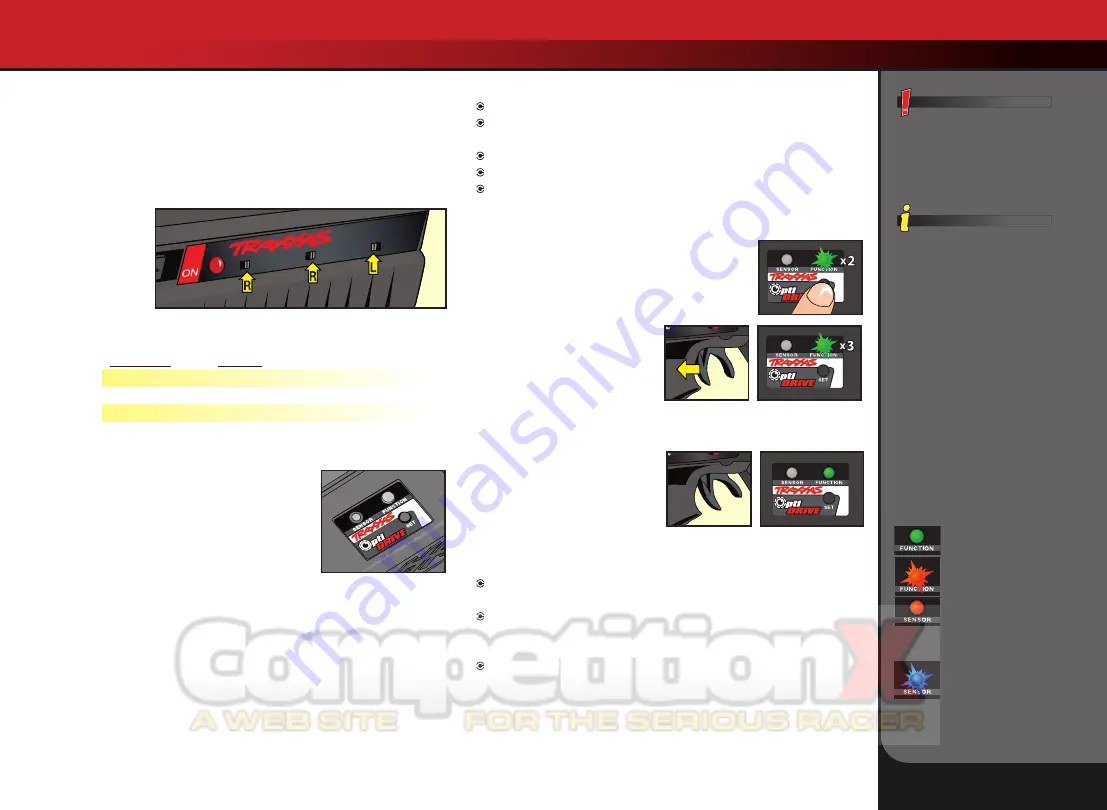
Revo • 15
Servo Reversing Switches
The servo reversing switches are located on the front of the transmitter,
next to the on/off switch. Moving a switch reverses the direction of the
corresponding servo. Each switch corresponds to a channel, as shown
below. For example, if you turn the steering wheel to the right and your
front wheels turn left, you would move the channel 1 switch to correct
the servo direction. It may be necessary to adjust the corresponding trim
control after
moving a switch
.
The default
position for the
servo reversing
switches is
shown.
Programming the OptiDrive
™
ESM
The OptiDrive ESM electronically monitors
vehicle speed and controls forward and reverse
shifting. Controlling the shift action electronically
rather than by mechanical systems reduces the
number of components in the transmission. The
transmission weighs less, there is lower
rotational mass for quicker acceleration, and
constant drive engagement for smooth power delivery.
The OptiDrive module prevents the transmission from changing
directions while the truck is in motion. The truck must be completely
stopped to change directions, regardless of the position of the shift
selector switch on the transmitter. The OptiDrive module is preset at the
factory. If the transmitter throttle trim adjustment is changed, then the
OptiDrive module will need to be re-programmed.
1.
The engine must be shut off. The radio system must be on (receiver
and transmitter).
2.
Set the TQ-3 Transmitter to its factory default shift settings:
Set the THROTTLE NEUTRAL switch to the 50/50 setting.
Set the THROTTLE TRIM to the center “0” setting, then adjust the
THROTTLE TRIM until the carburetor closes.
Set the CHANNEL 2 SERVO REVERSING SWITCH to the right position.
Set the CHANNEL 3 SERVO REVERSING SWITCH to the right position.
DO NOT change the position of any of the servo reversing switches
after programming the OptiDrive. If settings were changed after
programming the OptiDrive, it will have to be reprogrammed.
3.
With the throttle at neutral, press and hold the
SET button until the Function LED flashes green
twice and then release the button immediately.
You are now in programming mode.
4.
Pull the transmitter throttle
trigger to the full throttle
position. Hold it there until the
Function LED flashes green
three times.
Note:
The throttle
servo will not move during programming even though it is connected
to the controller.
5.
Release the transmitter throttle
trigger allowing it to return to
neutral. The Function LED will
turn solid green, indicating that
the shifting servo is OK to shift
and the programming has been completed. The controller is now
programmed and ready to go!
If the transmitter throttle settings are changed, it will be necessary
to complete the programming sequence again.
If the SET button is released before the Function LED flashes
green twice in step 3, the OptiDrive will return to the normal
operation mode.
If you experience any problems during programming, turn the
receiver off, then on again, and repeat the programming steps.
For instructions on how to use the OptiDrive with aftermarket radio
systems, or to access advanced programming options, visit our website,
www.Traxxas.com.
CH.3
CH.2
CH.1
Channel
Servo
1
Steering
2
Throttle and braking
3
Shifting
The Traxxas TQ-3 Radio System
Large adjustments to the
throttle trim and/or throttle
linkage may require
re-setting the OptiDrive
ESM to maintain proper
shifting action.
TQ-3 Channel to Servo Chart
For transmission durability,
the OptiDrive ESM limits
the model’s reverse speed
to about 70% of full
throttle. If settings are
changed, and you notice a
decrease in forward top
speed, you could have the
OptiDrive system reversed.
Return the TQ-3 servo-
reversing switches for
channels two and three
back to their default
settings and re-program the
OptiDrive Module. For
programming with
aftermarket radio systems,
please see our website.
•
Green
“
Function
”
Shift allowed
•
Red flashing
“
Function
”
Low battery, see pg. 12
•
Red
“
Sensor
”
Sensor circuit is broken.
Possible disconnected
sensor, broken wires, or
damaged sensor.
•
Blue flashing
“
Sensor
“
Normal operation as
vehicle moves. Indicates
signal pulse from sensor.
Depending on the rotor
position, solid blue or off
when vehicle is at rest.
OptiDrive Operation