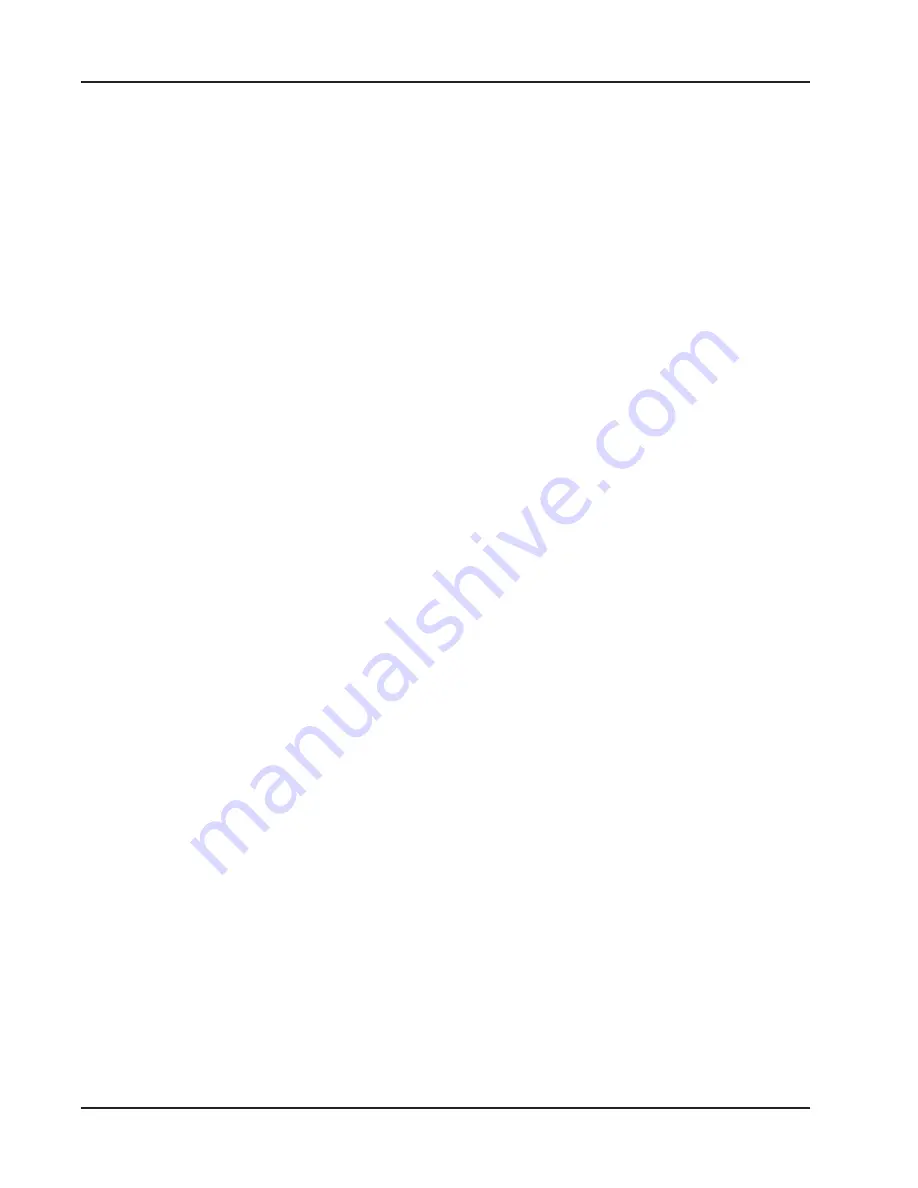
18
TRI TOOL INC.
92-0630 Rev. 190612
1. Adjust the cutting RPM with the Speed Control to just above the required
cutting speed as the Tool Bit enters the cut.
2. The Tool will slow down slightly as the cutting load increases, apply additional
power to hold the cutting speed.
3. Observe the chip as the machine is cutting.
•
The ideal chip will come off in a loose pig tail spiral.
•
A chip that is coming off in a tight straight spiral normally indicates that the
feed is too heavy.
•
A straight or slightly curled chip normally indicates that the feed is too light.
4. Back off the feed as required to break the chips and let them fall away.
5.
If a significant amount of stock must be removed, occasionally back out of the
cut and let the Tool Bit spin free in the air to cool.
6. Continue rotating the Feed Handle clockwise until the end of the pipe is
completely machined. Do not to let the Tool Bit cut into the Collet or the Collet
Adapter.
7. Discontinue feed and allow the Cutting Head to rotate one time for stainless
steel and up to three times for other materials to improve the finish of the prep
surface. Never let a Tool Bit 'rub’ the surface of a stainless steel tube without
cutting. This will work harden the material and it will be difficult for the Tool
Bit to get under the material in order to finish the cut. This will also cause
excessive Tool Bit wear.
8. Rotate the Feed Handle counter-clockwise to separate the Cutting Head and
the pipe.
9. Stop the Cutting Head rotation.
10. Release the Trigger.
11. Rotate the Feed Knob counter-clockwise until the Cutting Head clears the
tube or pipe by at least 1/8” (3.2 mm) or more.
12. On the Model 301 loosen the Collet Nut to release the tube or pipe.
13. On the Model 301QL pull the Toggle Clamp Lever back to release the tube or
pipe.
14. If the next cut is to be identical to the previous cut, then follow the sequence
starting with section 6.3, Install a Collet in the Model 301 or section 6.4 Install
a Collet in the Model 301L
15. If the next cut is to be different than the previous cut, disconnect the power
cord and then follow the sequence starting with section 6.1, Select a Tool Bit.
16. End squaring of 1/8” (3.2 mm) diameter or smaller tubing with the Model 301.
End squaring of small tubing with the Model 301 can be difficult due to the
cutting force causes the tube to flex. Another problem is that it is difficult to
Summary of Contents for 301A
Page 1: ...92 0630 Rev 190612 Model 301 Tube Squaring Machine ...
Page 42: ......