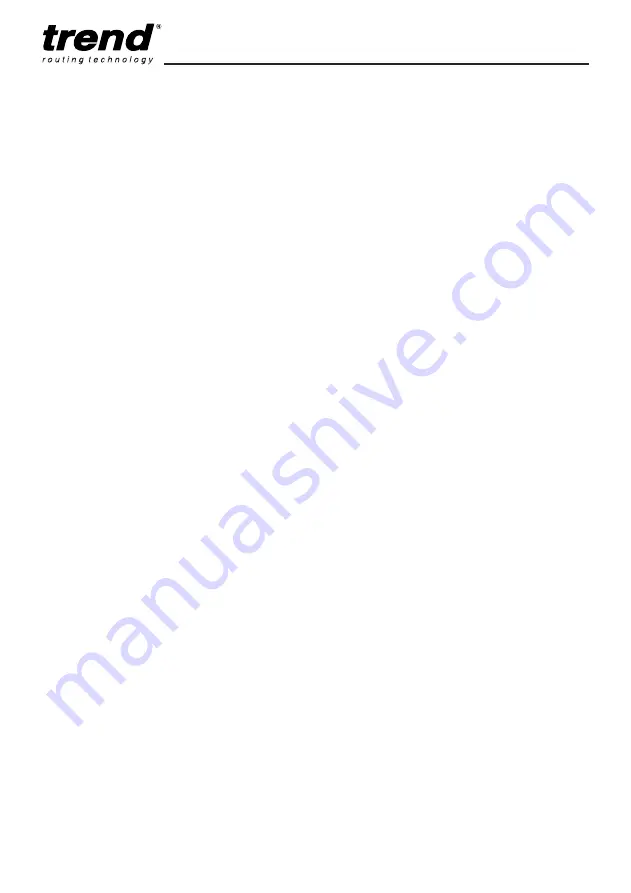
LOCK/JIG/A
-3-
7.
Do not switch router on with the
cutter touching the workpiece. At the
end of the cut, release the router
plunge and allow spindle to stop
rotating. Never use the spindle lock
as a brake
8.
The direction of routing must always
be opposite to the cutter’s direction
of rotation. Do not back-cut or climb-
cut.
9.
Check before cutting that there
are no obstructions in the path of
the router. Ensure there are no
obstacles beneath workpiece when
cutting full thickness, and that a
sacrificial work surface is used.
Router Cutter Safety
1.
Cutting tools are sharp. Care should
be taken when handling them. Do not
drop cutters or knock them against
hard objects. Handle very small
diameter cutters with extra care.
Always return cutter to its packaging
after use.
2.
Always use cutters with a shank
diameter corresponding to the size of
the collet installed in your tool.
3.
The maximum speed (n.max) marked
on the tool, or in instructions or on
packaging shall not be exceeded.
Where stated the speed range shall
be adhered to. Recommended
speeds are shown in the Trend
Routing Catalogue and/or website.
4.
Always use router cutters in a router.
Drill and boring bits must not be
used in a router. Router cutters
must only be used for the material
cutting application for which they are
designed. Do not use on metal or
masonry.
5.
Never use cutters with a diameter
exceeding the maximum diameter
indicated in the technical data of the
powertool or attachment used.
6.
Before each use check that the
cutting tool is sharp and free from
damage. Do not use the cutting tool
if it is dull, broken or cracked or if in
any other damage is noticeable or
suspected.
7.
Cutters should be kept clean. Resin
build up should be removed at
regular intervals with Resin Cleaner.
The use of a PTFE dry lubricant will
reduce resin build up. Do not use
PTFE spray on plastic parts.
8.
When using stacked tooling (multi-
blade, block and groover etc.) on a
spindle arbor, ensure that the cutting
edges are staggered to each other to
reduce the cutting impact.
9.
Cutter shanks should be inserted
into the collet all the way to the line
indicated on the shank. This ensures
that at least
3
⁄
4
of the shank length
is held in the collet. Ensure clamping
surfaces are cleaned to remove dirt,
grease, oil and water.
10.
Observe the correct assembly and
fitting instructions in the router
instruction manual for fitting the
collet, nut and cutter.
11.
Tool and tool bodies shall be
clamped in such a way that they will
not become loose during operation.
Care shall be taken when mounting
cutting tools to ensure that the
clamping is by the shank of the
cutting tool and that the cutting
edges are not in contact with each
other or with the clamping elements.
12.
It is advisable to periodically check
the collet and collet nut. A damaged,
worn or distorted collet and nut can
cause vibration and shank damage.
Do not over-tighten the collet nut
13.
Do not take deep cuts in one pass;
take several shallow or light passes
to reduce the side load applied to the
cutter and router. Too deep a cut in
one pass can stall the router.
14.
In case of excessive vibrations whilst
using the router stop immediately
and have the eccentricity of the
router, router cutter and clamping
system checked by competent
personnel
15.
All fastening screws and nuts should
be tightened using the appropriate
spanner or key and to the torque
value provided by the manufacturer.
16.
Extension of the spanner or
tightening using hammer blows shall
not be permitted.
17.
Clamping screws shall be tightened
according to instructions provided by
the manufacture. Where instructions
are not provided, clamping screws
shall be tightened in sequence from
the centre outwards.
Using Routers In A Fixed Position
1.
Attention should be made to the
HSE’s Safe Use of Vertical Spindle
Moulding Machines Information
Sheet No.18 and any revisions.
2.
After work, release the router plunge
to protect the cutter.
3.
Always use a push-stick or push-
block when making any cut less than
300mm in length or when feeding the
last 300mm of the cut.
4.
The opening around the cutter
should be reduced to a minimum
using suitably sized insert rings in
the table and closing the back fence
cheeks or fitting a false fence on the
back fence.
5.
Whenever possible use a work
holding device or jig to secure
component being machined. Ensure
any attachment is securely fitted to
the workbench, with table surface at
approximately hip height.
6.
Use a No-Volt Release Switch.
Ensure it is fixed securely, easily
accessible and used correctly.
7.
In router table (inverted) mode, stand
to the front right of the table. The
cutter will rotate anti-clockwise when
viewed from top so the feed direction
is from the right (against the rotation
of the cutter). In overhead mode,
stand to the front left of the machine
table and the feed direction is from
the left.
8.
Do not reach underneath table or
put your hands or fingers at any
time in the cutting path while tool is
connected to a power supply.
9.
Never thickness timber between the
back of the cutter and the backfence.
Useful Advice When Routing
1.
Judge your feed rate by the sound
of the motor. Feed the router at a
constant feed rate. Too slow a feed
rate will result in burning.
2.
Trial cuts should be made on waste
material before starting any project.
3.
When using some attachments e.g.
a router table or dovetail jig, a fine
height adjuster is recommended.
4.
When using a template guide bush,
ensure there is sufficient clearance
between cutter tip and inside edge
of bush and that it cannot come into
contact with collet and nut. Ensure
cutter and guide bush are concentric.
Router Cutter Repair/Maintenance
1.
Repair of tools is only allowed in
accordance with the manufacturers
instructions.
2.
The design of composite (tipped)
tools shall not be changed in process
of repair. Composite tools shall be
repaired by a competent person i.e.
a person of training and experience,
who has knowledge of the design
requirements and understands the
levels of safety to be achieved.
3.
Repair shall therefore include, e.g.
the use of spare parts which are in
accordance with the specification
of the original parts provided by the
manufacturer.
4.
Tolerances which ensure correct
clamping shall be maintained.
5.
Care shall be taken that regrinding
of the cutting edge will not cause
weakening of the body and the
connection of the cutting edge to the
body.
Version 7.2 06/2013