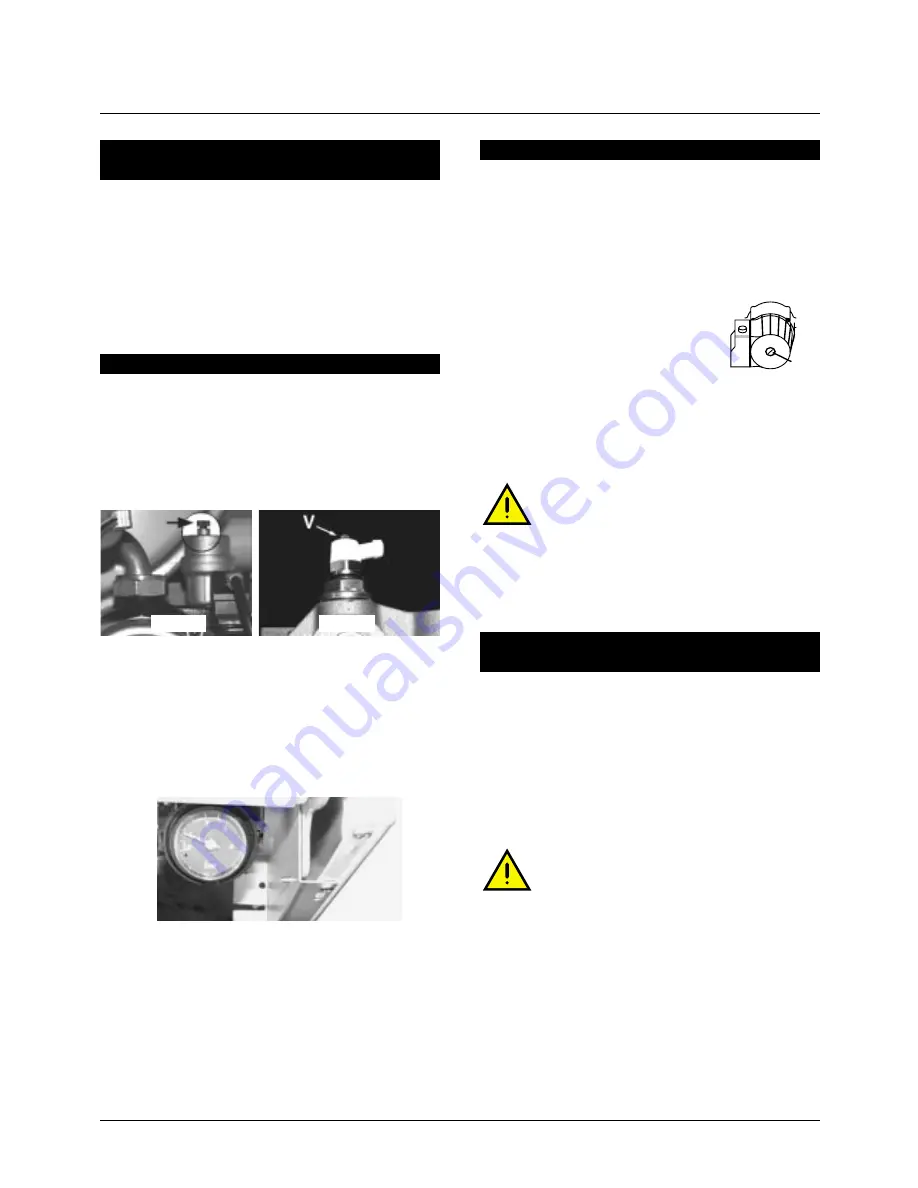
pag. 16
Before starting the boiler, check that:
- the gas line is not closed upstream of the appliance;
- the gas and water stopcocks are open;
- the appliance has been correctly connected to the
mains electricity and in such a way that the phase-
neutral polarity is observed;
- the system has been correctly filled with water (see
point 7.1).
In order to fill the system, gain access to the inside of
the sealed chamber, loosen the automatic escape
valve cap on the automatic air vent (fig. 7.1-1) and
screw V of the manual escape cock on the top of the
exchanger (fig.7.1-2) and gradually open the filling
valve tap.
The boiler operates correctly at a water pressure bet-
ween 1 and 1.5 bar this should be checked on the
pressure gauge located on the lower side of the boiler.
Once all the air has been vented from the system,
close the escape cocks and, when the desired pres-
sure has been reached, close the filling valve tap.
Control pressure gauge
manual air vent
automatic air vent
7.1 LOADING THE SYSTEM
7
PRELIMINARY CHECKS TO BE CARRIED
OUT BEFORE APPLIANCE START-UP
The water pressure is checked periodically on the
pressure gauge described in paragraph 7.1.
In order to reset the pressure to within the preset
values, gradually open the filling valve; when the desi-
red pressure has been reached, close the tap.
If, during normal operation, the appliance
frequently looses pressure or the boiler
safety valve comes into operation, con-
sult your installer or service engineer.
7.3 CHECKING SYSTEM PRESSURE AND POSSI-
BLE WATER RECOVERY
On initial start-up, the pump may be slightly noisy.
This may be caused by a small amount of air still trap-
ped in the pump. In order to let it out, proceed as fol-
lows:
- Loosen cap A (adjacent fig.) and
let out any air present.
- fasten cap A.
If pump not turning:
- remove screw A
- attempt to turn rotator knob using the
device on the shaft, taking care not to apply exces-
sive force so as not to damage it
- replace cap A checking that there are no water los-
ses
Before proceeding, take suitable precau-
tions to avoid possible scalds from hot
water and risks of damage to compo-
nents due to water losses from pump.
7.2 STARTING THE CIRCULATING PUMP
A
fig. 7.1-2
fig. 7.1-1
fig. 7.1-4
fig. 7.2-1
Summary of Contents for OPTIMA 28 CB
Page 1: ...OPTIMA 28 CB AND 28 SB WALL MOUNTED GAS BOILERS INSTALLATION INSTRUCTIONS...
Page 34: ......
Page 35: ......