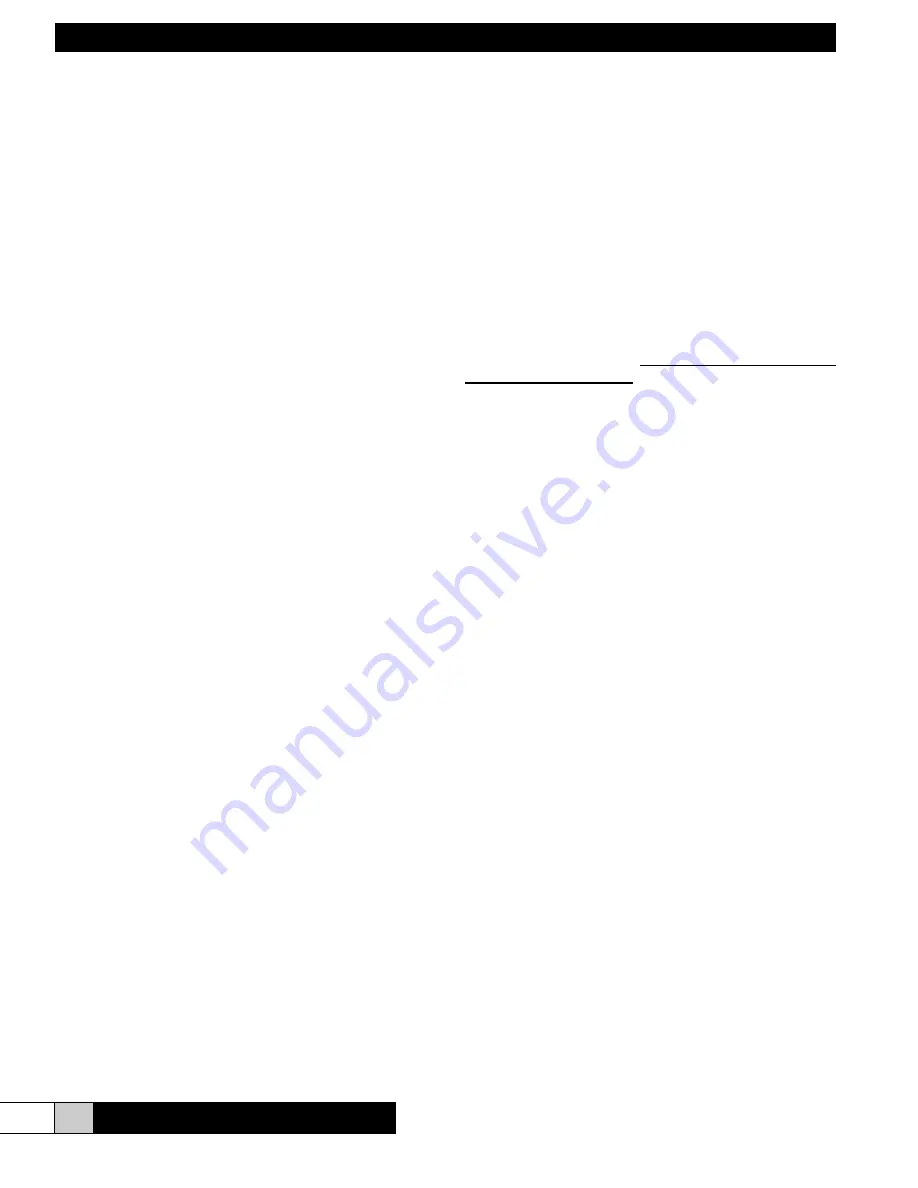
VOMP 600
I n s t a l l a t i o n , O p e r a t i o n , & M a i n t e n a n c e M a n u a l
4
www.trioniaq.com
III. INTRODUCTION AND OPERATION EXPLANATION
The TRION VOMP 600 is designed primarily for the filtration
of mists from ventilation air as found in the metal working
industries. The mists and smokes may be created from
either oil-based, synthetic, semisynthetic, or water-based
coolants like those used in cutting and grinding operations.
The unit, arranged vertical for upward airflow, is in the
collecting efficiency range of 95% and consists of an air
inlet chamber, a series of two or three filtration stages and
a blower.
Normally, a self-draining impingement baffle is used as a
pre-filter in the first stage of filtration. As the larger particles
of mist impinge on the baffle, they coalesce into droplets
that drain into the bottom of the unit to be drained away. In
lieu of the impinger, a metal mesh filter may be specified.
The second stage, if used, consists of an aluminum mesh
filter to remove larger coalesced droplets of liquid.
The third stage, electrostatic precipitator, is the primary
filtration method and consist of an ionizing/collecting cell to
remove up to 95% of particulate.
In application, the contaminated air is captured at its source
and transported to the unit through ducting furnished by
others. Upon entering the unit, the incoming air is diffused
by a baffle located inside the cabinet behind the inlet collar.
One inlet collar is factory installed. The contaminated air is
then pulled upward through the various stages of filtration
and the cleaned air is exhausted from the top of the cabinet
through a discharge grille. The unit should be located in the
vertical position and as close to the source of contaminant
as practical to minimize the length of ducting.
* Although the VOMP 600 is designed primarily for
mist or liquid particulate filtration, it may also be
used for the filtration of dry particulate.
IV. INTRODUCTION AND OPERATION EXPLANATION
HOOD AND DUCT DESIGN
The effectiveness of the installation is first dependent upon
the efficient capture of the contaminant at its source and
transporting it to the unit for collection.
In cases where adequate hooding is not provided by the
basic machine or the process creating the contaminant, the
design of the pick-up hood and the transport ducting should
not be over simplified. Due to the wide variety of applications,
this subject warrants a great deal more consideration than
can be given here. It is recommended that a recognized
text be consulted, such as Industrial Ventilation - A Manual
of Recommended Practice, available from:
American Conference of Governmental Industrial Hygienist
6500 Glenway Avenue, Building D-7
Cincinnati, OH 45211-4438
(Library of Congress Catalog Card #62-12929)
The duct between the pick-up hood and the unit should
be as short as possible and of adequate cross sectional
area to provide a transport velocity of 2000 feet per minute
(1 0.2 m/sec.). One air inlet collar is provided on the right
side of the unit cabinet at the bottom. The ductwork should
be sloped to prevent the pooling of liquids and sealed to
prevent leakage.
When ducting is utilized, the static pressure created by
the ductwork must be considered in conjunction with the
pressure that will be created by the build-up of contaminant
on the filters. Refer to the System Performance Curve in
Figure 2.
V. UNIT LOCATION
The unit should be mounted vertically with ample space
above the discharge grille (18” minimum, 457mm). Also,
provide ample service access, see Figure 1. If one unit
is to collect the contaminant from two sources, the unit
should be located so that the ducting from each source is
identical in length and configuration. If this is not practical,
the ducting should be designed and sized so that the static
pressure created by each duct run is identical or so that
adequate capture and transport velocities from each source
is assured.