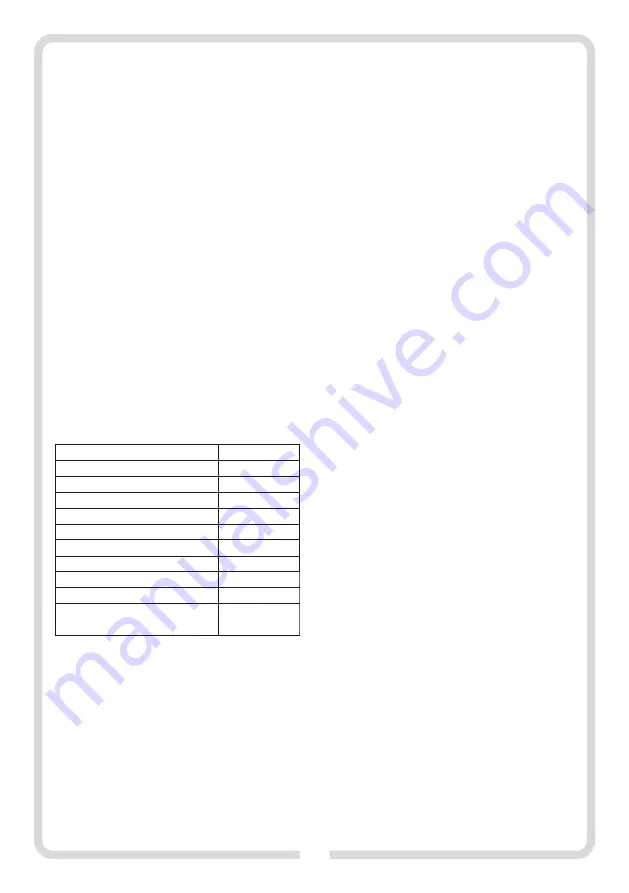
7
8
.
Protecting cover for the transmission belt
and the safety button (
5
) is released.
9
.
Opening to install a parallel guide bar
3. Prior to commencement of working with the tool check whether the
10
.
Chip bag
planing cutters are properly adjusted and reliably fixed (see
11
.
Limiter for grooving depth
«
Replacement of cutting blades
»
) and make sure that all moving part
12
.
Bolt to fix the limiter for grooving depth
of the tool are in sound operating condition, are not seized, cracked or
13
.
Angle bracket to fix the guide bar
damaged that may affect proper operation of the tool. Damaged
14
.
Bolt to fix the guide bar to the angle bracket
tools must be handed over for repairs before they can be used again
.
15
.
Fixing bolt of the angle bracket
4
. When your workplace is too far to plug the tool directly to the mains
16
.
Washer
socket, use an extension cord with a cable cross-section meeting the
17
.
Nut to fix the planing guide to the angle bar
tool requirements. Extension cords should be as short as possible.
18
.
Compartment for tools (spanners)
When in use extension cords must be fully uncoiled.
19
.
M8 wrench
NOTE:
While working with the plane always use protection means for the
20
.
Hexagonal socket wrench
upper respiratory tract (dust masks). Due to the reason of health protection
G
uide
bar for parallel planing
it is always necessary to collect shavings to the dedicated bag or use a
22
.
Transmission belt
vacuum cleaner as a dust aspirator. The vacuum cleaner must be capable to
Fig.
23
.
V-type groove for edge bevelling
collect dust or shavings released by machined materials and its intake hose
Fig.
24
. Bolts to adjust height of the cutter
is to be connected directly to the chip ejection outlet (
3
). DO NOT WORK
25
. Two-sided cutter
MATERIALS CONTAINING ASBESTOS.
26
.
Rear sole of the base shoe
27
.
Bolts for the cutter holder
28
.
29
.
Swivelled protective cover
30
.
Cutter holder
31
.
Cutting shaft
32
.
Front sole of the base shoe
Fig.
33
.
Fixing bolts for the cover of the transmission belt
OPERATION:
Switching on/off
ź
The device is provided with a safety button (
5
) that prevents from
unintentional switching the machine on. To start the plane
r
it is first
necessary to depress the button and only then one can push the On/Off
trigger (
6
) of the plane
r
and hold the trigger depressed. Due to safety
reason the trigger cannot be locked in the active position during
operating the plane
r
.
ź
Releasing the On/Off trigger (
6
) switches the machine off.
BEFORE YOU START:
1. Make sure that power supply parameters meet the requirements
provided on the tool nameplate.
2. Make sure that the On/Off trigger (
6
) of the plane is in the Off position
21
.
D:
H:
n
Installation of the chip bag
Insert the chip bag (
10
) nozzle into the chip ejector outlet (
3
) as deep as
Backup plate
possible (see Fig.
B
, p. 2).
NOTE:
The chip bag must be emptied as needed under regular basis. Detach
the bag, unzip it and remove collected chips and dust.
Do never put fingers into the chip ejector outlet!
When the outlet is
clogged, disconnect the tool from the power network and remove the
J:
obstacle with a thin stick or compressed air.
TECHNICAL DATA
:
n
Adjustment of cutting depth
(see Fig.
C
, p. 2)
The knob for adjustment of cutting depth (
2
) enables to set gradually the
cutting depth ranging from 0 to
3,
0 mm against the depth scale (
1
) with
the scale increment of
0
,5
mm.
- anticlockwise rotation of the knob reduces the cutting depth,
- clockwise rotation of the knob increases the cutting depth.
n
The vibration level value given refers to basic application of the tool. If the
n
Surface machining
tool is used for other applications or with other tools, or if it is not
Set the desired cutting depth and place the front sole of the tool shoe
maintained properly, the vibration level may differ from the values
(
32
) onto the machined surface.
given. The above-mentioned causes may lead to higher exposure to
NOTE:
Hazard of powerful reaction kicks! Start planing only after the
vibrations during the whole work time.
cutting shaft reaches the maximum rotation speed.
One must implement additional safety measures to protect the operators
Switch the tool on and hold it with two hands. Move the plane
r
smoothly
from exposure to vibrations, such as maintenance of the electric tool and
and uniformly down the entire surface to be machined. Both the front
work tools, assurance of proper hand temperature, or determination of
and rear soles of the shoe plate must firmly rest on the machined part.
the sequence of work operations.
CAUTION:
The power cord should be always within a safe distance from
rotating parts of the electric tool. Remember to keep always the power cord
behind the electric tool.
To achieve high quality of finishing it is recommended to keep pushing
the plane
r
really gently, trying to equalize pressure onto the plane shoe.
Rated frequency
50 Hz
Power consumption
900 W
Rotational speed max.
16000 rpm
Rated voltage
230-240 V
Sound power level
K=±3dB(A))
LwA (
102,2 dB(A)
Vibration level according to
2
(m
easurement tolerance
K=1,5 m/s )
EN 60745-1:2009
Protection class
II
Weight
91,2 dB(A)
0-3 mm
Planing depth
82 mm
Planing width
2
4,13
m/s
Sound pressure level
K=±3dB(A))
LpA (
2,9 kg
Summary of Contents for THG900
Page 2: ...2 10 3 B A 13 10 11 12 16 17 18 19 20 21 14 15 22 10 1 2 3 5 6 8 9 4 7 18 7 C 2 1...
Page 3: ...F 12 11 3 o 45 23 D 900W 0 E 21 13 11 17 14 16 12 15...
Page 4: ...4 0 G 28 32 H 27 24 19 26 29 30 31 25 23 I 25 20 J 8 33 K 22...
Page 16: ...RCD 16 THG900...
Page 17: ...17 a a...
Page 21: ...34 03 228 21 PROFIX...
Page 48: ...www profix com pl...