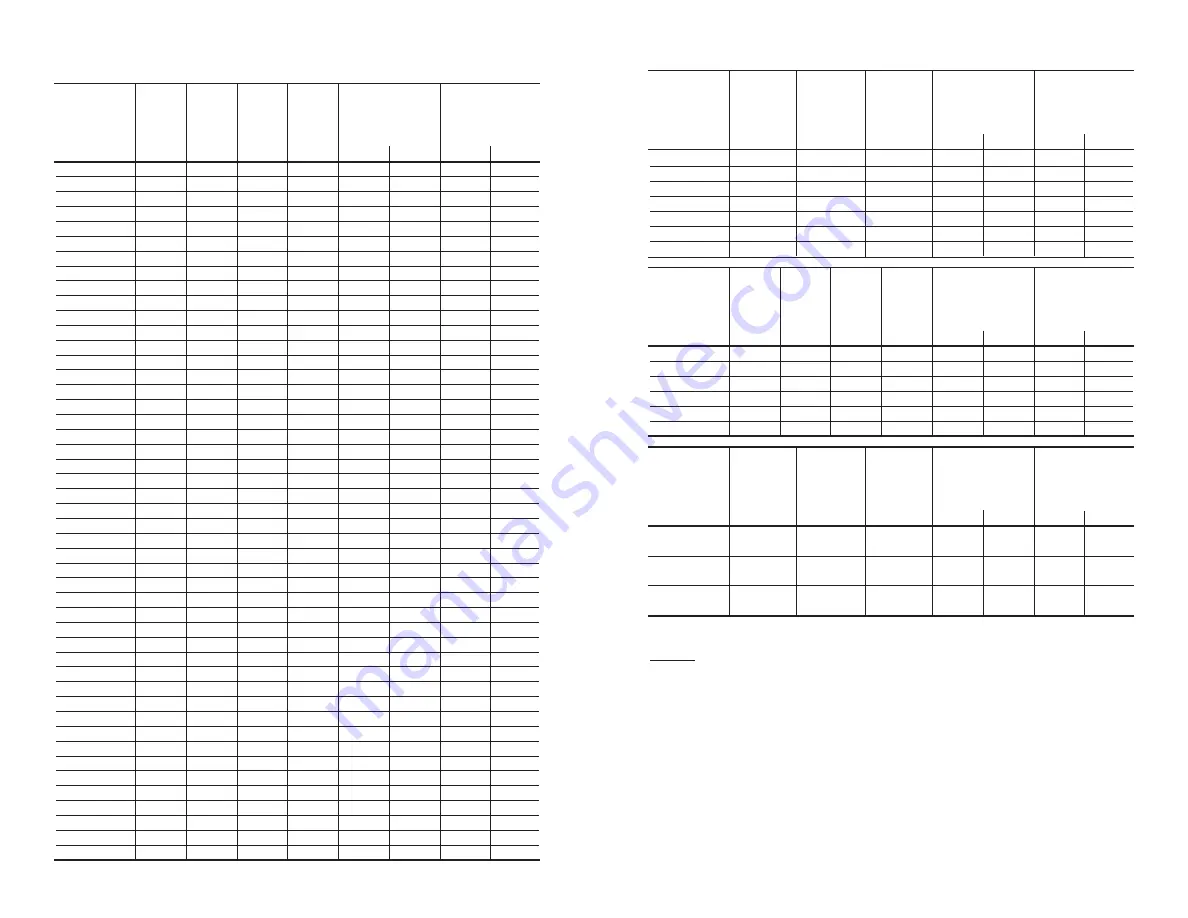
Table 8 (continued)
dB(A)
lbs.
lbs.
50 Hz
60 Hz
50 Hz
60 Hz
TRMA 32-25
69
37
40
2900
3500
0.75
1.1
TRMB 32-50
69
53
57
2900
3500
1.5
2.2
TRMB 32-75
70
81
91
2900
3500
3
4
TRMB 40-110
68
145
156
1450
1750
3
4
TRMB 40-150
69
167
233
1450
1750
4
5.5
TRMB 40-200
72
227
244
1450
1750
5.5
7.5
TRMB 50-300
72
277
—-
1450
—-
7.5
—-
dB(A)
lbs.
lbs.
lbs.
50 Hz
60 Hz
50 Hz
60 Hz
TRVB 40-110
68
—-
136
—-
1450
1750
3
4
TRVB 40-150
69
—-
141
—-
1450
1750
4
5.5
TRVB 40-200
72
—-
172
—-
1450
1750
5.5
7.5
TRVB 50-300
72
—-
194
—-
1450
1750
7.5
10
TRVA 65-300
70
293
341
354
1450
1750
7.5
10
TRVA 65-450
70
321
387
442
1450
1750
11
15
dB(A)
lbs.
lbs.
50 Hz
60 Hz
50 Hz
60 Hz
SA0E3U
67
123
242
2900
3500
11
15
15
20
SA0G2D
69
183
297
2900
3500
11
18,5
15
25
SA0G2G
69
191
139
2900
3500
15
20
157
22
30
NOTES:
• Noise level (measured at 3 feet distance, without motor, with pump installed in
the system) for pump series TRH, TRM, TRV when operating at 60 Torr and
pump series TRS when operating at 175 Torr. Noise level test to ISO 3746
standards and with pumps at 50 Hz operating speeds.
• Weights are for pumps fitted with Mechanical Seals and in Cast Iron materials
(tolerance ± 10%).
• The assemblies, Monoblock and with Baseplate, are suitable for 50 Hz motors,
except where other wise noted. Indicated total weights for the assemblies are
without motors.
• The installed motor size will cover the whole per formance cur ve when operating
as vacuum pump.
– 24 –
9.12 - PUMP ENGINEERING DATA
Table 8
dB(A)
lbs.
lbs.
lbs.
50 Hz
60 Hz
50 Hz
60 Hz
TRHE 32-4
67
30
42
70
1450
1750
0.55
0.75
TRHC 32-20
66
55
68
90
2900
3500
1.1
1.5
TRHE 32-20
66
40
50
75
2900
3500
1.1
1.5
TRHC 32-45
66
62
75
97
2900
3500
1.5
2.0
TRHE 32-45
66
46
56
81
2900
3500
1.5
2.0
TRHC 32-60
66
66
79
103
2900
3500
2.2
3
TRHE 32-60
66
57
68
95
2900
3500
2.2
3
TRHC 40-110
65
147
174
202
1450
1750
4
5
TRHE 40-110
65
108
134
160
1450
1750
4
5
TRHC 40-140
65
174
194
262
1450
1750
4
5
TRHE 40-140
65
147
167
220
1450
1750
4
5
TRHC 40-190
65
191
231
301
1450
1750
5.5
7.5
TRHE 40-190
65
165
205
260
1450
1750
5.5
7.5
TRHB 50-280
70
286
321
429
1450
1750
9
15
TRHB 50-340
70
308
374
466
1450
1750
11
15
TRHB 50-420
71
319
392
484
1450
1750
15
20
TRHC 80-600
76
484
539
792
1450
1750
22
30
TRHC 80-750
76
528
616
829
1450
1750
30
40
TRHE 100-870
79
906
—-
1263
960
1150
30
40
TRHE 100-1260
79
1067
—-
1434
960
1150
37
50
TRHE 100-1600
79
1140
—-
1518
960
1150
45
60
TRHA 150-2000
83
2926
—-
3971
730
880
75
100
TRHA 150-2600
84
3256
—-
4609
730
880
90
125
TRHA 150-3100
84
3586
—-
4939
730
880
110
150
TRSC 32-20
69
42
55
85
2900
3500
1.1
1.5
TRSE 32-20
69
32
45
68
2900
3500
1.1
1.5
TRSC 32-50
69
44
58
89
2900
3500
1.5
2.0
TRSE 32-50
69
38
47
73
2900
3500
1.5
2.0
TRSC 40-55
66
119
147
73
1450
1750
2.2
3
TRSE 40-55
66
75
103
130
1450
1750
2.2
3
TRSC 40-80
66
125
154
180
1450
1750
3
5.0
TRSE 40-80
66
81
110
136
1450
1750
3
5.0
TRSC 40-100
67
132
158
187
1450
1750
3
5.0
TRSE 40-100
67
86
114
141
1450
1750
3
5.0
TRSC 40-150
67
156
194
211
1450
1750
4
5.0
TRSE 40-150
67
97
125
152
1450
1750
4
5.0
TRSC 50-220
67
191
229
268
1450
1750
5.5
7.5
TRSE 50-220
67
162
202
240
1450
1750
5.5
7.5
TRSC 100-550
76
440
495
719
1450
1750
15
20
TRSC 100-700
76
506
561
836
1450
1750
18.5
30
TRSB 100-980
78
550
638
847
1450
1750
30
40
TRSE 125-1250
174
959
—-
596
960
1150
37
50
TRSE 125-1550
174
1016
—-
634
960
1150
45
60
TRSA 200-1950
183
2475
—-
1600
730
880
75
100
TRSA 200-2500
184
2695
—-
1700
730
880
75
100
TRSA 200-3100
184
2915
—-
1800
730
880
110
160
– 23 –
Noise
Level
Weight
Bare
Pump
Weight
assembly
Monoblock
(B5 design)
Weight
assembly
with
baseplate
Operating
Speed
RPM
Installed
Motor Size
kW
PUMP
MODEL
Noise
Level
Weight
assembly
Monoblock
50 Hz motor
Weight
assembly
Monoblock
60 Hz motor
Operating
Speed
RPM
Installed
Motor Size
kW
PUMP
MODEL
Noise
Level
Weight
Bare
Pump
Weight
assembly
Monoblock
(B5 design)
Weight
assembly
with
baseplate
Operating
Speed
RPM
Installed
Motor Size
kW
PUMP
MODEL
Noise
Level
Weight
assembly
Monoblock
50 Hz motor
Weight
assembly
Monoblock
60 Hz motor
Operating
Speed
RPM
Installed
Motor Size
kW
PUMP
MODEL