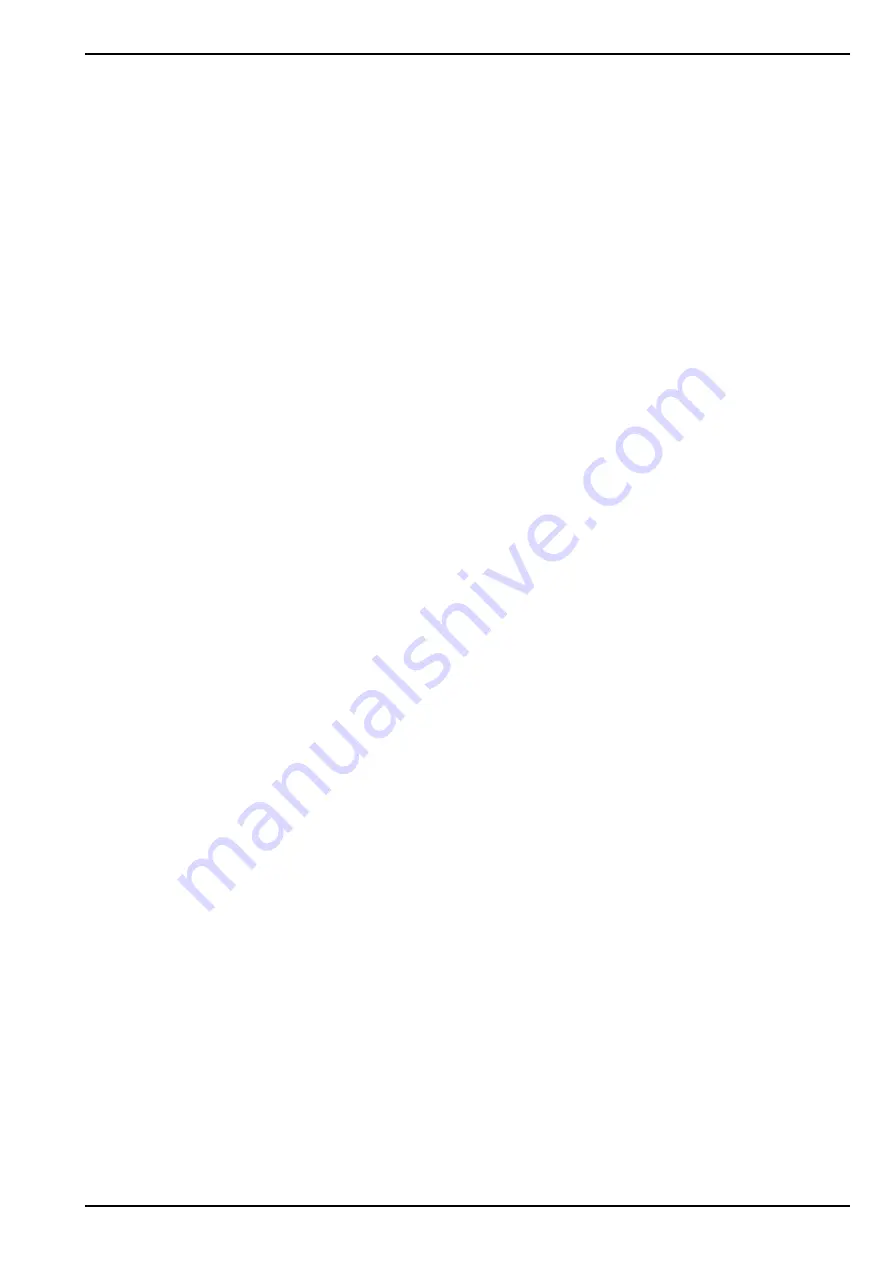
Safety
15
2.6 Safety notes for carrying out service,
inspection and installation work
The operator must ensure that all service, inspection and
assembly work is carried out by authorised and qualiied
personnel that has suficiently informed itself through detailed
study of the operating manual.
Work on the machine must, in principle, only be performed
while at a standstill. The machine's halting procedure
described in the operating manual must absolutely be
observed.
When carrying out maintenance on the lifted device, always
secure it with suitable supports.
Use suitable tools and gloves when exchanging the sweeping
drum and sweeping rail.
Lawfully dispose of oil and grease.
Directly after inishing work, all protection equipment must be
reattached.
Before restarting, the points listed in the sections on start-
up must be adhered to.
2.7
Unauthorised conversion and spare
parts manufacturing
Conversion of or changes to the machine are only
permitted after consultation with the manufacturer.
Original spare parts and accessories authorised by the
manufacturer provide safety. The use of other parts
invalidates the liability for the consequences thereof.
2.8 Modes of operation that are not
permitted
The operational safety of the machine is only guaranteed if
used as intended according to the operating manual (see
Chapter 1). The limits speciied in the data sheets must
not be exceeded under any circumstances.
Summary of Contents for Profi Gigant
Page 1: ...Profi Gigant Sweeping Machine Operating Manual ...
Page 2: ......
Page 4: ...Preface 4 ...
Page 6: ...Table of contents 6 ...