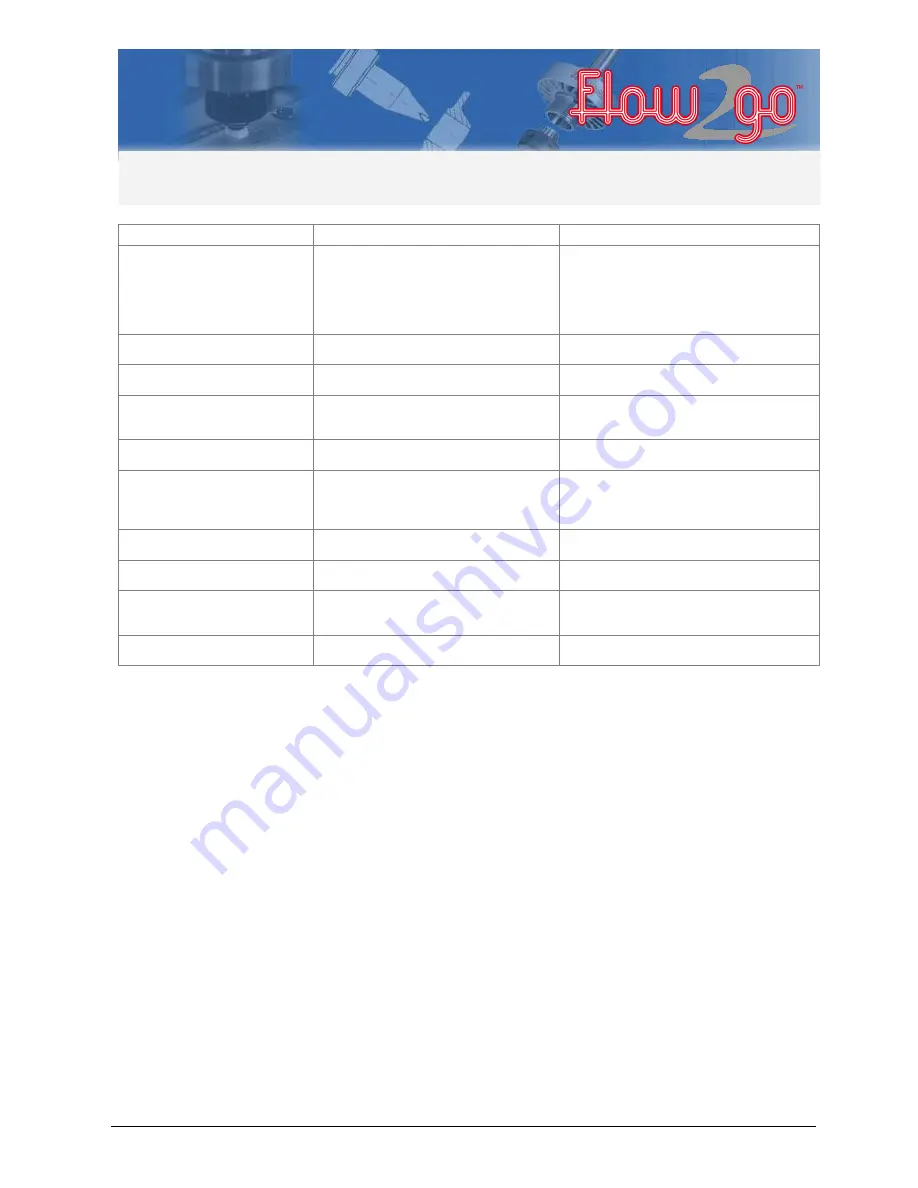
Instruction Manual
Mobile thermal drilling
12
© Copyright by Flowdrill GmbH
Olbrichtstr.18
69469 Weinheim
7. Trouble shooting
Problem
Cause
Remedy
Motor does not start
- No mains voltage
- Rotation direction not selected
- Switch not clearly positioned
- Switch or lead faulty
- Carbon brushes worn (observe flashing
light!)
- Check mains voltage
- Preset rotation direction
- Have switch or lead replaced
- Have carbon brushes replaced
Motor running, but the spindle
does not rotate
- Switch is not clearly positioned
- Check and correctly set switch position
Motor stops when drilling
- Contact pressure too high
- Electronics switch off automatically
- Reduce contact pressure
- Wait a short time, then start again
Drilling not possible in spite of
correctly set rotational speed
- Tool also rotates in the collet
- Material thicker than permitted
- Re-clamp tool
- Replace collet
- Use thinner material
Workpiece and/or vice is raised
when flowtapping
- Workpiece clamping not sufficient
- Vice not secured
- Re-clamp workpiece
- Secure vice
Flowtap gets stuck
- Thermal drill hole not completely
tapped (material too thick)
- Bush/bush length too conical
- Lack of lubrication
- Fully tap bush
- Manually unscrew tool
- Use thinner material
- Lubricate tool
Tool holder rotates with left turn
of the spindle
- Retaining screw missing or is not firmly
tightened
- Tighten or reorder retaining screw
Drill is pushed upwards out of
the clamp during drilling
- Clamping screw not tightened
-Tighten clamping screw
The feed is very difficult to
access without drilling
- Foreign bodies between the guides
- The pre-tensioning of the guide is too
high
- Remove contaminants (dirt, chips etc.)
- Re-adjust the guide system in accordance
with maintenance instructions
The slide moves downwards on
its own due to its own weight
- The pre-tensioning of the guide is too
low
- Re-adjust the guide system in accordance
with maintenance instructions