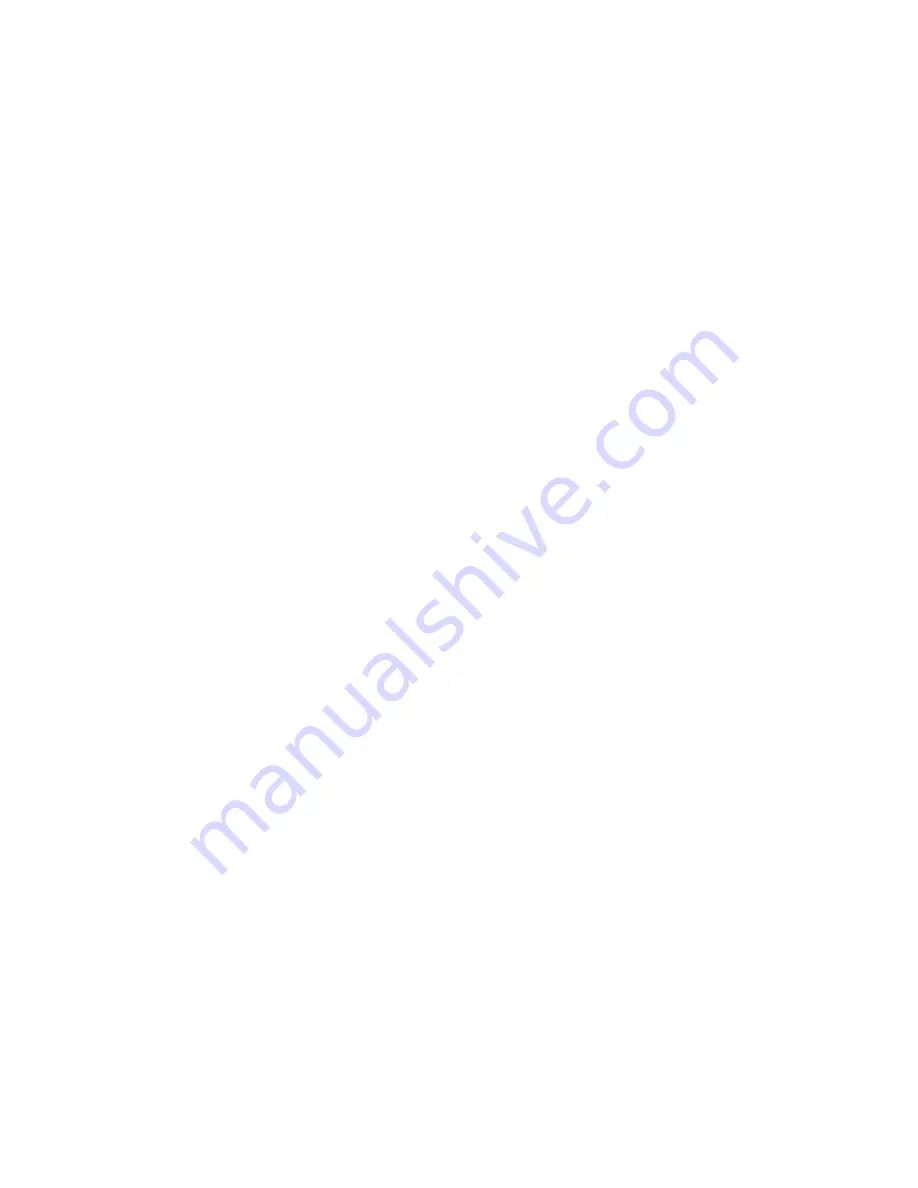
16
The tank should be fitted with the fill and vent connection
(weather protected), a drain-off cock, shut off valve and an
oil level indicator.
Plastic Tanks
Polyethylene tanks are now widely used because of their
advantages over traditional steel tanks:
a) They do not need pier supports and can be mounted
directly on any flat surface giving uniform support for
the tank base
b) They do not corrode and therefore never need painting.
c)
They are easier to handle because of their weight.
Plastic tanks should be fitted with similar components to
those used with steel tanks.
Fire Protection
To comply with building regulation
Section J5:
1
Where a storage tank is close to a dwelling, fire
cladding must be provided to the eaves, if less than
1.8m from the top of the tank.
2
The cladding must extend 300mm beyond the tank.
3
The tank must be sited on a non-combustible base.
Pollution Protection
To comply with building regulation
section J6
, the tank
must be ‘bunded’ (i.e. double walled) if:
1
The tank is less than 10m from a stream.
2
The tank is less than 50m from a well, spring, or drinking
water.
3
The tank cannot be viewed from the delivery point.
4
In the event of a leak, there is a risk of oil reaching a
manhole cover or drain.
5
The tank capacity exceeds 2500 Litres.
Oil Supply Line
A long life flexible oil hose is supplied with the boiler, a fil-
ter and shut-off valve are required.
The oil shut-off valve should be fitted as close to the burner
as practicable to enable the burner to be disconnected
without undue loss of oil. The filter must be connected in
the oil supply pipe and positioned outside the building.
Fire Valve
A fire-valve must be fitted in the oil line outside the building
with its sensing phial positioned within the boiler casing
below the control panel. A clip is provided for retaining the
phial.
All oil joints must be completely sealed and the total pipe
run thoroughly flushed out before connecting to the burner.
No soldered joints are permitted in the oil line.
The oil line can be fed into the back of the boiler base tray
or through the holes at the side.
Single pipe oil supply
(Fig 11)
When, the bottom of the oil supply tank is above the burner,
a single pipe gravity system can be used. The oil supply
pipe must be connected to the suction port on the burner
pump via the flexible hose.
Two pipe Oil Supply
(Fig 12)
Where, the bottom of the oil storage tank is below the
burner, a two-pipe suction lift system is necessary.
On the BFP II pump remove the end cover and filter, then
remove the ‘U’ washer by unscrewing the bottom screw,
then replace the screw ensuring it is fully inserted. An
additional flexible hose is also required.
A spring loaded non-return must be fitted in the suction line
to stop the oil running back to the tank. A filter, shut-off
valve and fire valve must be fitted in the line.
No valves are permitted in the return line which must
remain unobstructed at all times.
Notes:
(1) The pump suction should not exceed 0.4 bar, other
wise dissolved gas will be released form the oil to
affect combustion.
(2) The return pipe must end at the same level as the suction
outlet to prevent loss of prime.
(3) The outlet from the tank should be approximately
75mm (3 in) above the bottom to prevent sediment
and water being drawn into the supply pipe.
Oil De-aerator- Single Pipe Supply
(Fig. 13)
Where a two-pipe suction lift system is required , but the
return pipe is too long, or impractical to run., a de-aerator
can be used. The burner is piped as for a two-pipe system
up to the De-aerator but only a single pipe is required to be
run back to the oil storage tank. A non-return valve is not
required with this system but the bypass plug must be fitted
in the pump as for two pipe systems.
The Oil De-aerator should be fitted external to the building
close to the boiler but should not be fitted inside the boiler
casing.
Oil De-aerators are available from most Builders
Merchants and some Oil Tank manufacturers.
Summary of Contents for Combi 50 ECO
Page 10: ...7 Fig 2...
Page 14: ...11 Fig 4 EUROSTAR COMBI SCHEMATIC LAYOUT Fig 5 SEALED SYSTEM PIPING SCHEMATIC DIAGRAM...
Page 20: ...17 Fig 11 SINGLE PIPE OIL SUPPLY HEAD H METRES...
Page 21: ...18 Fig 12 TWO PIPE OIL SUPPLY...
Page 22: ...19 Fig 13 DE AERATED OIL SUPPLY INSTALLATION...
Page 32: ...29 Fig 20 2273 VERTICAL B F KIT 2273 Vertical Balanced Flue Kit 600mm 24 3000mm MAX 118...