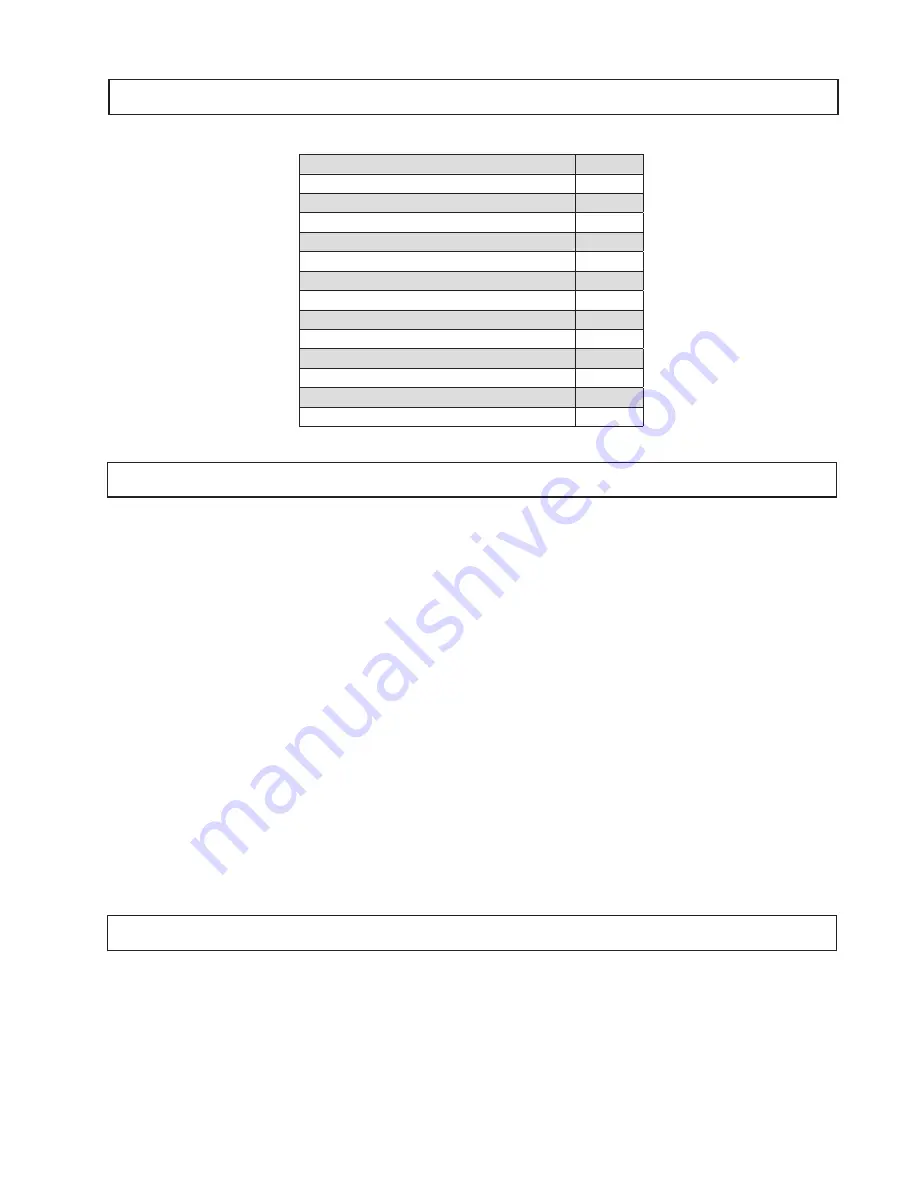
4
Read, understand and follow all safety instructions and
operating procedures. If you do not understand the
instructions or if conditions are not correct for proper
operation, do not operate the machine. Consult your
supervisor or other responsible person.
*Check that the trigger switch is not locked on.
*Check that the manual return valve is closed.
*Make sure that the proper punch and die are installed
correctly. See
Die Selection
and
Proper Punches and
Dies
on next page.
*If you are using the hole locator gauge, adjust it to the
proper distance. See
Hole Locator Gauge Adjustment
on next page.
*Plug the power cord into the proper power supply.
OPERATING PROCEDURES
*Position the puncher at the proper location on the
workpiece using the hole locator gauge or by locating the
point on the end of the punch into a center punch mark on
the piece.
With everything in proper order, the switch can be activated
to start the electric motor. The punch piston will move out
and push the punch through the material. Keep the switch
on until the punch has reached the end of its stroke and
stops. Release the switch. The automatic return valve will
open at the end of the stroke allowing the punch piston to
retract to its home position. The punch piston must return
completely before another hole can be punched.
If the punch stops in the midst of its stroke or does not
come out of the material, open the manual return valve.
Once the punch piston has returned to its home position,
tighten the manual return valve.
Although the foot switch is guarded against inadvertent
operation, it is best to position the foot pedal away from
normal standing position. Place it in a position that
requires deliberate effort to reach and activate the switch.
The trigger switch should be locked on only when ready
to punch. Release the trigger switch immediately after
punching to prevent operation by inadvertent actuation
of the foot switch.
INSTRUCTIONS -- FOOT SWITCH
WARNING! Failure to check punch retaining nut periodically during use, can result in
personal injury or damage to the unit could occur.
75006PR CONTENTS
Hydraulic Oil #32
75377
13/16" Diameter Punch
76366
13/16" Diameter
B Die (>1/8-1/4THK)
75605
Pin Spanner
76554
Foot Switch (115V)
75110
Foot Switch (230V)
76480
Foot Switch (230V, Type I)
76479
Work Stand
76552
M3 Hex Key
75742
M5 Hex Key
75744
M6 Hex Key
76556
M8 Hex Key
75746
Tommy Bar
76554
Strap
76555
Summary of Contents for 0756102
Page 6: ... 6 75006PR EXPLODED VIEW ...
Page 11: ... 11 NOTES ...