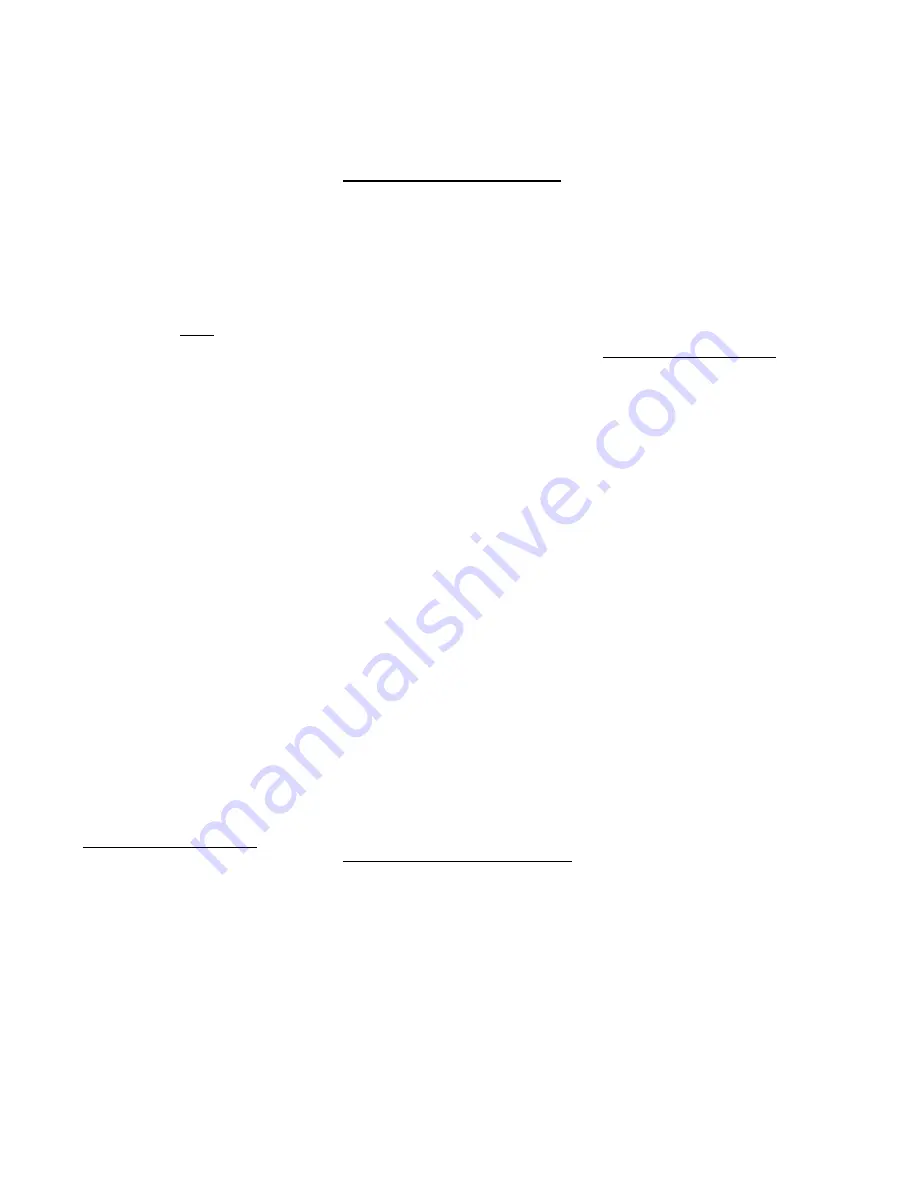
Insert the rotor Blades, angled edge
first into each groove with a coating of
oil to keep them in place (do not use
grease).
Place the Cylinder (18) centrally over
the Rotor assembly locating the
shorter spring pin in its location hole in
the Front End Plate (19).
With the oil grooves of the Rear Plate
(14) assembly facing downwards,
place onto the threaded end of the
Rotor and using the second Ø15mm
tube on the centre race of the bearing.
Ensure that the long spring pin (17) is
aligned with its location hole in the
Rear Plate and lightly press down until
there is no visible gap between the
Cylinder and Rear Plate.
Check that assembly rotates smoothly.
If stripped reassemble the Governor,
Insert the threaded end of the Plunger
(12) into the Governor (slotted side).
Fit the Spring (45) and the Adjust Nut
(42).
Holding the Plunger tighten the
Adjuster Nut until the end of the nut to
face of the Governor measures 6mm,
which will give a safe starting point.
Attach the three Pendulums to either
side of the Governor, retain using the
two spring pins (48), tap in with small
hammer.
Screw the Governor assembly onto the
threaded end of the motor assembly,
this is a left hand thread.
Place the splined end of the motor
assembly into a soft jawed vice and
using a 13mm spanner on the spanner
flats, nip up the Governor.
Assembling the Spindle
Using the Ø21.5 tube as a base, place
the new bearing (32) centrally over the
tube. Insert the Spindle (33) threaded
end uppermost and press the spindle
onto the bearing until solid.
Place the Spacer (35) on the Bearing
and insert the Woodruff Key (34) into its
keyway and slide the Bevelled Gear
(30) onto the Spindle (33) with the teeth
facing away from the bearing.
Place the Wavy Washer (31) on the
Spindle followed by the Circlip (29),
pressing it down on it against the Wavy
Washer (31) to ensure that it is secure
in its groove.
Support the Spindle (33) under the
boss, threaded end down, use the
21.5mm tube as a base, and using the
Ø10mm tube over the Bearing (28)
press onto the Spindle until solid.
Assembling the Gear Housing
Place Spacer (81) into the Felt Oiler
(79), note that the hole is offset in the
oiler, the short side sits at the bottom of
the Gear Head.
Insert the Steady (80) into the Felt Oiler
Spacer (81) and position the
assembly’s hole directly over the hole
for the retaining Screw (27).
Insert retaining Screw (27) with it’s
O’Ring (7) but before tightening fully,
ensure that the Felt Oiler is fully seated,
then tighten.
Insert the Spacer (26) into it’s recess at
the bottom of the Gear Housing with the
domed side first.
Place several drops of gear oil onto
the Felt Oiler (79).
Also grease the Bevel Gear (30) with a
molybdenum or lithium based general
purpose grease and insert the Spindle
assembly into the Gear Housing (23).
Insert the Spindle Lock Button
assembly with the flat adjacent to the
retaining grub Screw threaded hole.
Insert the grub Screw (61) and tighten
the grub Screw using a 2.5mm Allen
key.
Fit the Bearing Cap (36) over the
spindle with the Spring’s (68) location
hole nearest the Spindle Lock Button
location hole.
Fit the 4 x M5 caphead Screws (43)
and tighten using a 4mm Allen key.
Assembling the Motor Housing
Insert the throttle Pin (5) into the Motor
Housing (1).
Locate the Throttle Lever assembly (4)
into position and secure with the Spring
Pin (2).
Using the Ø11.8mm bar push in the
Valve Seat (6) through the threaded
brass insert until seated.
When in the correct position the Valve
seat should be 25mm down the bore.
Insert the Valve Stem (10) long stem
first into the threaded brass insert,
followed by the Spring, small end first.
Fit the O’Ring (66) onto the Exhaust
Deflector (53) and push into the end of
the Motor Housing (1).
Carefully apply a small drop of
Loctite 243 to the thread of the
Air Inlet (3) only.
Do not allow Loctite onto the Spring
face of the Air Inlet (3) as this could
cause the motor to seize if it
contaminates internal components.
Fit the Air Inlet (3) into the Exhaust
Deflector (53) and tighten using a
21mm spanner.
Assembling the Grinder
Place the Inlet Guide (44) onto the
Governor end of the motor locating the
spring pin (17) into its slot in the Inlet
Guide.
Hold the assembly vertically by the
splines with the Inlet Guide (44) at the
top and carefully slide into the Motor
Housing (1).
The large diameter of the Front End
Plate (19) should now be almost level
with the Motor Housing face.
Put a smear of grease on the gasket
face to hold it in position and place the
gasket (21) onto the Motor
Housing (1).
Fit the Gear Housing (23) onto the
Motor Housing (1) by inserting the
splined shaft into the centre of the
bearing, you may have the turn the
spindle (33) to engage the splines into
the Bevel Gear (30).
Line up with the Screw holes and
insert the 4 x M5 Screws (25) with their
Spring Washers (24). Using a 4mm
Allen key, tighten all equally.
With the spindle facing upwards, insert
the spring (68) onto its recess.
Place the Lock Ring (69) into its
location, with the three recessed holes
on the tab facing towards the Bearing
Cap (36), followed by the Disc Cover
(37), and the Disc Spring (70).
Fit the Circlip (71) using circlip pliers,
ensuring its locates into the location
groove.
Check the spindle RPM and if
necessary strip down and adjust the
governor until 10,000rpm ±100rpm is
achieved.
Summary of Contents for 735.7072
Page 1: ...4 Vibration Reduced Angle Grinder Operation and Maintenance Manual www trelawnyspt co uk ...
Page 2: ......
Page 3: ......
Page 11: ...NOTES ...
Page 12: ...NOTES ...
Page 13: ...NOTES ...