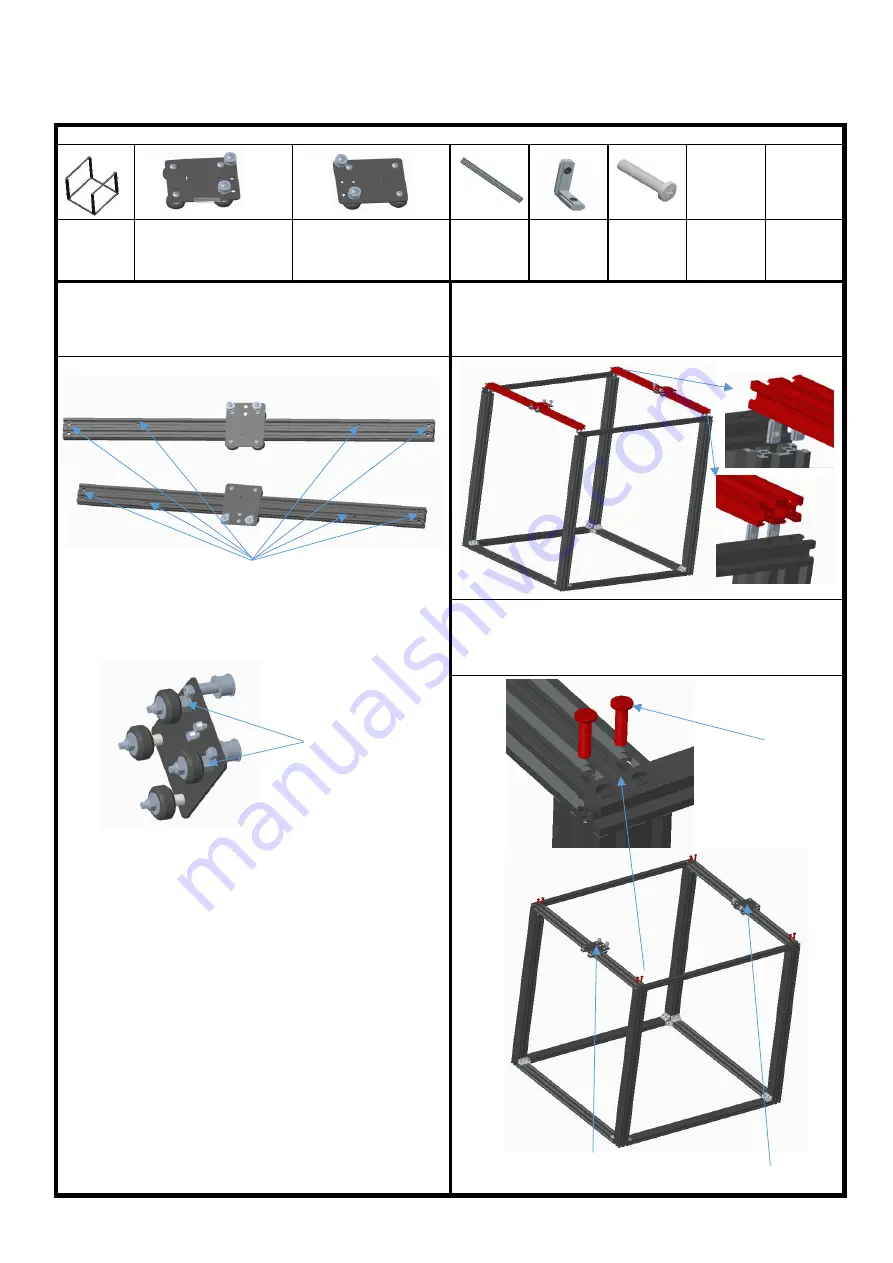
L angle code
PM6*25
screws
PM6*25
8pcs
3. Assemble the aluminum profile 5 components according to the position
shown in the diagram, align the L Angle code to the position of the
aluminum profile groove, and screw PM6*25 into the position shown in the
diagram.(do not lock tightly to facilitate subsequent adjustment)
L type angle
code
component
8pcs
Assemble material specification and quantity:
right sliding plate component
1pcs
Aluminum5
20*40*670
2pcs
Step 3: install the sliding plate
left sliding plate component
1pcs
underframe
1pcs
2. Put the end of aluminum profile 2 of the bottom frame
component into L Angle code, as shown in the figure;Screw on the
M5*5 meter.(do not lock tightly to facilitate subsequent
adjustment)
left sliding plate component right sliding plate component
1. Take 5,2 aluminum profiles, and insert the left and right
components of the slide respectively, as shown in the figure.Note:
two rows of pulleys are on the side of the middle hole, and the
sliding plate is on the side of the sink hole.
Pay attention to the sink hole
The eccentric nut
Adjust pulley clearance by rotating eccentric nut