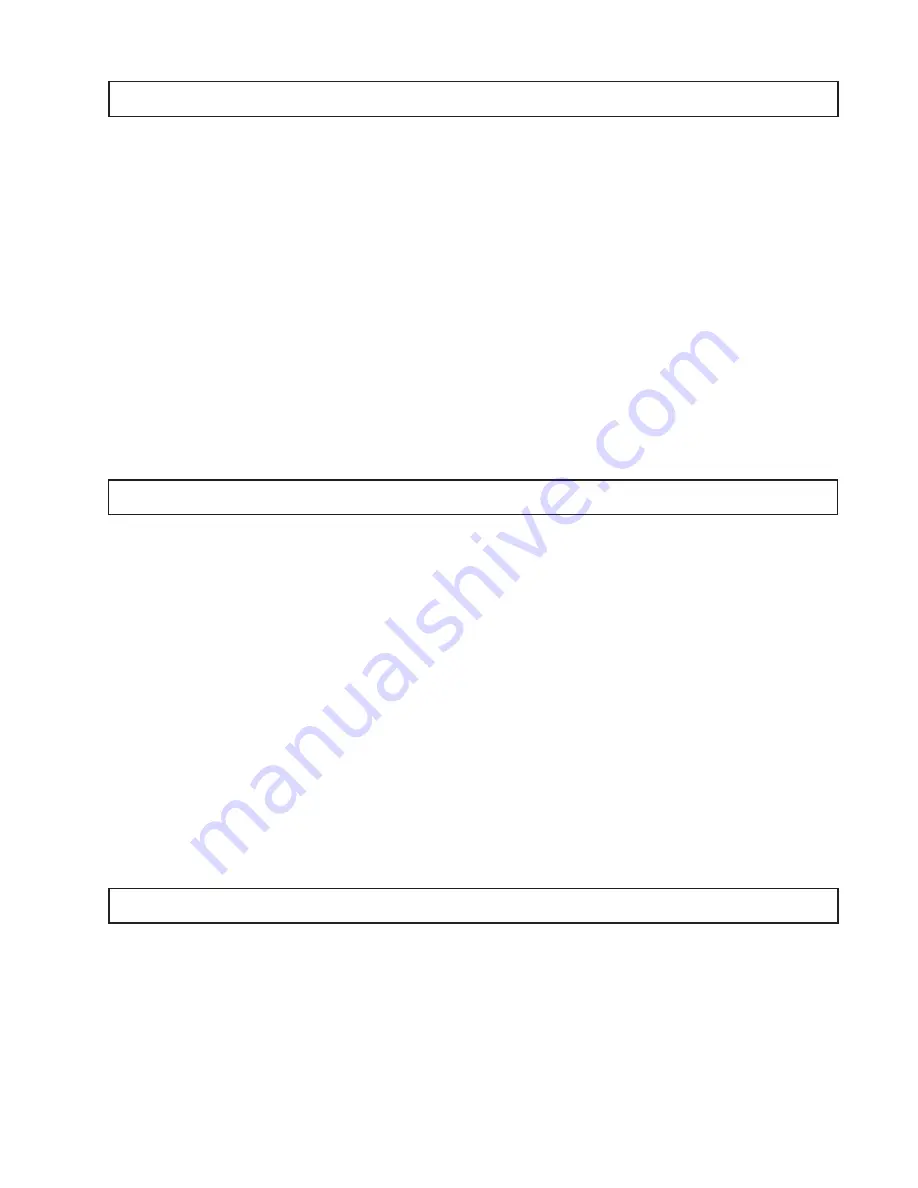
10
NOTE: The internal components of the pump and piston area have very close clearances and are sensitive
to damage from dust, dirt, contamination of the hydraulic fluid or improper handling. The disassembly of the
pump housing requires special tools and training, and should be attempted by a qualified repair person. The
improper servicing of electrical components can lead to conditions that could cause serious injury.
ANY ATTEMPT BY UNAUTHORIZED PERSONNEL TO SERVICE THE INTERNAL COMPONENTS OF
THE PUMP AREA WILL VOID THE WARRANTY.
In order to insure smoother operation and longer life of your
hole puncher, the following maintenance should be done
periodically, based on use.
1. Keep the machine clean. It is especially important to
keep the sliding portion of the punch piston free from metal
chips, scale, dirt, dust or other debris. To clean the punch
piston, turn on the switch to move the punch piston almost
to the bottom of its stroke. If necessary, cycle the punch
several times to determine where the bottom of the stroke
is, and to correctly position the punch piston.
Unplug the power cord. Wipe any debris from the ex-
posed part of the punch piston.
2. Regularly tighten all fasteners and replace any
worn components.
3. Check power cord, if cracked or frayed, return the
machine to an authorized repair center for
replacement.
4. Check oil level, carefully using the procedure below.
ADDING OIL
4. Carefully open the oil port by removing the socket
head cap screw.
5. Using the small squeeze bottle supplied with the
Hole Puncher, carefully add hydraulic oil to completely
fill the reservoir. Rock the Hole Puncher back and forth
slightly several times to free any trapped air bubbles,
then add additional oil if necessary.
6. Replace the cap screw and wipe up any excess oil.
7. Cycle the Hole Puncher several times with the
Manual return Valve open, and again with the valve
closed, to work any trapped air out of the system,
then repeat the above procedure, making sure that the
punch piston is almost at the bottom of the stroke
before removing the cap screw from the oil port.
8. Add additional oil as necessary. If the unit was
extremely low on oil, it may be necessary to repeat
the procedure several times.
MAINTENANCE
HELPFUL HINTS FOR HOLE PUNCHING
Each of the punches is provided with a sharp point at its
center. If the hole locations are center punched, the point
on the end of the punch may be used to "find" the center
punched spot.
Also, for accurate and easy positioning of the punch to a
hole location, the switch can be intermittently pulsed on
an off to jog the punch down to the work surface.
If the position is not satisfactory, open the manual return
valve to retract the punch for another attempt. This
operation can also be performed with the manual return
valve "cracked" open slightly to prevent full punching
pressure from being developed. In this manner, the
punch can be easily brought right down to the surface
without beginning to punch the hole. If the location is
satidfactory, close the valve and finish the operation.
Use of the correct hydraulic oil is essential. Approved oils
are Shell "TELLUS Oil" and Exxon "TERESSTIC" (Part
No. 75377). Grade #32 viscosity must be used. Check the
unit specifications. Make sure that the work area and all
equipment are clean so that no dirt, dust or other foreign
material can get into the hydraulic oil or pump area.
1. Locate the socket head cap screw that plugs the oil port.
It is just above the manual return lever on the right hand
side of the Hole Puncher.
2. Lay the Hole Puncher on its left side so that the oil port
is facing up.
3. Turn on the switch to move the punch piston almost
to the bottom of its stroke. If necessary, cycle the punch
several times to determine where the bottom of the stroke
is, and to correctly position the punch piston. In this posi-
tion, the maximum amount of oil has been drawn from the
pump and the correct fill can be obtained.
WARNING! Failure to check punch retaining nut periodically during use, can result in
personal injury or damage to your unit.
Summary of Contents for 0756102
Page 6: ... 6 75006PR EXPLODED VIEW ...
Page 11: ... 11 NOTES ...