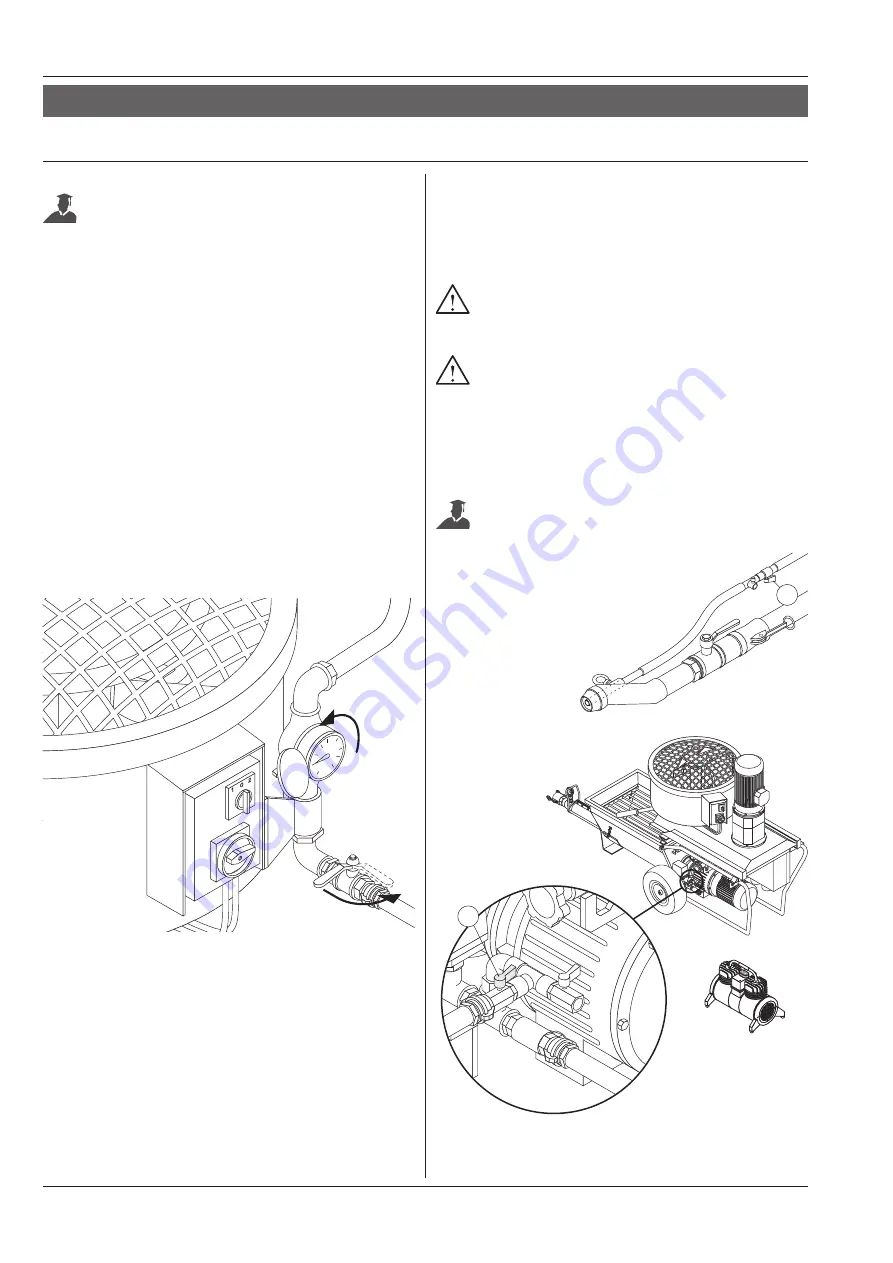
20
21
Conveying and spraying the mix
Drain the residual water of the pump calibration operation
from the hopper by opening the hatch located on the
bottom of the hopper.
Use nitrile gloves to protect against cuts and
scratches; preferably use models with CE 940072
certification.
During work use goggles, preferably with shockproof
polycarbonate lens, to protect the eyes.
Pour two or three bucketfuls (30 l) of slurry (50% water,
50% cement or lime) into the hopper.
If there is no slurry available but only ready-mix
materials, make them slightly more fluid than
normal.
• Open the air supply valve
(30)
located
on the machine and the air control
valve
(14)
on the mortar gun.
Preparing the batch
The mix should be plastic and within the grading
curve, as shown in point 4.2.
The pan mixer
(/MP version)
may be used to prepare the
batch.
When preparing mixes for traditional plasters, pour water
into the mixer; add 50% of the aggregate (sand), then
100% of the binder (cement) and lastly the remaining 50%
of the aggregate; add more water if necessary.
With traditional mortars it is advisable to use the vibrating
sieve to prevent the pump from being damaged by stones
or encrustation of material.
When preparing ready-mixed batches, follow the material
supplier’s instructions.
For correct batching of the water, a water gauge is
available (optional), which indicates the quantity of water
put into the mixer.
• Turn the water gauge so that the indicator is on position
0
.
• Put water into the mixer, turning the lever in the direction
indicated in the drawing.
• Close the valve, by positioning the lever at right angles
to the actual valve, when the litre-counter indicator has
reached the required quantity.
Prior to each new batch, put the water gauge indicator
to
0
to facilitate operations.
14
30
Summary of Contents for POLI T
Page 31: ...31 ...