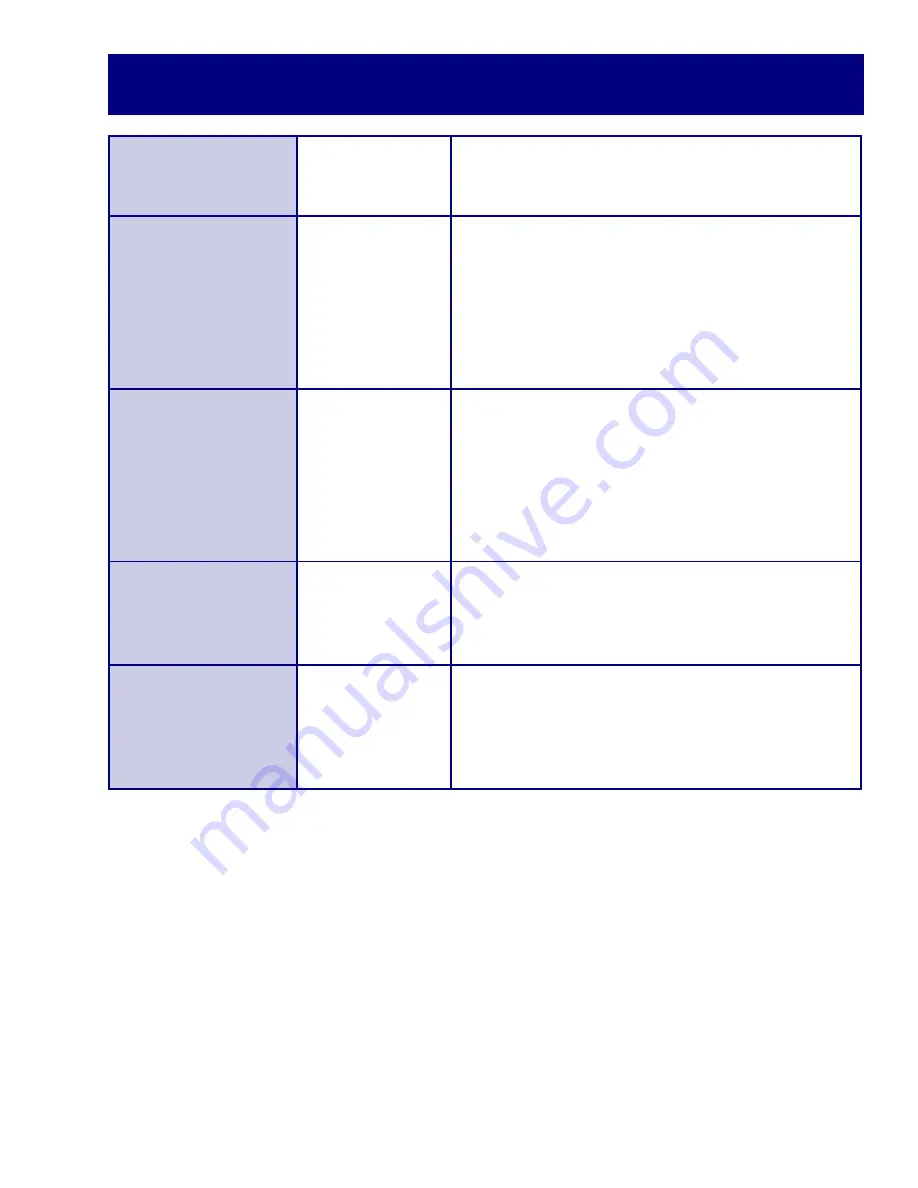
8
Features
♦
Smooth
arc
curve
targeted
for
small
to
medium
sized
diameter
studs
♦
Enhanced
Duty
Cycle
production
requirements
♦
Capable
of
up
to
100
feet
of
4/0
welding
cable
accommodates
a
large
variety
of
work
station
layouts
♦
Stepless
time
and
current
control
allow
for
infinite
settings
for
fine
‐
tuning
the
welding
output
♦
Stud
Job
Counter
that
can
be
reset
for
every
job
♦
On
‐
Demand
Fan
that
cycles
on
and
off
when
needed.
Weld
Range
1/4”
to
7/8”
Consistent
welding
regardless
of
stud
diameter.
Duty
Cycle
1/4”
thru
3/8”
1/2”
5/8”
3/4”
7/8”
Unlimited
22
to
24
per
minute
9
to
10
per
minute
4
to
5
per
minute
3
to
4
per
minute
Dimensions
Height
Width
Length
Weight
22”
(559mm)
25”
(635mm)
30”
(762mm)
390
Lbs.
(177kg)
Input
Voltages
230
/
460
/
575
VAC
3
Phase
60Hz
Fusing
Requirements
(Slow
acting)
230
/
120Amps
460
/
60
Amps
575
/
50
Amps
SC1900
Product
Specifications
**
Specifications
are
subject
to
change
without
prior
notification.