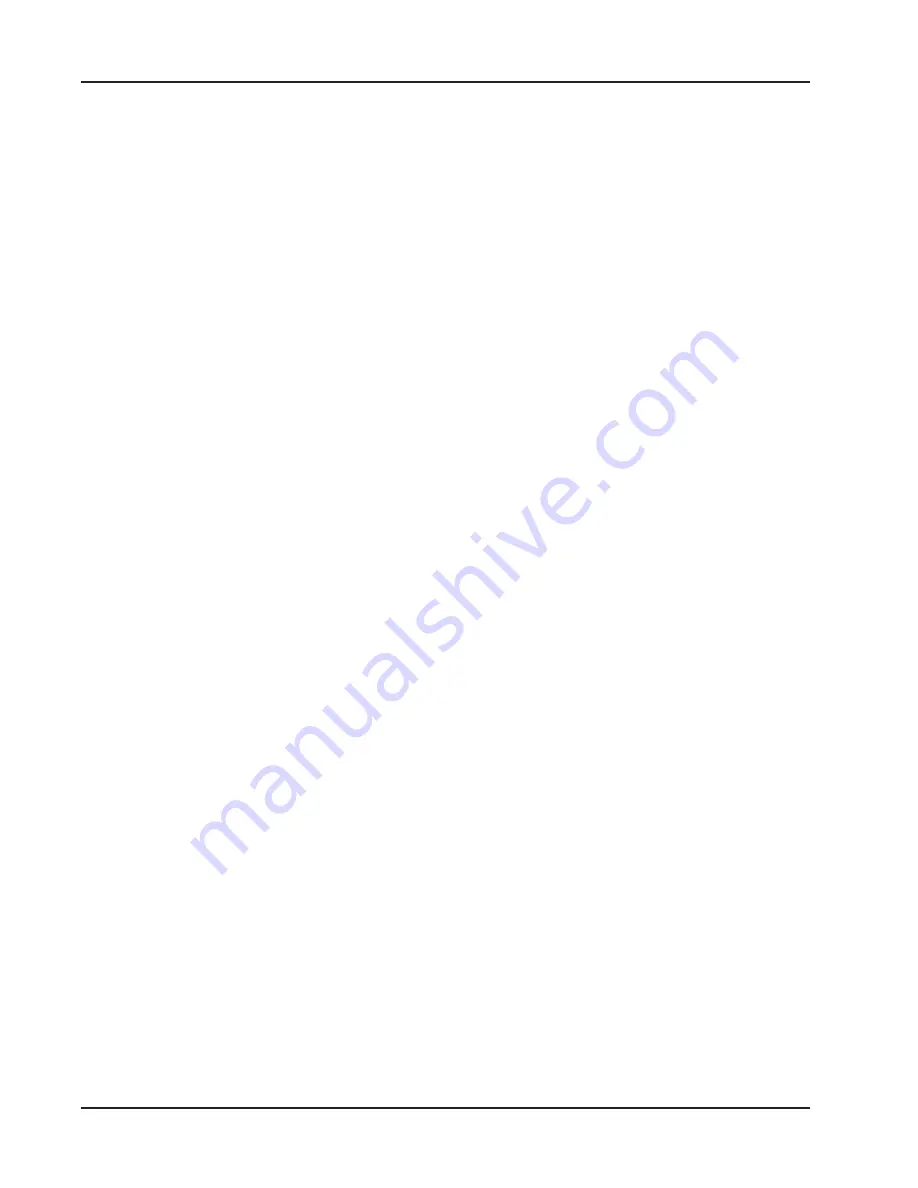
12
TRI TOOL INC.
92-0630 Rev. 190612
Use the M-42 Tool Bits with the exotic alloys if high heat resistance is required to
avoid burning the cutting edge of the Tool Bit.
•
M-42 can improve the life expectancy of the Tool Bit under some conditions
on stainless steel.
•
M-42 Tool Bits are more brittle than the M-2 Tool Bits, therefore there is a
much greater risk of damaging the M-42 Tool Bit when installing the tubing in
the Tube Squaring Machine.
Loss of Tool Bits from damaged edges may not off-set the improved cutting life
that those Tool Bits promise.
Some exotic alloys may require Tool Bits with both the extra hook angle as well
as the M-42 tool steel for heat resistance.
6.2 INSTALL A TOOL BIT
1. Ensure that the Model 301 is disconnected from the power source before
installing a Tool Bit.
2. Insert the Tool Bit into the slot in the Cutting Head. Refer to Fig. 4. This
position is used for .50” (12.7 mm) and smaller diameter tubing. This is the
designed working position of the Tool Bit and will leave virtually no burr with
standard tubing.
•
When working with electro-polished stainless steel tubing, use slow cutting
speeds to minimize the ID burr.
•
The Tool Bit (P/N 99-1445) may be reversed. Refer to Fig. 4. Use the
reversed position for tubing with an ID greater than .50" (12.7mm).
•
With the extreme shear cutting action, the burr on the ID will be virtually
eliminated.
•
Minimum burr may be obtained with a slow RPM and a slow feed, which will
cut a continuous chip.
•
Terminate the cut with one or two revolutions without feed to square the end
of the tubing.
•
The cutting edge of the Tool Bit must be located on the radial centerline.
3. Tighten the Set Screws to secure the Tool bit to the Cutting Head. Refer to
Fig. 5.
Summary of Contents for 301A
Page 1: ...92 0630 Rev 190612 Model 301 Tube Squaring Machine ...
Page 42: ......