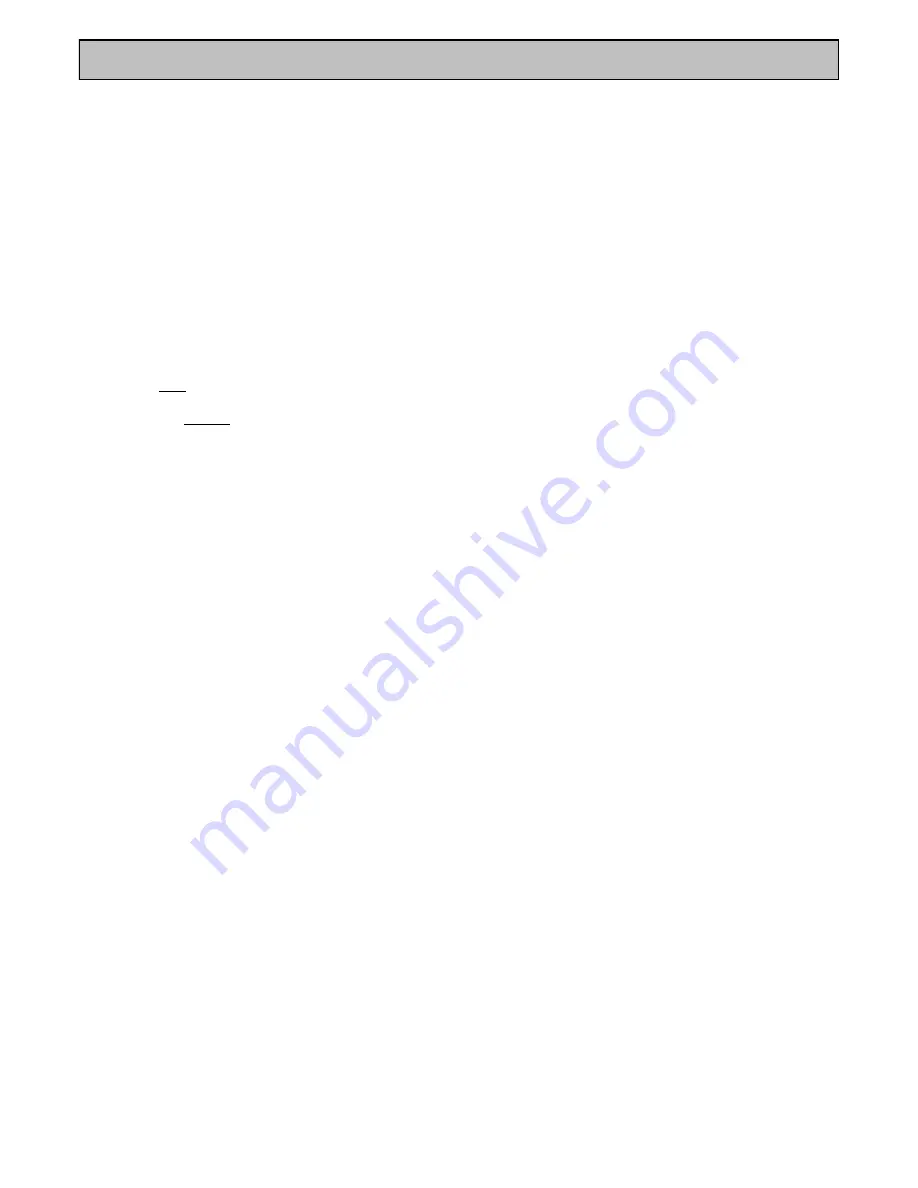
OPERATION & MAINTENANCE
While changing
the
drum
the
condition of the drive shaft and side
plate bearings should be checked.
If any roughness, side play or
leakage of grease is detected then
new bearings should be fitted.
Lightly oil the drive shaft to prevent
a build up of rust which could cause
difficulty when trying to removing the
drum later.
At the same time check belt tension
and condition also checking the
pulley grooves are clean and
undamaged.
The drive shaft is manufactured from
high quality steel to produce the
special properties required.
The shaft is extremely strong and
virtually unbreakable when used as
intended.
If however sideways pressure is
exerted on the shaft while it is not
supported by the side plate bearing it
can be bent.
With the drum removed check that
the vacuum port is free from
blockages and that the dust skirts
are in good condition.
Remove all build up and deposits of
material from the under side of the
drum housing.
On certain applications, e.g. the
removal of damp self levelling
compounds, it may be necessary to
clean away deposits hourly!
Failure to do so could result in
overload of the drum assembly, drive
motor and drive belts.
Machine Operation
continued:
Do not
pull the control levers into
reverse when cutting as this could
result in the machine reversing
quickly in an uncontrolled manner.
The machine should operate
smoothly with a minimum of
vibration.
When the depth of cut is correctly
set very little effort should be
required to operate the machine.
EXCESSIVE downward pressure on
the cutters may marginally improve
the work rate/finish but the negative
result will be a definite increase the
wear rates on the cutter drum
assembly and machine components.
Remember two light passes are
quicker and more cost effective than
one slow pass with a heavy cut.
Tests have proven conclusively that
heavy downward pressure reduces
cutter and drum life by over 50%.
The TFP320 should always be
operated in a forward direction.
The operator varies the speed of
travel to determine the final finish
having already pre-set the depth
control.
It is recommended that you do not
operate the machine in reverse
whilst the cutters are in contact with
the surface.
When lifting the cutter drum from the
work surface it is not necessary to
turn the hand wheel - raise the
cutters by simply operating the
hydraulic lift lever.
N e v e r
l e a v e
t h e
T F P 3 2 0
unattended while in use
.
Always stop the motor and raise the
height adjustment fully up before
leaving the machine and disconnect
all power leads.
MAINTENANCE
PRIOR TO ANY MAINTENANCE
OR ADJUSTMENT SWITCH OFF
THE POWER SUPPLY AT THE
MACHINES CONTROL BOX AND
DISCONNECT FROM THE MAINS.
After use:
Clean the machine to remove all
build up of dust and surface
residues.
If using a hose pipe or pressure
washer take care that water is not
directed onto electrical components
and switches.
Note:
Motors and switches are not
waterproof
Drum Removal:
Remove bolts on side plate and then
screw two bolts back into the two
tapped holes in the side plate.
Continue winding in and this will
push side plate off dowel pins.
Remove the side plate and the key
from shaft. Pull out cutting drum.
Fitting a new cutter head is simply a
reversal of the above procedure, a
little care must be taken to align the
drive shaft, cutter drum and support
end drive bush.
EXCESSIVE FORCE SHOULD NOT
BE NEEDED TO REFIT THE
CUTTER DRUM.
Cutter Drum Maintenance:
When changing cutter drum always
check that the flail shafts are not
worn with pronounced grooves and
also that the centres of cutters and
spacers are not elongated and
beginning to "mushroom".
The
drum
assembly
is
hitting
concrete with great force 3900 times
every minute! Expenditure on
consumables must be expected and
built into all job costing.