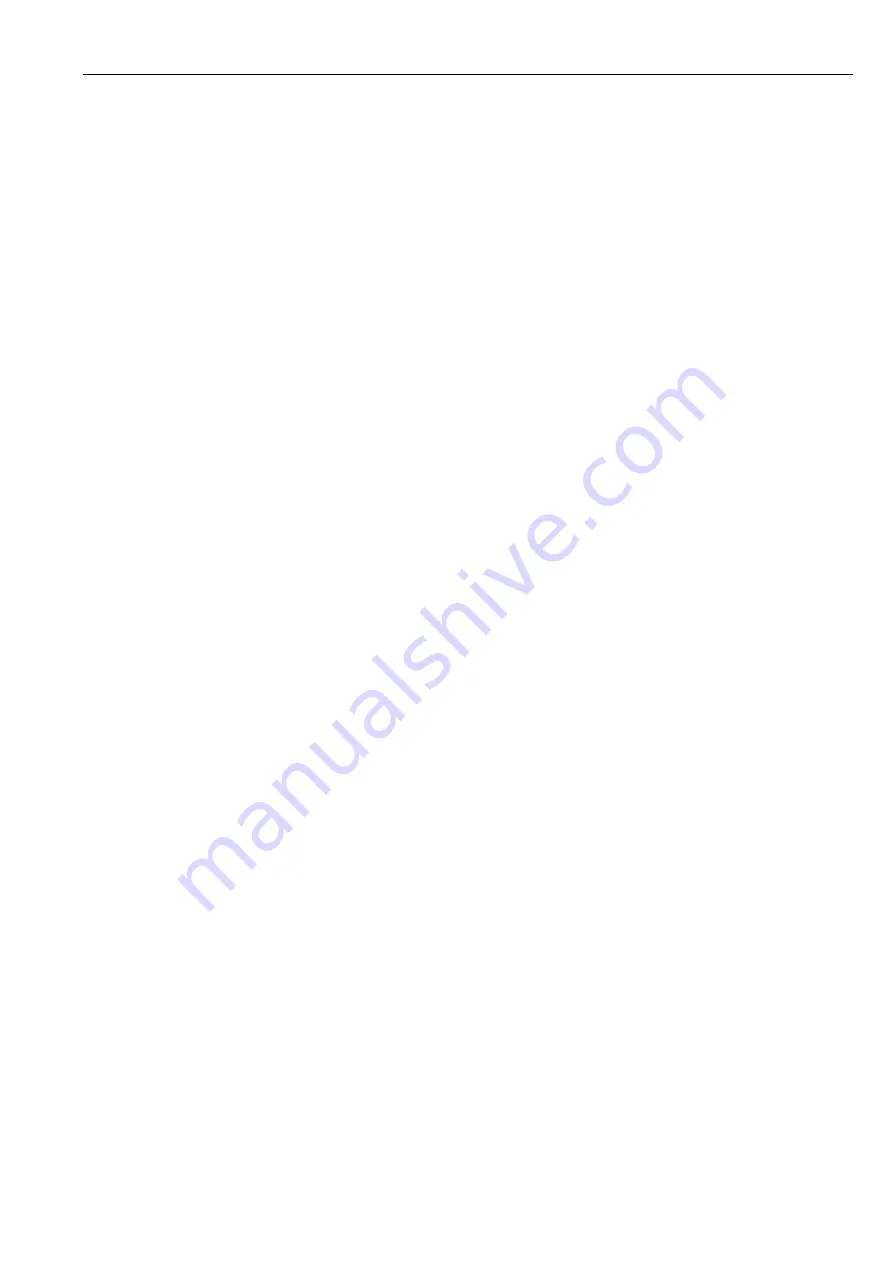
SIXpack 2 – Manual (V1.10 / January 29
th
, 2010)
8
3
System Start Up
3.1
System Start Up / Notes
When the SIXpack 2 is supplied with power it runs an internal initialization and a self-test of the internal
processor-system starts. If executed successfully a “0“ appears in the LED-display after a second. The SIXpack 2 is
operational now and can receive user commands.
Defective motor drivers can not be detected by the self test. Should the motor turn on and off during operation, a
constant high motor current or insufficient cooling of the drivers could be the problem. The motor driver chip
turns itself off for a short time when overheated. This condition should not occur in a normal operation condition.
If the SIXpack 2 reports a board temperature above or near 85°C, a forced air cooling or other means to reduce
heat dissipation, like reduction of stand by motor current is proposed to ensure a long product life time.
When an application requires detection of temporarily interrupted power supply of the SIXpack 2, this can be done
for example by signaling via external TTLOUT1 by programming it to a negative level. It will return to a high level
after a reset. The RS 232-interface usually receives a 0-byte after hardware reset.
3.2
Selecting Motors
When selecting motors, consider stepper motors with the lowest inductance possible, i.e. low coil resistance, to
obtain smoothest movements and the maximum possible RPM. On the other hand low coil resistance increases the
required motor current. Therefore you should choose the motor with the lowest inductance possible which
delivers the required torque at a coil current of approx. 1000 to 1400 mA. Highest possible operating voltage of
the SIXpack 2 results in high RPM also. With higher coil resistance or a too low operating voltage the duty factor
of the chopper drivers increases. When exceeding 50% a chirping noise can occur in the coils.
3.3
Length of Wires
motor wires:
typically < 3m (use twisted pair wire)
RS 232:
typically < 3m
CAN, RS485:
can be > 30m
3.4
Grounding
For a good ESD protection the electronics must be connected effectively with ground. Therefore two holes are
provided on the PCB with ground contacts.
If the electronics is delivered without housing, these two screws must be connected to ground.
If the electronics are built-in in the housing the protection tape must be taken away of the two fixing drilled holes
on the back side. The electronics must now be grounded via these two blank areas.
3.5
Improvement of the EMC-Conduction
To improve the cable-bound conducted emission, a ferrite-clip should be clipped over the supply circuit.
3.6
Further Information:
For further information please view our homepage (
www.trinamic.com
). You will find help under “frequently
asked questions”. You also have the possibility to send us an e-mail via a contact sheet located on the same site.