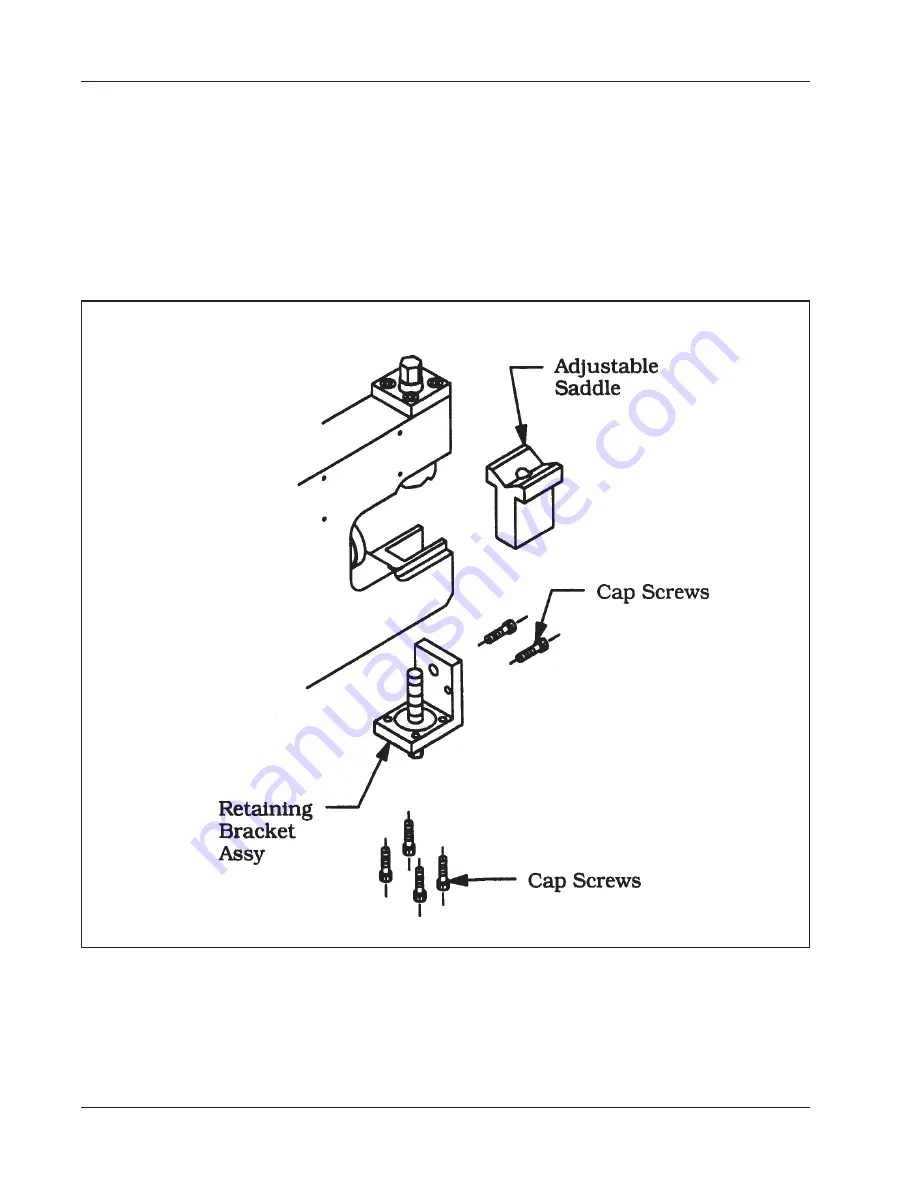
16
TRI TOOL INC.
92-0631 : Orig. 960119
If the next bevel is to be different than the previous bevel, then follow the sequence
starting with “Adjusting the Adjustable Saddle Kit….”
Converting the Adjustable Saddle to the Fixed Saddle.
Remove the (4) four Cap Screws from the bottom of the Retaining Bracket Assy and
(2) two Cap Screws from the front.
Removal of the Adjustable Saddle from the Model 201BA
Remove the Retaining Bracket Assy from the front of the Model 201BA.
Insert the Fixed Saddle Adapter into the front of the Model 201BA.
Attach the Fixed Saddle Adapter by using (4) four Cap Screws from the bottom and
(2) two Cap Screws from the front.