 in. NPT connection to the bottom