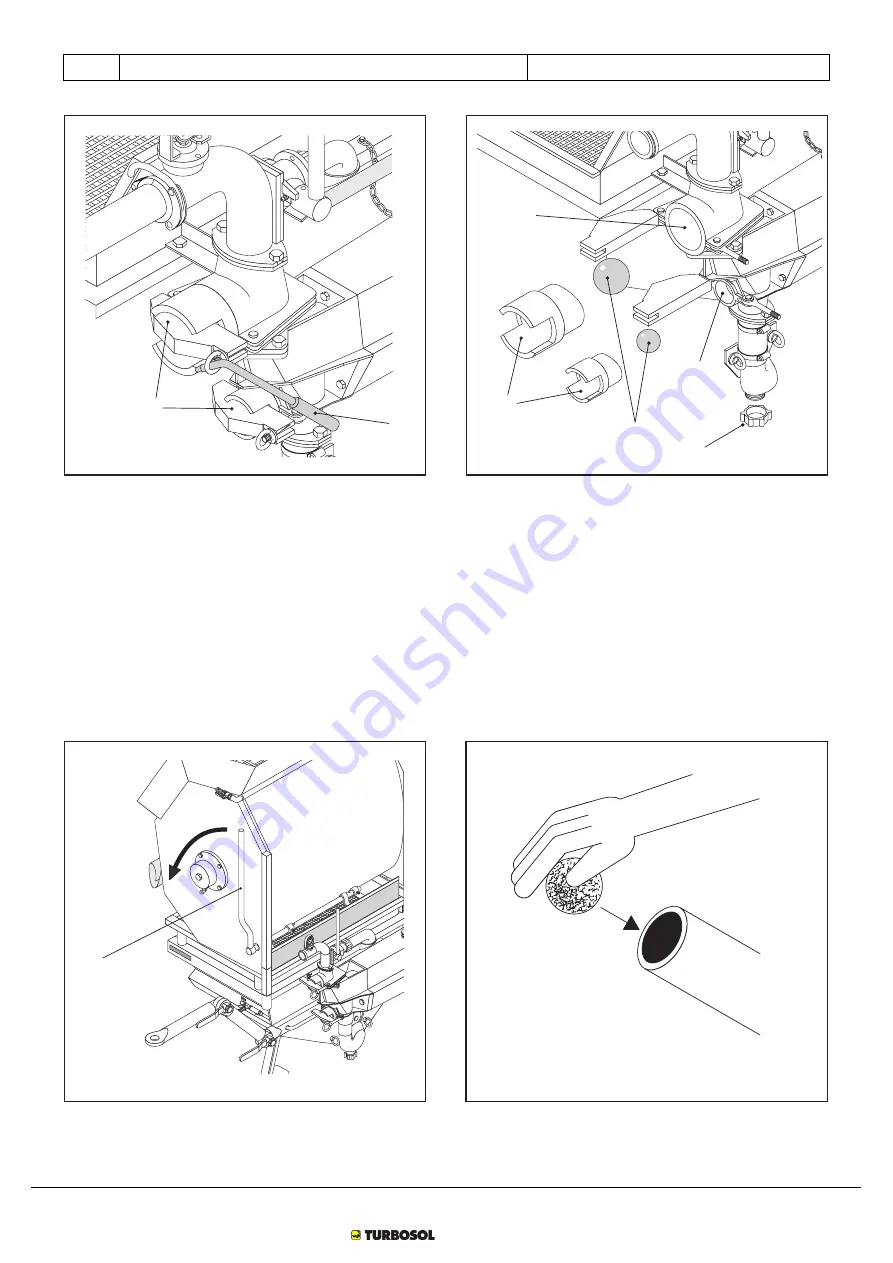
EN
UNI 30 E
17261 - 561.228
7 - USE AND OPERATION
Cap. 7 -
Pag.
13/14
THIS MANUAL IS PROPERTY OF
-
ANY TOTAL OR PARTIAL REPRODUCTION IS STRICTLY FORBIDDEN
4
5
2
3
1
2
1
FIG.44 FIG.45
Wash the entire plastering machine using a pressurised jet, more precisely: the hopper, the mortar diverter unit, the inside of
the valves and all dirty parts.
In the plastering machines with incorporated mixer (EMF version), first wash the mixer, taking care to open the material
discharge hatch with the lever (FIG.46-REF.1).
During washing operations make sure that the bodywork is closed in order to protect the motor and the other parts that could
be damaged.
When the plastering machine has been washed, wash the mortar piping.
Insert a washing sponge at the mouth of the pipe.
Re-connect the pipe to the machine and then re-mount the rubber balls, the various types of caps as well as the vibrating sieve,
in a way that the machine is ready for functioning again.
Make sure that the inspection caps and the junction fitting between the mortar pipe and the machine are well locked.
1
FIG.46 FIG.47
Fill the machine hopper with water, keeping it almost full until washing has been performed. Activate the machine.