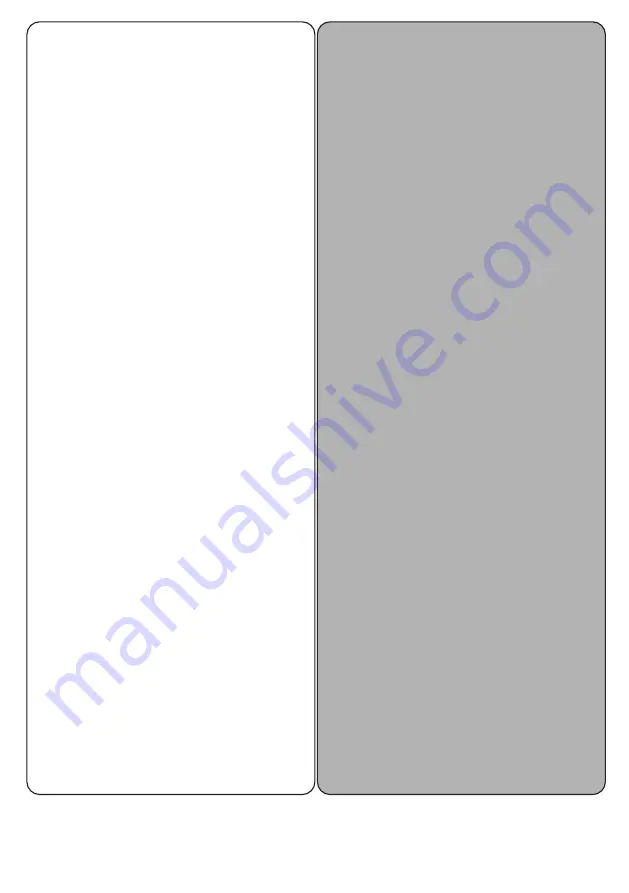
In the event of a product fault or complaint occurring,
the following procedure should be followed:
DO NOT REMOVE THE PRODUCT
1. Telephone Customer Experience on
024 7637 2222
having
available your details including post code, the model number
and power rating of the product, together with the date of
purchase and, where applicable, details of the particular fault.
2. If required, the Customer Experience Advisor will arrange for a
qualifi ed engineer to call.
3. All products attended to by a Triton service engineer must be
installed in full accordance with the Triton installation guide
applicable to the product. Every product pack contains an
installation guide, however, they can also be downloaded free at
www.tritonshowers.co.uk.
4. Our engineer will require local parking and if a permit is required,
this must be available to the engineer on arrival at the call.
5. If loft access is required for isolation or to complete a repair,
the loft must have a fi xed access ladder and be boarded, with
appropriate lighting from the access point to and around the
repair area.
6. It is essential that you or an appointed representative, who must
be over 18 years of age, is present for the duration of the service
engineer’s visit. If the product is in guarantee you must produce
proof of purchase.
7. Where a call under the terms of guarantee has been booked
and the failure is not product related (i.e. scaling and furring,
incorrect water pressure, pressure relief device operation or
electrical/plumbing installation fault) a charge will be made. A
charge will also be issued if nobody is at the property when the
service engineer calls or adequate parking/permit is not available.
8. If the product is no longer covered by the guarantee an up-front
fi xed fee will be charged before the site visit.
9. Your receipt must be retained as proof of purchase. Should proof
of purchase not be available on an ‘in-guarantee’ call, or should
the service engineer fi nd that the product is no longer under
guarantee, the engineer will charge the same fi xed price and
will request payment prior to departing. If payment is not made
on the day an administration charge will be added to the fi xed
charge.
10. If a debt is outstanding from a previous visit, or from any other
Triton purchase, Triton reserves the right to withhold service until
the debt has been settled.
11. Triton takes the health, safety and wellbeing of its employees
very seriously and expects customers to treat all staff members
with respect. Should any employee feel threatened or receive
abuse, either verbally or physically, Triton reserves the right to
withhold service.
Replacement Parts Policy
In line with AMDEA guidelines, Triton retains functional spares
for as long as there is a market for them and in most cases, well
beyond. Due to the vast array of product types, the life cycle of
products can vary and therefore so can the length of time parts
can be supplied. Spare parts can be ordered via our online spare
parts store or by telephoning Triton Customer Experience team
on
024 7637 2222
. Payment should be made by
credit / debit card (excluding American Express or Diners Card).
Payment can also be made by pre-payment of a pro-forma
invoice, by cheque or postal order.
Telephone orders are based on information given during
the call. Before contacting Triton, please verify your
requirements using the Triton website or your professional
installer. Triton cannot accept liability for incorrect part
identifi cation.
TRITON UK STANDARD GUARANTEE
This guarantee applies only to products installed within the
United Kingdom and does not apply to products used
commercially. This guarantee does not affect your statutory
rights.
With the exception of accessories, Triton guarantee the
product against all manufacturing defects for a period of
2 years
(for domestic use only) from the date of purchase,
provided that it has been installed by a competent person in
full accordance with the fi tting instructions.
All accessories such as shower heads, hoses and riser rails carry
a
1 year
parts only guarantee against manufacturing defects.
Any part found to be defective during this guarantee period
we undertake to repair or replace at our option without
charge, so long as it has been properly maintained and
operated in accordance with the operating instructions and
has not been subject to misuse or damage. This product must
not be taken apart, modifi ed or repaired except by a person
authorised by Triton.
What is not covered:
1. Breakdown due to:
a)
use other than domestic use by the property
occupants;
b)
wilful act or neglect;
c)
any malfunction resulting from the incorrect use or
quality of electricity, gas or water or incorrect setting of
controls;
d)
failure to install in accordance with this installation
guide.
2. Claims for missing parts once the product has been
installed.
3. Repair costs for damage caused by foreign objects or
substances.
4. Total loss of the product due to non-availability of parts.
5. Compensation for loss of use of the product or
consequential loss of any kind.
6. Call out charges due to an abortive visit or where no fault
has been found with the appliance.
7. The cost of repair or replacement of isolating switches,
electrical cable, fuses and/or circuit breakers or any other
accessories installed at the same time. Replacement of the
Pressure Relief Device that only activates when the shower
outlet is blocked is also excluded.
8. The cost of routine maintenance, adjustments, overhaul
modifi cations or loss or damage arising therefrom,
including the cost of repairing damage, breakdown,
malfunction caused by corrosion, furring, frost or exposure
to freezing conditions.
9. Callout charges where the water supply cannot be
isolated, this includes consequential losses arising from
unserviceable supply valves, or inaccessible product or
valves located in a loft space without suitable access.
For the latest Terms & Conditions please see:
www.tritonshowers.co.uk/terms
PLEASE NOTE PRODUCT REGISTRATION IS ONLY
AVAILABLE TO UNITS PURCHASED & INSTALLED IN THE UK
Triton Showers
Triton Road
Nuneaton
Warwickshire, CV11 4NR
Triton is a division of Norcros Group (Holdings) Limited
Customer Experience: 024 7637 2222
Trade Installer Hotline: 024 7637 8344
www.tritonshowers.co.uk
E-mail: [email protected]
E-mail: [email protected]
UK SERVICE POLICY
Triton reserve the right to change product specifi cation without prior notice. E&OE. © TRITON SHOWERS 2021
Summary of Contents for NOVA Thermostatic Series
Page 26: ...26 Electric shower ...
Page 27: ...27 Electric shower ...