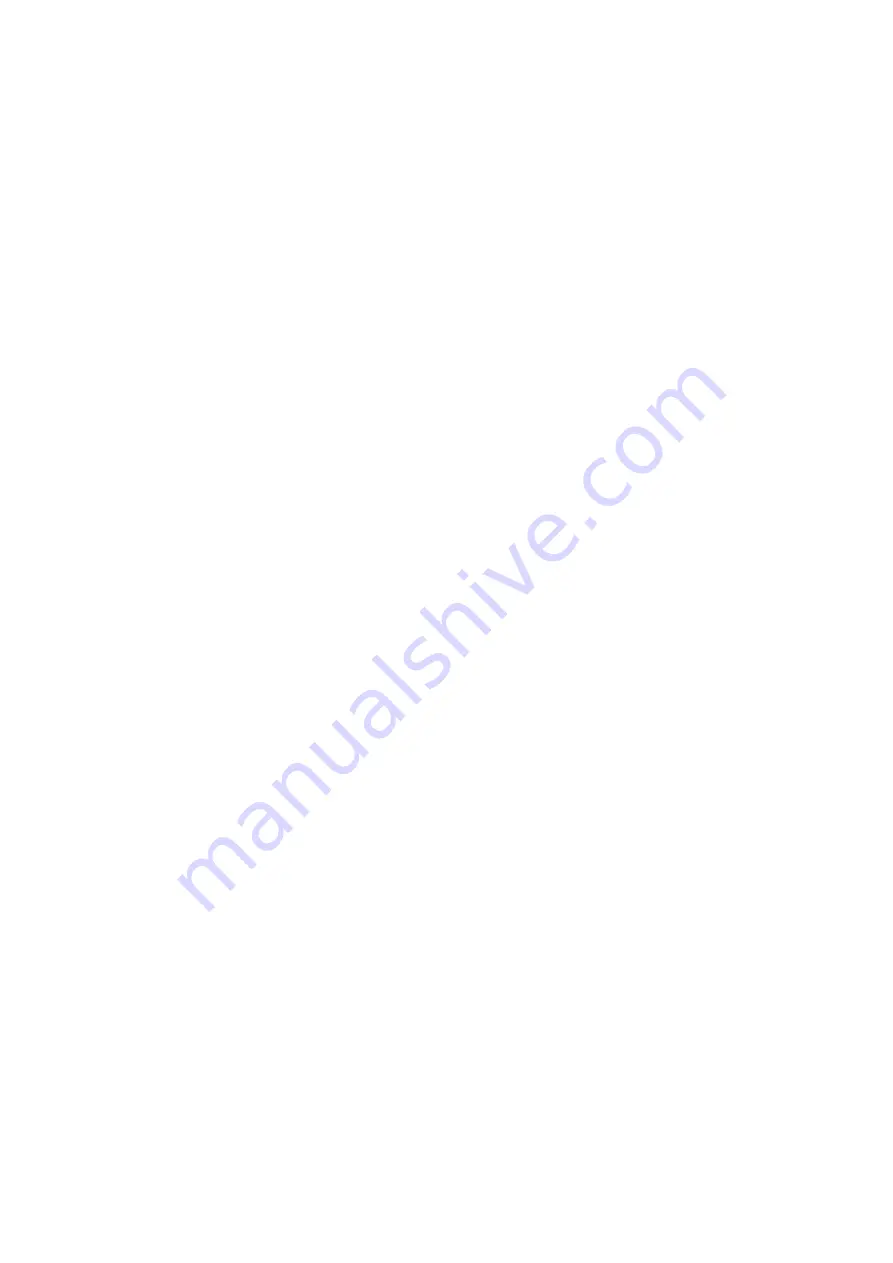
14
Commissioning must be carried out by
an OFTEC trained and registered engineer.
It is the responsibility of the installer to
ensure the boiler is properly commis-
sioned, failure to do so will make the
boiler’s guarantee and any extended
warranty null and void.
Although all burners are factory tested
before despatch, they will usually need
further air adjustment to achieve the
readings indicated in ‘Burner details’
because of site variations in flue draught
and back pressure.
Procedure
1. Switch off electrical supply to the
boiler.
2. Ensure boiler is full of water and all
valves are open.
3. Remove flue-cover and check that
flue-baffles are correctly positioned
4. Disconnect oil hose from burner,
open shut-off valve and run off a
8. SERVICING
7. COMMISSIONING
quantity of oil into a container to
check for a clean air free supply then
reconnect hose. (This applies to
single pipe gravity system only).
5. Check that the time-switch (if fitted)
is in the ON position and room and
boiler thermostats are calling for
heat.
6. Switch on electrical supply and the
burner should start.
Note:
The burner may lock-out on
first firing due to air in the pump. If
this happens, wait about a minute
before pressing reset button to
restart burner. If a further lock-out
occurs, the air should be bled from
the pump pressure gauge connection.
7. Start and stop the burner two or
three times until the flame cuts off
sharply - this indicates any
remaining air has been dispersed.
8. Allow the burner to run for about 15
minutes, then take a CO2 reading
through the sampling hole in flue-
cover. Compare the reading with
that given under ‘Burner Settings’
and adjust the air setting if necessary
to achieve the required CO2%.
Also, check the smoke and flue gas
temperature.
Handing Over
After completing the boiler installation,
the installer should make a thorough
check of the system to ensure it is com-
pletely satisfactory and demonstrate to
the user the operation of the boiler and
any system controls.
All instructions should be handed to the
user for retention and advice regarding
the need for annual servicing.
IMPORTANT: ISOLATE
ELECTRICAL SUPPLY TO THE
BOILER BEFORE SERVICING
To maintain the boiler’s high thermal
efficiency and reliable operation, it should
be serviced annually by an OFTEC trained
and registered engineer. Electrical work
should be carried out by a qualified
engineer.
If the boiler is used to provide central
heating and hot water all year round,
the best time for its annual service is
just before the start of the heating season.
Where the boiler is shut down for the
summer months, the service should be
carried out as soon as possible after the
end of the heating season.
Oil tank
Open tank drain-cock to draw off any
accumulated water and sludge.
Line filters
Turn off oil supply and remove filter
bowl. Wash filter element clean with
kerosene.
Servicing the Boiler
(Burner removed)
1. Remove the flue cover and lift out
the flue baffles (see diagram)
2. Brush all deposits from flue baffles
and internal surfaces of the boiler.
3. Remove flue deposits from the com
bustion chamber floor using vacuum
cleaner.
4. Replace flue baffles in correct
arrangement. Re-fit flue cover and
fully tighten wing-nuts to make a gas
tight seal.
5. Refit burner to boiler, connect
flexible air hose.
6. Turn on oil supply, switch on
electricity and burner should fire.
7. Finally check the combustion readings
with those given under ‘Burner
Settings’ and make any air or
pressure adjustments as necessary.
Burner Service Plate
A plate is supplied with this boiler for
supporting the burner during servicing.
The plate is to be bolted to the front
face of the boiler using the 2 studs pro-
vided. After servicing remove the plate
and store inside casing.
Summary of Contents for Contractor WM 70
Page 16: ...12 DE AERATOR OIL SUPPLY INSTALLATION TRIANCO CONTRACTOR WM BOILER...
Page 27: ......
Page 28: ......